Sputter deposition is a physical vapor deposition (PVD) technique used to deposit thin films of material onto a substrate, such as a silicon wafer. The process involves bombarding a target material with high-energy ions, typically from an inert gas like argon, in a vacuum chamber. These ions dislodge atoms from the target, which then travel through the gas and deposit onto the substrate, forming a thin, uniform film. The method is widely used in industries like semiconductors, optics, and coatings due to its ability to produce high-quality, adherent films with precise control over thickness and composition.
Key Points Explained:
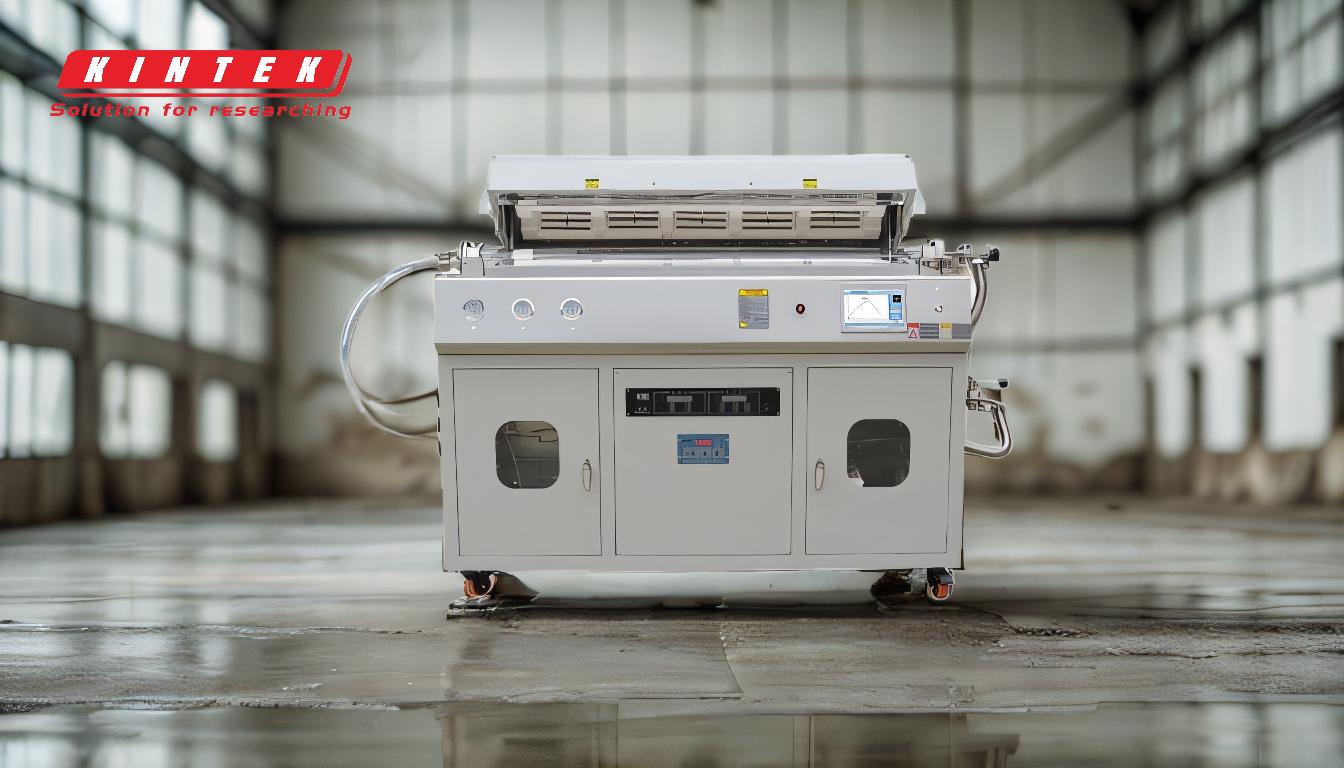
-
Introduction to Sputter Deposition:
- Sputter deposition is a type of physical vapor deposition (PVD) used to create thin films on substrates.
