Glass-lined reactors are a specialized type of reactor used in various industries, particularly in chemical and pharmaceutical applications. They are designed to handle corrosive materials and high-purity processes due to their glass lining, which provides excellent resistance to chemical attack. Based on the references provided, there are several ways to categorize glass-lined reactors, including their structural design, functionality, and specific applications. The main types include single-layer, double-layer, and three-layer glass reactors, as well as specialized types like jacketed glass reactors, hydrothermal synthesis reactors, and high-pressure reactors. Each type serves distinct purposes, from basic chemical reactions to complex, controlled-environment processes.
Key Points Explained:
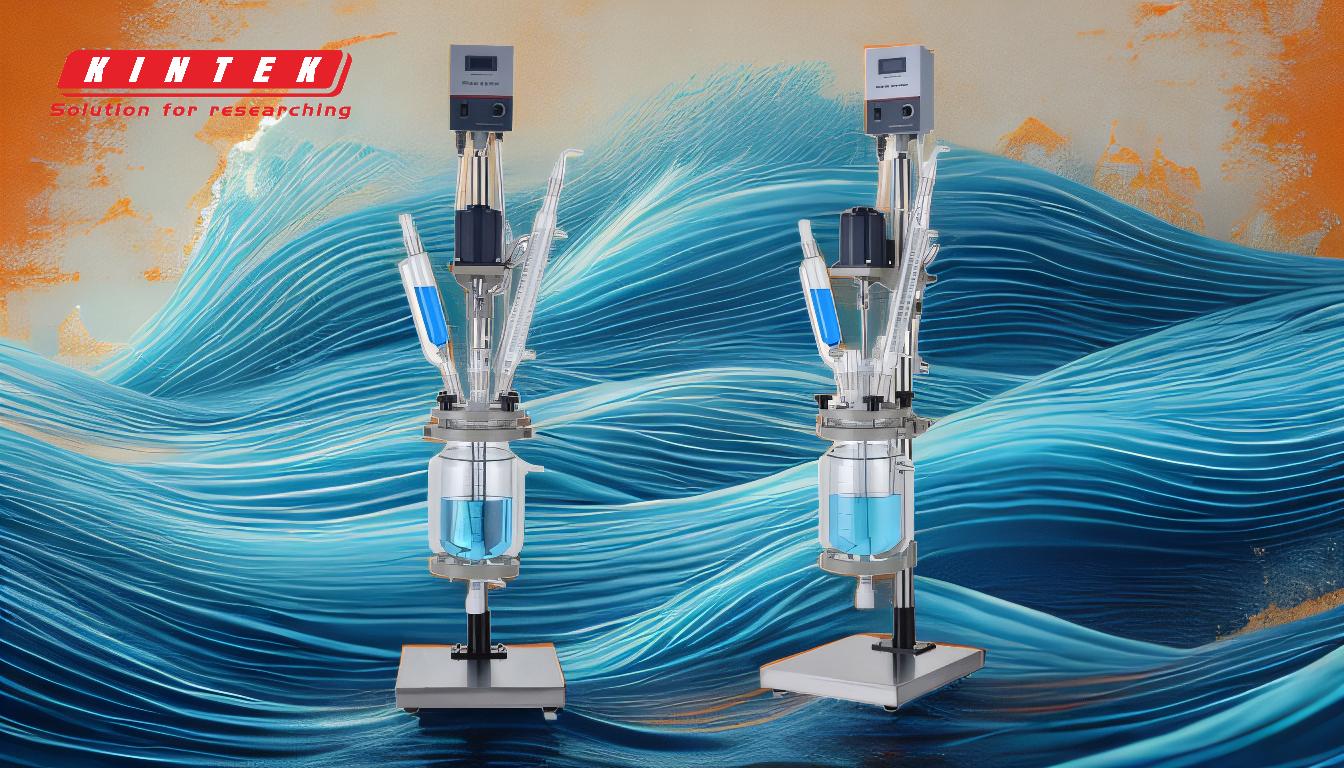
-
Single-Layer Glass Reactor:
- Description: This is the simplest form of glass-lined reactor, consisting of a single layer of glass lining the interior of the reactor.
- Applications: It is multifunctional and widely used in the chemical industry for processes that do not require precise temperature control or vacuum conditions.
- Advantages: Cost-effective, easy to maintain, and suitable for a wide range of chemical reactions.
- Limitations: Limited in handling processes that require thermal regulation or vacuum environments.
-
Double-Layer Glass Reactor:
- Description: This type features two layers, with the outer layer often used for temperature control (e.g., heating or cooling) and the inner layer for the reaction process.
- Applications: Commonly used in processes requiring controlled temperature environments, such as distillation, crystallization, and reflux.
- Advantages: Provides better temperature control compared to single-layer reactors, making it suitable for more complex reactions.
