Continuous flow reactors are widely used in industrial and laboratory settings due to their efficiency, scalability, and ability to handle continuous reactant flow. They offer advantages such as reduced material usage, lower costs, and higher yields compared to batch reactors. Examples of continuous flow reactors include Plug Flow Reactors (PFRs), Continuous Stirred-Tank Reactors (CSTRs), Loop Reactors, and Catalytic Reactors. Each type has unique characteristics and applications, making them suitable for different chemical processes. These reactors are particularly advantageous for high-volume production and processes requiring precise control over reaction conditions.
Key Points Explained:
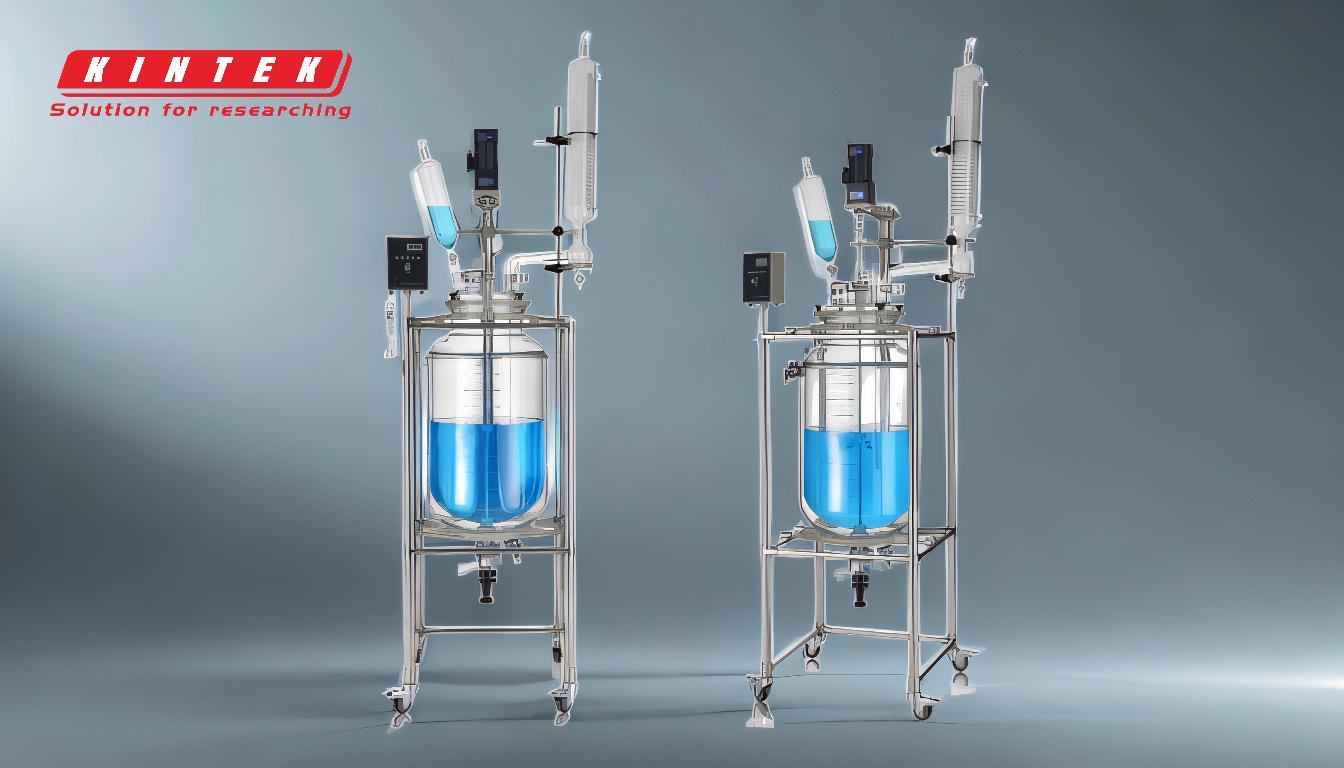
-
Plug Flow Reactor (PFR):
- Description: A PFR is a tubular reactor where reactants flow continuously through a pipe, and the reaction occurs as the materials move along the length of the reactor.
