Sputtering targets are specialized materials used in the sputtering process, a form of physical vapor deposition (PVD), to create thin films on substrates. These targets are typically made of metallic elements, alloys, or ceramics, and are available in various forms such as discs or sheets. The sputtering process involves bombarding the target material with ions, causing atoms to be ejected and deposited onto a substrate, forming a thin film. The choice of sputtering target material depends on the desired properties of the thin film, such as conductivity, hardness, or aesthetic appeal. Common materials include tantalum for semiconductors, titanium for wear-resistant coatings, and gold for decorative purposes. The process is widely used in industries like electronics, solar energy, and tool manufacturing.
Key Points Explained:
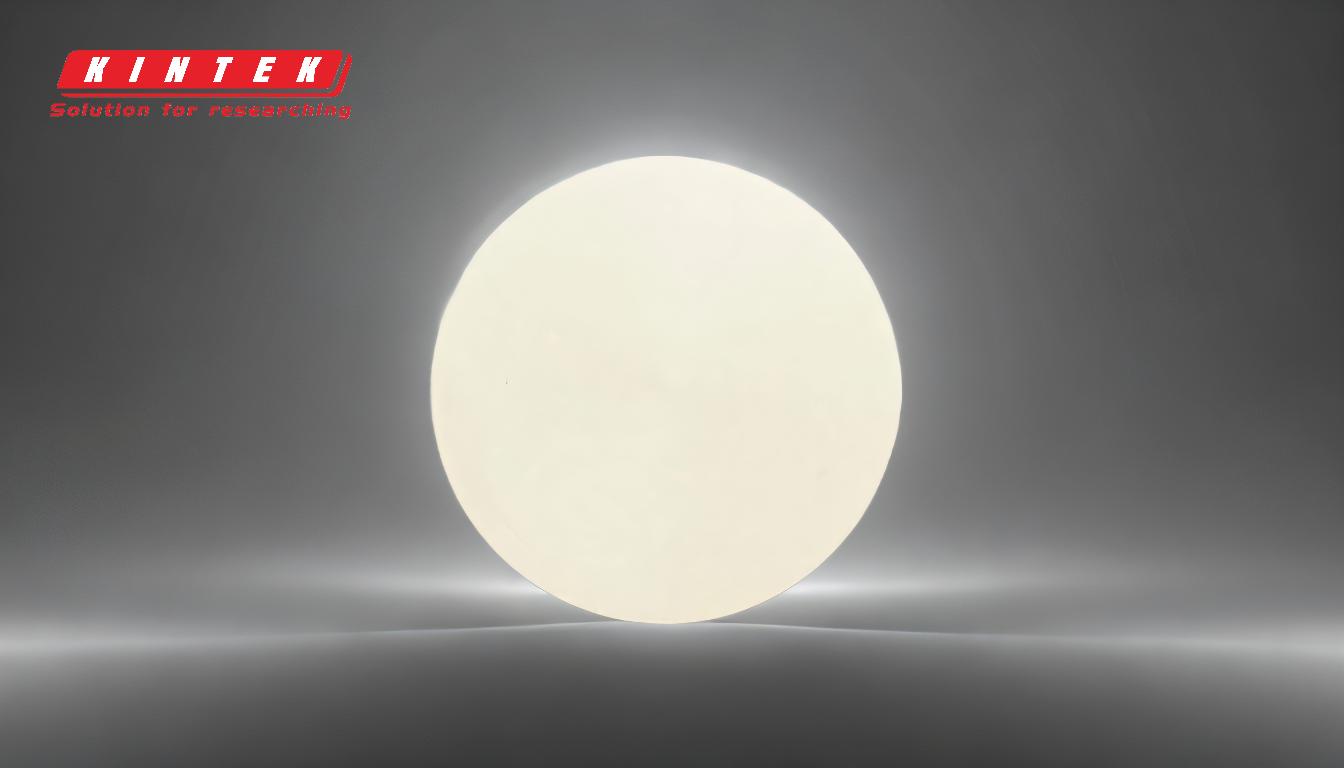
-
Definition of Sputtering Targets:
- Sputtering targets are solid materials, often in the form of discs or sheets, used in the sputtering process to deposit thin films onto substrates.
- They can be made from a variety of materials, including pure metals, alloys, and ceramics.
-
Materials Used in Sputtering Targets:
- Metallic Elements: Common metals include tantalum, niobium, titanium, tungsten, molybdenum, hafnium, and silicon.
- Alloys: Examples include gold-palladium and platinum.
- Ceramics: Used for creating hardened thin coatings, often for tools.
-
Applications of Sputtering Targets:
- Semiconductors: Tantalum and hafnium are used in semiconductor production.
- Electronics: Niobium is utilized in electronic components.
- Wear-Resistant Coatings: Titanium is chosen for its durability and aesthetic properties.
- Decorative Coatings: Tungsten and gold are used for their visual appeal.
- Solar Panels: Molybdenum and silicon are key materials in solar cell production.
-
Sputtering Process:
- The process involves bombarding the target material with ions, causing atoms to be ejected from the surface.
- These ejected atoms form a spray that coats the substrate, creating a thin film.
- The quality of the film can be influenced by factors such as the vacuum level and the choice of target material.
-
Advantages of Different Materials:
- Gold: Commonly used for its excellent conductivity and aesthetic properties.
- Chromium: Requires better vacuums but allows for finer grain size and thinner coatings.
- Ceramics: Provide hardened coatings, ideal for tools requiring durability.
-
Selection Criteria for Sputtering Targets:
- The choice of material depends on the specific application and the desired properties of the thin film.
- Factors to consider include conductivity, hardness, aesthetic qualities, and the specific requirements of the substrate.
-
Industrial Relevance:
- Sputtering targets are crucial in various industries, including electronics, solar energy, and tool manufacturing.
- They enable the production of high-quality thin films with precise properties, essential for advanced technological applications.
In summary, sputtering targets are essential components in the thin film deposition process, with a wide range of materials available to meet the diverse needs of different industries. The selection of the appropriate target material is critical to achieving the desired film properties, making sputtering targets a key element in modern manufacturing and technology.
Summary Table:
Category | Details |
---|---|
Definition | Solid materials (discs/sheets) used in sputtering to deposit thin films. |
Materials | Metals (tantalum, titanium), alloys (gold-palladium), ceramics. |
Applications | Semiconductors, electronics, wear-resistant coatings, solar panels. |
Process | Bombarding target with ions to eject atoms, forming a thin film on substrate. |
Key Advantages | Conductivity (gold), durability (ceramics), aesthetic appeal (tungsten). |
Selection Criteria | Conductivity, hardness, aesthetic qualities, substrate requirements. |
Industrial Relevance | Electronics, solar energy, tool manufacturing. |
Discover how sputtering targets can enhance your thin film processes—contact our experts today!