Designing a bioreactor involves a systematic approach to ensure it meets the specific requirements of the biological process it will support. A bioreactor is a controlled environment where biological or biochemical processes are carried out, often involving microorganisms, cells, or enzymes. The design process includes selecting the appropriate type of bioreactor, determining its size and configuration, and incorporating features for monitoring and controlling critical parameters such as temperature, pH, oxygen levels, and agitation. The goal is to optimize the growth conditions for the organisms or cells, maximize productivity, and ensure scalability for industrial applications.
Key Points Explained:
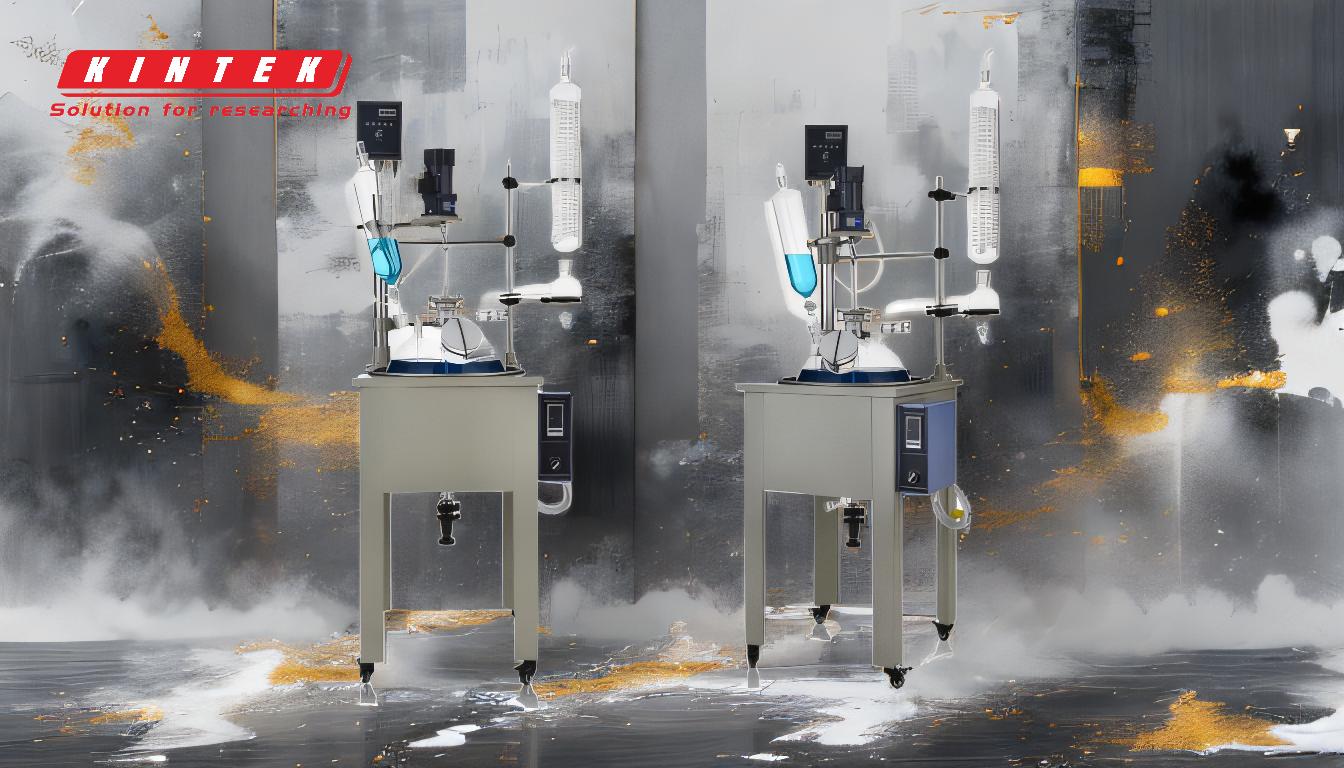
-
Define the Purpose and Requirements:
- Objective: Clearly define the biological process (e.g., fermentation, cell culture, enzyme production) and the desired outcomes (e.g., biomass production, metabolite synthesis).
- Scale: Determine whether the bioreactor is for laboratory-scale research, pilot-scale testing, or full-scale industrial production.
- Organism/Cell Type: Identify the specific organism or cell type to be used, as different organisms have unique growth requirements.
- Product: Specify the end product (e.g., proteins, biofuels, pharmaceuticals) and its purity requirements.
-
Select the Type of Bioreactor:
- Stirred-Tank Bioreactor: Commonly used for its versatility and ability to provide good mixing and oxygen transfer. Suitable for aerobic processes.