- Limitations: More expensive and complex to maintain than single-layer reactors.
-
Three-Layer Glass Reactor:
- Description: This advanced design includes three layers, offering enhanced insulation and temperature control capabilities.
- Applications: Ideal for highly sensitive reactions requiring precise thermal management, such as pharmaceutical synthesis.
- Advantages: Superior temperature control and insulation, suitable for high-purity processes.
- Limitations: Higher cost and maintenance requirements compared to single- and double-layer reactors.
-
Jacketed Glass Reactor:
- Description: A specialized type of reactor where the outer jacket allows for the circulation of heating or cooling fluids, enabling precise temperature control.
- Applications: Used in vacuum and temperature-controlled environments, such as chemical engineering and material synthesis.
- Advantages: Excellent for processes requiring strict temperature regulation and vacuum conditions.
- Limitations: More complex and expensive than standard reactors.
-
Hydrothermal Synthesis Reactor:
- Description: Designed for high-pressure and high-temperature reactions, often used in material science and nanotechnology.
- Applications: Suitable for synthesizing nanomaterials, crystals, and other advanced materials.
- Advantages: Capable of handling extreme conditions, making it ideal for specialized research and industrial applications.
- Limitations: Requires specialized equipment and safety measures due to high-pressure operations.
-
Stirring Magnetic Reactor:
- Description: Equipped with a magnetic stirring mechanism, this type of reactor ensures uniform mixing of reactants.
- Applications: Used in processes where consistent mixing is critical, such as polymer synthesis and emulsion preparation.
- Advantages: Provides efficient mixing without the need for mechanical seals, reducing contamination risks.
- Limitations: Limited to processes where magnetic stirring is sufficient; not suitable for highly viscous materials.
-
Electric Heating Reactor:
- Description: Utilizes electric heating elements for temperature control, offering precise and rapid heating.
- Applications: Common in small-scale laboratory settings and processes requiring quick temperature adjustments.
- Advantages: Fast and precise heating, easy to control, and suitable for small-scale applications.
- Limitations: Higher energy consumption and less suitable for large-scale industrial processes.
-
Steam Reactor:
- Description: Uses steam as a heating medium, often integrated into larger industrial systems.
- Applications: Suitable for large-scale chemical processes, such as petrochemical refining and bulk chemical production.
- Advantages: Efficient for large-scale operations, with steam being a readily available and cost-effective heating medium.
- Limitations: Requires a steam supply system, making it less flexible for small-scale or laboratory use.
-
High-Pressure Reactor:
- Description: Designed to withstand high-pressure conditions, often used in processes like hydrogenation and polymerization.
- Applications: Critical in industries requiring high-pressure reactions, such as petrochemicals and advanced materials.
- Advantages: Capable of handling extreme pressure conditions, enabling unique chemical processes.
- Limitations: Requires specialized safety measures and equipment, increasing complexity and cost.
In summary, the choice of glass-lined reactor depends on the specific requirements of the process, including temperature control, pressure conditions, and the nature of the reactants. Each type offers unique advantages and limitations, making it essential to select the appropriate reactor based on the intended application.
Summary Table:
Type | Description | Applications | Advantages | Limitations |
---|---|---|---|---|
Single-Layer | Simplest design with a single glass lining | Chemical industry processes without precise temperature control | Cost-effective, easy to maintain | Limited thermal regulation and vacuum handling |
Double-Layer | Two layers for temperature control and reaction process | Distillation, crystallization, reflux | Better temperature control | More expensive and complex to maintain |
Three-Layer | Advanced design with three layers for enhanced insulation and temperature control | Pharmaceutical synthesis, high-purity processes | Superior temperature control and insulation | Higher cost and maintenance |
Jacketed Glass | Outer jacket for heating/cooling fluid circulation | Vacuum and temperature-controlled environments | Excellent temperature regulation and vacuum handling | More complex and expensive |
Hydrothermal Synthesis | Designed for high-pressure and high-temperature reactions | Nanomaterial synthesis, crystal growth | Handles extreme conditions | Requires specialized equipment and safety measures |
Stirring Magnetic | Magnetic stirring mechanism for uniform mixing | Polymer synthesis, emulsion preparation | Efficient mixing, reduces contamination risks | Limited to low-viscosity materials |
Electric Heating | Uses electric heating elements for precise temperature control | Small-scale laboratory processes | Fast and precise heating | Higher energy consumption, less suitable for large-scale processes |
Steam Reactor | Utilizes steam as a heating medium | Petrochemical refining, bulk chemical production | Efficient for large-scale operations | Requires steam supply system, less flexible for small-scale use |
High-Pressure | Designed for high-pressure conditions | Hydrogenation, polymerization | Handles extreme pressure conditions | Requires specialized safety measures and equipment |
Need help selecting the right glass-lined reactor for your needs? Contact our experts today for personalized guidance!