-
Advantages:
- High conversion rates due to minimal back-mixing.
- Ideal for reactions requiring precise control of residence time.
- Suitable for gas-phase reactions and large-scale production.
- Applications: Used in petroleum refining, polymerization, and chemical synthesis.
-
Continuous Stirred-Tank Reactor (CSTR):
- Description: A CSTR consists of a tank with an agitator that ensures uniform mixing of reactants. Reactants are continuously fed into the tank, and products are continuously removed.
-
Advantages:
- Uniform temperature and concentration throughout the reactor.
- Easy to scale up for industrial applications.
- Suitable for liquid-phase reactions and processes requiring steady-state operation.
- Applications: Commonly used in fermentation, wastewater treatment, and chemical manufacturing.
-
Loop Reactor:
- Description: A loop reactor is a closed-loop system where reactants circulate through a loop, often with a pump or agitator to maintain flow and mixing.
-
Advantages:
- Efficient heat and mass transfer due to continuous circulation.
- Compact design compared to traditional reactors.
- Suitable for highly exothermic or endothermic reactions.
- Applications: Used in polymerization processes, hydrogenation, and catalytic reactions.
-
Catalytic Reactor:
- Description: Catalytic reactors are designed to facilitate reactions using catalysts, which are often packed in beds or coated on surfaces within the reactor.
-
Advantages:
- Enhanced reaction rates and selectivity due to the presence of catalysts.
- Can operate at lower temperatures and pressures, reducing energy costs.
- Suitable for gas-phase and liquid-phase reactions.
- Applications: Widely used in petrochemical industries, ammonia synthesis, and environmental catalysis.
-
General Advantages of Continuous Flow Reactors:
- Efficiency: Continuous flow reactors are more efficient than batch reactors, as they allow for continuous processing without downtime.
- Scalability: They are easily scalable for industrial production, making them ideal for high-volume manufacturing.
- Cost-Effectiveness: Reduced material usage and lower manufacturing costs contribute to overall cost savings.
- Flexibility: These reactors can handle a wide range of reaction conditions, including variations in temperature, pressure, and reactant types.
-
Comparison with Batch Reactors:
-
Continuous Flow Reactors:
- Better suited for high-volume production.
- Offer higher yields and lower manufacturing costs.
- Require less manual intervention and are more automated.
-
Batch Reactors:
- Preferred for small-scale or specialized processes.
- Easier to fabricate and can save on initial setup costs.
- More versatile for processes requiring frequent changes in reaction conditions.
-
Continuous Flow Reactors:
-
Industrial Applications:
- Continuous flow reactors are widely used in industries such as pharmaceuticals, petrochemicals, food processing, and environmental engineering.
- They are particularly valuable in processes requiring consistent product quality and high throughput.
In summary, continuous flow reactors, including PFRs, CSTRs, Loop Reactors, and Catalytic Reactors, are essential tools in modern chemical engineering. Their ability to handle continuous processes, coupled with their efficiency and scalability, makes them superior to batch reactors in many industrial applications. However, the choice between continuous flow and batch reactors ultimately depends on the specific requirements of the process, including production volume, reaction conditions, and cost considerations.
Summary Table:
Reactor Type | Key Advantages | Applications |
---|---|---|
Plug Flow Reactor (PFR) | High conversion rates, precise residence time control, ideal for gas-phase reactions | Petroleum refining, polymerization, chemical synthesis |
CSTR | Uniform mixing, easy scalability, steady-state operation | Fermentation, wastewater treatment, chemical manufacturing |
Loop Reactor | Efficient heat/mass transfer, compact design, suitable for exothermic/endothermic reactions | Polymerization, hydrogenation, catalytic reactions |
Catalytic Reactor | Enhanced reaction rates, lower energy costs, operates at lower temperatures/pressures | Petrochemicals, ammonia synthesis, environmental catalysis |
General Advantages | Efficiency, scalability, cost-effectiveness, flexibility | High-volume production, precise reaction control, consistent product quality |
Ready to optimize your chemical processes with continuous flow reactors? Contact our experts today for tailored solutions!