The lifespan of oil in a vacuum pump depends on several factors, including the type of pump, the application it is used for, and the operating conditions. Regular maintenance, such as oil changes, cleaning, and inspection, is crucial to ensure the pump operates efficiently. High and extremely-high vacuum pumps, like turbomolecular or ion getter pumps, have different maintenance requirements compared to rough and medium vacuum pumps. For oil-lubricated pumps, the oil should be checked and changed regularly to prevent contamination and wear. The exact duration between oil changes varies, but adhering to the manufacturer's guidelines and monitoring the oil's condition are key to maintaining optimal performance.
Key Points Explained:
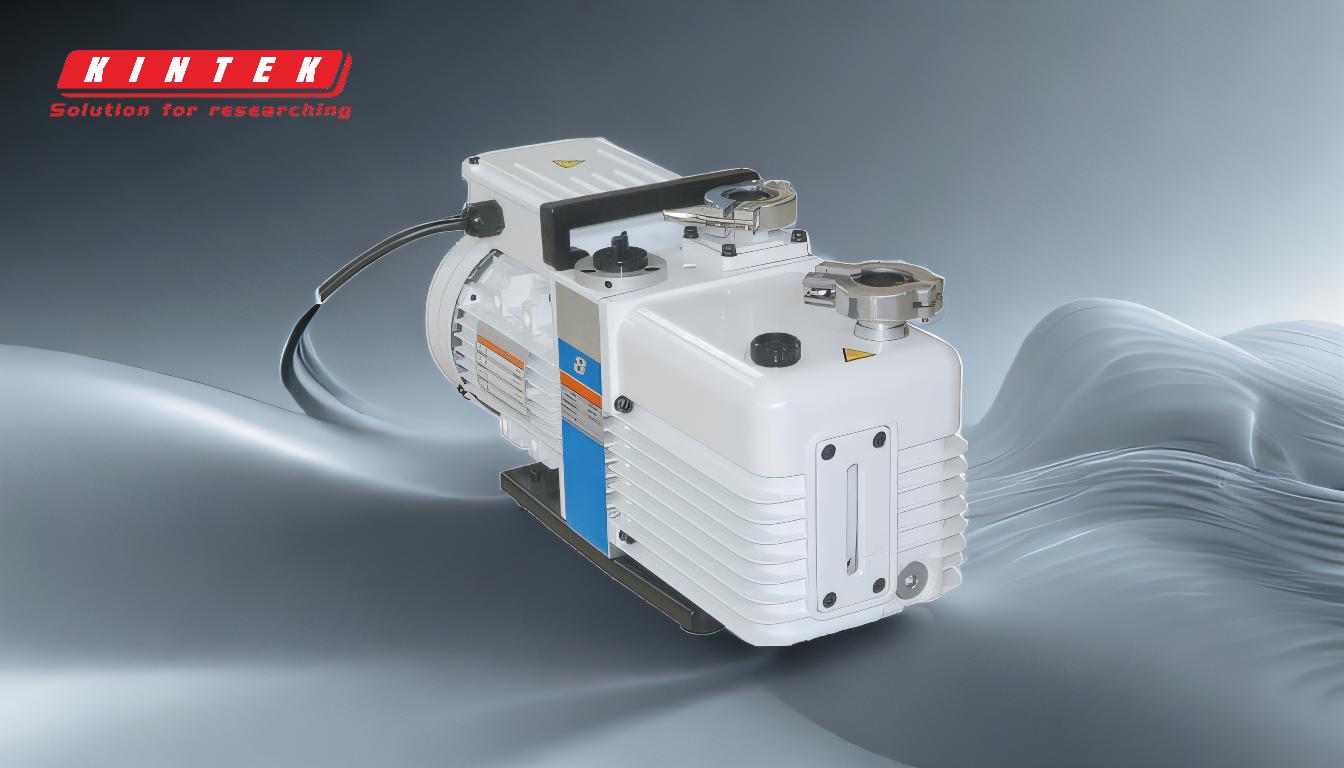
-
Factors Affecting Oil Lifespan:
- Type of Pump: Different vacuum pumps (e.g., rough, medium, high, or extremely-high vacuum pumps) have varying oil requirements. For example, oil-lubricated rotary vane pumps require more frequent oil changes compared to oil-free pumps like turbomolecular pumps.
- Application: The environment and materials being processed (e.g., corrosive gases, dust, or high temperatures) can accelerate oil degradation.
- Operating Conditions: Continuous operation, high temperatures, and exposure to contaminants can reduce the oil's lifespan.
-
Importance of Regular Oil Checks:
- Contamination Monitoring: Oil can become contaminated with dust, debris, or process by-products, reducing its effectiveness. Regular checks help identify when the oil needs to be replaced.
- Performance Maintenance: Clean oil ensures proper lubrication, reduces wear on components, and maintains the pump's efficiency.
-
Maintenance Practices:
- Oil Changes: Follow the manufacturer's recommendations for oil change intervals. For example, some pumps may require oil changes every 500-1000 hours of operation, while others may need it more or less frequently.
- Cleaning: Regularly clean the pump components to remove dust and debris that could contaminate the oil.
- Leak Inspection: Check for leaks that could lead to oil loss or contamination.
- Component Replacement: Replace worn-out parts, such as vanes or diaphragms, to prevent damage to the pump and contamination of the oil.
-
Special Considerations for High and Extremely-High Vacuum Pumps:
- These pumps often require specialized maintenance and may not use oil in the same way as rough or medium vacuum pumps. For example, turbomolecular pumps use bearings that may require specific lubrication schedules, while ion getter pumps are typically oil-free.
-
Monitoring Oil Condition:
- Visual Inspection: Check for changes in oil color or consistency, which may indicate contamination or degradation.
- Oil Analysis: In some cases, oil samples can be analyzed to assess its condition and determine if a change is needed.
By understanding these factors and adhering to proper maintenance practices, you can extend the lifespan of the oil in your vacuum pump and ensure reliable operation. Always refer to the manufacturer's guidelines for specific recommendations tailored to your pump and application.
Summary Table:
Key Factor | Details |
---|---|
Type of Pump | Oil-lubricated pumps (e.g., rotary vane) require more frequent oil changes. |
Application | Corrosive gases, dust, or high temperatures accelerate oil degradation. |
Operating Conditions | Continuous operation and high temperatures reduce oil lifespan. |
Maintenance Practices | Regular oil changes, cleaning, leak inspection, and component replacement. |
Monitoring Oil Condition | Visual inspection and oil analysis help determine when to change oil. |
Special Pumps | High/extremely-high vacuum pumps may require specialized maintenance. |
Ensure your vacuum pump operates at peak performance—contact our experts today for tailored maintenance advice!