RF sputtering is a highly advantageous thin-film deposition technique, particularly for insulating and semiconductor materials. It operates at lower pressures, reducing particle collisions and enabling higher sputtering rates compared to DC sputtering. This method minimizes substrate heating, prevents charge buildup, and reduces "Race Track Erosion," extending target lifetimes. RF sputtering also allows for better film densification, smoother coatings, and improved adhesion due to the high energy of sputtered atoms. Additionally, it supports a wide range of target materials, including low-melting-point and poorly conductive substances, making it versatile for various applications in electronics, optics, and materials science.
Key Points Explained:
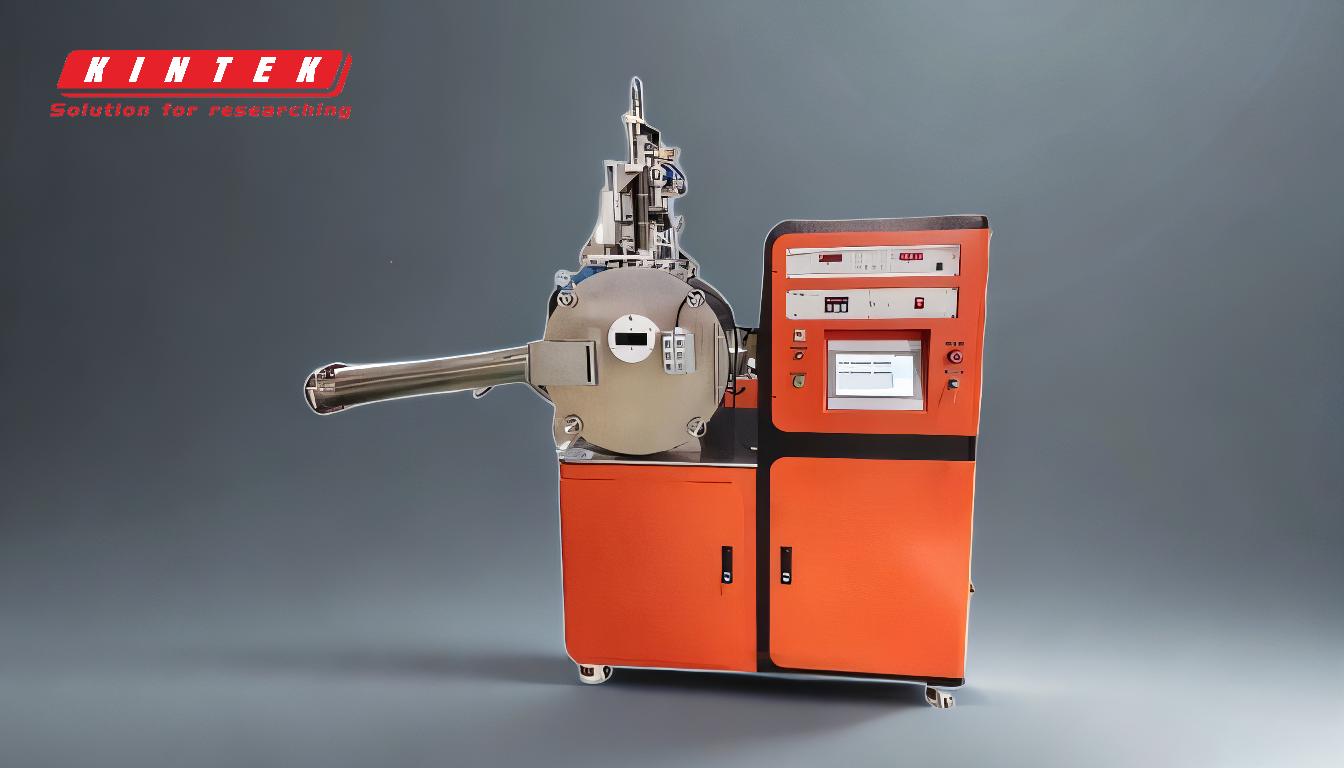
-
Ability to Sputter Insulating and Semiconductor Materials:
- RF sputtering excels in depositing thin films of insulators (e.g., aluminum oxide, boron nitride) and semiconductors, which are challenging for DC sputtering due to charge buildup on insulating targets.
