Fiber insulation, particularly fiberglass insulation, is a durable and long-lasting material commonly used in attics and walls. Its lifespan typically ranges from 80 to 100 years, making it a reliable choice for thermal and acoustic insulation. However, over time, even fiberglass insulation can degrade due to factors such as moisture, physical damage, or settling, which may reduce its effectiveness. Proper installation and maintenance can help maximize its lifespan and performance. Below, we explore the key factors influencing the longevity of fiber insulation, its degradation process, and how to ensure it remains effective over its lifespan.
Key Points Explained:
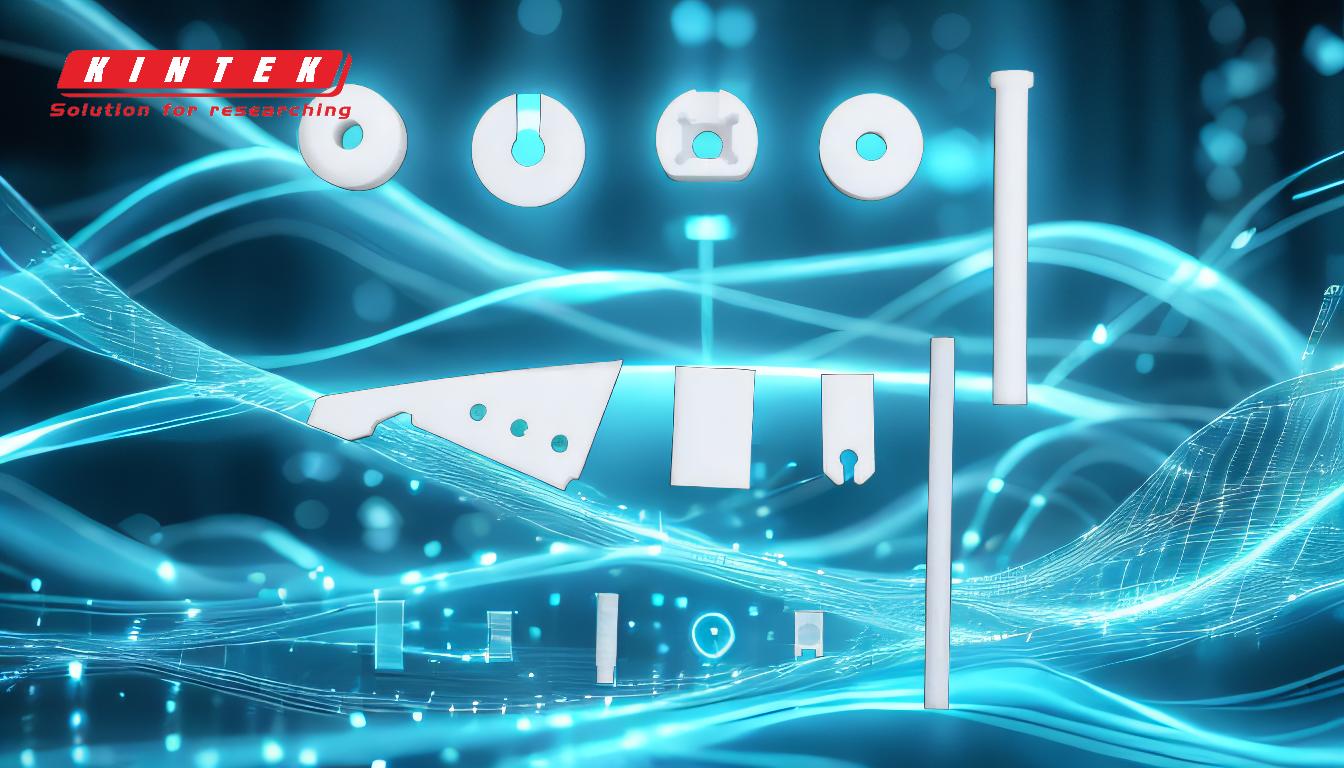
-
Lifespan of Fiber Insulation
- Fiberglass insulation, a common type of fiber insulation, has an estimated lifespan of 80 to 100 years.
- This longevity is due to its construction from natural materials like sand and recycled glass, which are inherently durable.
- Unlike some synthetic materials, fiberglass does not easily break down under normal conditions.
-
Factors Affecting Longevity
- Moisture Exposure: Prolonged exposure to moisture can cause fiber insulation to compress, mold, or lose its insulating properties.
- Physical Damage: Rodents, pests, or improper handling during renovations can tear or compress the insulation, reducing its effectiveness.
- Settling: Over time, fiber insulation may settle or compact, especially in vertical applications like walls, leading to gaps and reduced thermal performance.
- Environmental Conditions: Extreme temperatures, humidity, or exposure to UV light (in rare cases) can accelerate degradation.
-
Signs of Degradation
- Reduced Thermal Performance: If your heating or cooling bills increase unexpectedly, it may indicate that the insulation is no longer performing optimally.
- Visible Damage: Look for signs of compression, tears, or moisture stains on the insulation.
- Mold or Mildew Growth: This is a clear sign of moisture infiltration, which can compromise the insulation's effectiveness and pose health risks.
-
Maximizing Lifespan
- Proper Installation: Ensure the insulation is installed correctly, with no gaps or compression, to maintain its R-value (thermal resistance).
- Moisture Control: Use vapor barriers or ensure proper ventilation in areas like attics to prevent moisture buildup.
- Regular Inspections: Periodically check the insulation for signs of damage, settling, or pest activity, especially in older homes.
- Pest Prevention: Seal entry points and address any rodent or insect infestations promptly to protect the insulation.
-
When to Replace Fiber Insulation
- If the insulation is significantly compressed, torn, or contaminated with mold, it may need replacement.
- In cases where the insulation has settled and no longer provides adequate coverage, adding new layers or replacing it entirely may be necessary.
- Upgrading to newer insulation materials with higher R-values or better moisture resistance can also be a worthwhile investment.
-
Environmental and Economic Considerations
- Fiberglass insulation is recyclable, making it an environmentally friendly option.
- Its long lifespan reduces the need for frequent replacements, saving costs over time.
- However, if the insulation is damaged or no longer effective, replacing it can improve energy efficiency and reduce utility bills.
By understanding the factors that influence the lifespan of fiber insulation and taking proactive steps to maintain it, you can ensure that your insulation remains effective for decades. Regular inspections and addressing issues like moisture or pests promptly will help preserve its performance and extend its useful life.
Summary Table:
Key Aspect | Details |
---|---|
Lifespan | 80 to 100 years |
Factors Affecting Longevity | Moisture, physical damage, settling, environmental conditions |
Signs of Degradation | Reduced thermal performance, visible damage, mold growth |
Maintenance Tips | Proper installation, moisture control, regular inspections, pest prevention |
When to Replace | Significant compression, tears, mold contamination, or inadequate coverage |
Environmental Benefits | Recyclable, reduces frequent replacements, improves energy efficiency |
Ensure your insulation lasts for decades—contact our experts today for advice and solutions!