- Airlift Bioreactor: Uses air or gas to mix and aerate the culture. Ideal for shear-sensitive cells and processes requiring low energy input.
- Packed-Bed Bioreactor: Contains immobilized cells or enzymes on a solid support. Suitable for continuous processes and high cell density cultures.
- Membrane Bioreactor: Combines a bioreactor with a membrane filtration system, often used in wastewater treatment and for separating cells from the product.
- Photobioreactor: Designed for photosynthetic organisms, such as algae, with controlled light exposure.
-
Determine the Size and Configuration:
- Volume: Calculate the working volume based on the required production scale. Consider the headspace for gas exchange and foam control.
- Aspect Ratio: Choose the height-to-diameter ratio, which affects mixing efficiency, oxygen transfer, and heat dissipation.
- Material: Select materials that are biocompatible, corrosion-resistant, and easy to sterilize (e.g., stainless steel, glass, or specialized plastics).
- Ports and Connections: Include ports for sampling, feeding, gas exchange, and sensor integration.
-
Design the Agitation and Aeration System:
- Agitation: Design the impeller system to ensure uniform mixing and prevent cell settling. Consider the type of impeller (e.g., Rushton turbine, marine propeller) and its speed.
- Aeration: Ensure adequate oxygen supply for aerobic processes. Design spargers or diffusers to distribute gas evenly and minimize shear stress on cells.
- Oxygen Transfer Rate (OTR): Calculate the OTR to meet the metabolic demands of the organisms or cells. Optimize the agitation and aeration system to achieve the desired OTR.
-
Incorporate Monitoring and Control Systems:
- Sensors: Integrate sensors for real-time monitoring of critical parameters such as temperature, pH, dissolved oxygen (DO), and pressure.
- Control Systems: Implement automated control systems to maintain optimal conditions. Use feedback loops to adjust parameters like agitation speed, gas flow rate, and cooling/heating.
- Data Logging: Include data logging capabilities for process optimization and regulatory compliance.
-
Ensure Sterility and Contamination Control:
- Sterilization: Design the bioreactor to withstand sterilization methods such as autoclaving, steam-in-place (SIP), or chemical sterilization.
- Sealing: Use high-quality seals and gaskets to prevent contamination. Ensure all connections are leak-proof.
- Air Filtration: Install HEPA filters or other air filtration systems to maintain a sterile environment.
-
Optimize for Scalability and Flexibility:
- Modular Design: Consider a modular design that allows for easy scaling up or down. This is particularly important for transitioning from lab-scale to industrial-scale production.
- Flexibility: Design the bioreactor to accommodate different processes or organisms, allowing for flexibility in research and production.
-
Consider Energy Efficiency and Cost:
- Energy Consumption: Optimize the design to minimize energy consumption, particularly in agitation and aeration systems.
- Cost-Effectiveness: Balance the cost of materials and components with the performance requirements. Consider the total cost of ownership, including maintenance and operational costs.
-
Validate and Test the Design:
- Prototype Testing: Build and test a prototype to validate the design. Conduct experiments to ensure the bioreactor meets the desired performance criteria.
- Process Optimization: Use the prototype to optimize the process parameters, such as agitation speed, aeration rate, and nutrient feeding strategies.
- Regulatory Compliance: Ensure the design complies with relevant regulatory standards, particularly for applications in pharmaceuticals and food production.
-
Document and Iterate:
- Documentation: Maintain detailed documentation of the design process, including calculations, material specifications, and test results.
- Iteration: Use feedback from testing to refine the design. Iterate as necessary to improve performance, scalability, and cost-effectiveness.
By following these steps, you can design a bioreactor that is well-suited to your specific biological process, ensuring optimal performance, scalability, and regulatory compliance.
Summary Table:
Step | Key Considerations |
---|---|
1. Define Purpose & Requirements | Objective, scale, organism/cell type, product specifications |
2. Select Bioreactor Type | Stirred-tank, airlift, packed-bed, membrane, or photobioreactor |
3. Determine Size & Configuration | Volume, aspect ratio, material, ports, and connections |
4. Design Agitation & Aeration | Impeller type, spargers, oxygen transfer rate (OTR) |
5. Incorporate Monitoring Systems | Sensors for temperature, pH, DO, pressure; automated control systems |
6. Ensure Sterility | Sterilization methods, sealing, air filtration |
7. Optimize Scalability | Modular design, flexibility for different processes |
8. Consider Energy & Cost | Energy efficiency, cost-effectiveness, total cost of ownership |
9. Validate & Test | Prototype testing, process optimization, regulatory compliance |
10. Document & Iterate | Detailed documentation, iterative design improvements |
Ready to design a bioreactor tailored to your needs? Contact our experts today for personalized guidance!