- The use of radio waves instead of direct current prevents surface charging, enabling consistent and high-quality deposition.
-
Lower Substrate Heating:
- RF sputtering generates less heat on the substrate compared to DC sputtering, making it suitable for temperature-sensitive materials.
- This is particularly beneficial for applications requiring low or medium-temperature deposition, such as in microelectronics or flexible substrates.
-
Higher Sputtering Rates:
- The oscillating electrons in RF plasma result in a sputtering rate approximately 10 times higher than DC sputtering at the same chamber pressure.
- This efficiency allows for faster deposition of thin films with controlled microstructures.
-
Operation at Lower Pressures:
- RF sputtering operates at pressures below 15 mTorr, compared to DC sputtering's typical 100 mTorr.
- Lower pressure reduces collisions between target material particles and gas ions, creating a more direct pathway for particles to reach the substrate and improving film quality.
-
Reduced Charge Buildup and Plasma Arcing:
- The alternating electric field in RF sputtering eliminates charge buildup on the cathode surface, preventing plasma arcing.
- This results in smoother, higher-quality layers and reduces defects in the deposited films.
-
Extended Target Lifetime:
- RF sputtering involves a larger surface area of the target in the sputtering process, reducing localized erosion (e.g., "Race Track Erosion").
- This extends the target's usable lifetime, lowering operational costs.
-
Versatility in Target Materials:
- RF sputtering supports a wide range of target materials, including metals, semiconductors, insulators, and compounds.
- It is particularly effective for materials with low melting points or poor electrical conductivity, which are difficult to process using other methods.
-
Improved Film Properties:
- RF sputtering produces films with better densification, fewer pinholes, and higher purity due to the absence of evaporation source contamination.
- The high energy of sputtered atoms enhances adhesion between the film and substrate, forming a diffusion layer for stronger bonding.
-
Precise Thickness Control and Uniformity:
- Film thickness can be precisely controlled by adjusting the target current, ensuring reproducibility and uniformity.
- RF sputtering enables the deposition of uniform films over large areas, making it ideal for industrial-scale applications.
-
Environmental and Process Advantages:
- RF sputtering is an environmentally friendly method, as it operates in a vacuum and minimizes waste.
- It allows for the deposition of small quantities of oxides, metals, and alloys on various substrates, making it versatile for research and production.
By leveraging these advantages, RF sputtering is a preferred method for applications requiring high-quality thin films, such as in semiconductor manufacturing, optical coatings, and advanced materials research. Its ability to handle diverse materials, combined with precise control over film properties, makes it a cornerstone of modern thin-film technology.
Summary Table:
Advantage | Description |
---|---|
Sputters Insulating Materials | Ideal for insulators and semiconductors, preventing charge buildup. |
Lower Substrate Heating | Minimizes heat, suitable for temperature-sensitive materials. |
Higher Sputtering Rates | 10x faster than DC sputtering, enabling efficient thin-film deposition. |
Operation at Lower Pressures | Reduces particle collisions, improving film quality. |
Reduced Charge Buildup | Prevents plasma arcing, ensuring smoother layers. |
Extended Target Lifetime | Reduces localized erosion, lowering operational costs. |
Versatile Target Materials | Supports metals, insulators, and low-melting-point materials. |
Improved Film Properties | Better densification, fewer pinholes, and enhanced adhesion. |
Precise Thickness Control | Ensures uniformity and reproducibility for industrial applications. |
Environmental Benefits | Operates in a vacuum, minimizing waste and contamination. |
Unlock the potential of RF sputtering for your thin-film applications—contact our experts today!