- It is a non-thermal process that relies on the ejection of atoms from a solid target material due to bombardment by high-energy ions.
-
Components of the Sputter Deposition System:
- Target Material: The source material from which atoms are ejected. It is typically a pure metal or compound.
- Substrate: The surface onto which the ejected atoms are deposited, such as a silicon wafer or glass.
- Vacuum Chamber: A controlled environment where the process occurs, ensuring minimal contamination and precise deposition.
- Inert Gas (Argon): Used to create a plasma that bombards the target material.
- Cathode and Anode: The target is connected to a negatively charged cathode, while the substrate is connected to a positively charged anode, facilitating the deposition process.
-
The Sputtering Process:
- Creation of Plasma: Argon gas is introduced into the vacuum chamber and ionized to form a plasma. This plasma consists of positively charged argon ions and free electrons.
- Bombardment of Target: The argon ions are accelerated toward the negatively charged target material due to the electric field. Upon impact, they dislodge atoms from the target through a process called sputtering.
- Ejection of Target Atoms: The ejected atoms from the target material are neutral and travel through the vacuum chamber in a random direction.
- Deposition on Substrate: These atoms eventually collide with and adhere to the substrate, forming a thin film. The process is controlled by opening and closing a shutter to expose the substrate to the ejected atoms.
-
Advantages of Sputter Deposition:
- High Adhesion: The high energy of the sputtered atoms ensures strong adhesion to the substrate, making the films more durable.
- Uniformity: Sputter deposition produces highly uniform films, even on complex geometries.
- Versatility: It can deposit a wide range of materials, including metals, alloys, and compounds.
- Precision: The process allows for precise control over film thickness and composition, making it ideal for applications requiring high accuracy.
-
Applications of Sputter Deposition:
- Semiconductor Industry: Used to deposit thin films of metals and dielectrics on silicon wafers for integrated circuits.
- Optics: Applied in the production of anti-reflective coatings, mirrors, and optical filters.
- Decorative Coatings: Used to create durable and aesthetically pleasing coatings on consumer products.
- Magnetic Storage: Essential for depositing thin magnetic films in hard disk drives.
-
Comparison with Other Deposition Techniques:
- Thermal Evaporation: Unlike sputter deposition, thermal evaporation relies on heating the source material to vaporize it. Sputter deposition offers better adhesion and uniformity, especially for high-melting-point materials.
- Chemical Vapor Deposition (CVD): CVD involves chemical reactions to deposit films, whereas sputter deposition is a purely physical process. Sputter deposition is often preferred for its simplicity and ability to deposit pure materials without chemical byproducts.
-
Challenges and Considerations:
- Contamination: The vacuum environment must be carefully maintained to avoid contamination from residual gases.
- Target Erosion: Continuous bombardment can erode the target material, requiring periodic replacement.
- Energy Efficiency: The process can be energy-intensive, especially for large-scale applications.
In summary, sputter deposition is a versatile and precise method for depositing thin films, widely used in various industries due to its ability to produce high-quality, adherent coatings. The process involves creating a plasma, bombarding a target material to eject atoms, and depositing them onto a substrate in a controlled vacuum environment. Its advantages include high adhesion, uniformity, and versatility, making it a preferred choice for many applications.
Summary Table:
Aspect | Details |
---|---|
Process | Physical vapor deposition (PVD) using high-energy ions to eject target atoms. |
Key Components | Target material, substrate, vacuum chamber, inert gas (argon), cathode/anode. |
Advantages | High adhesion, uniformity, versatility, and precise control over film properties. |
Applications | Semiconductors, optics, decorative coatings, and magnetic storage. |
Comparison | Better adhesion and uniformity than thermal evaporation; simpler than CVD. |
Challenges | Contamination risks, target erosion, and energy-intensive processes. |
Discover how sputter deposition can enhance your projects—contact our experts today!