Sputtering is a versatile and widely used process with applications across multiple industries. It is primarily employed for thin-film deposition, enabling the creation of precise, high-quality coatings on various substrates. Key applications include the production of computer hard disks, integrated circuits, optical coatings, and durable tool coatings. Additionally, sputtering is utilized in the semiconductor industry, photovoltaic solar cell manufacturing, and the production of CDs, DVDs, and anti-reflective glass. Its ability to deposit thin films of metals, alloys, and other materials makes it essential for advancing technology and improving product performance in fields such as electronics, optics, and renewable energy.
Key Points Explained:
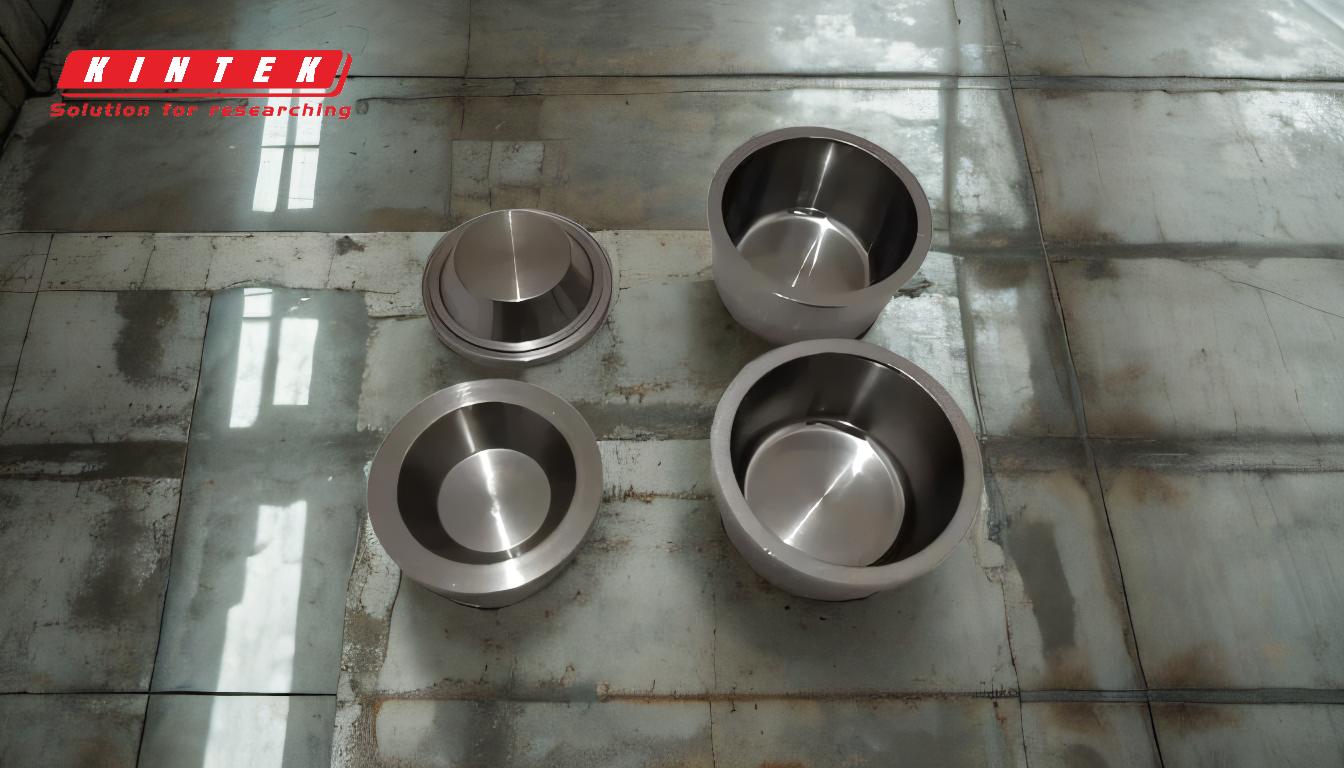
-
Thin-Film Deposition:
- Sputtering is a high-vacuum-based coating technique used in Physical Vapor Deposition (PVD) processes.
- It deposits thin films ranging from a few nanometers to micrometers in thickness on substrates.
- Applications include creating anti-reflective coatings on glass, low-emissivity coatings on double-pane windows, and metalizing plastics.
-
Semiconductor Industry:
- Sputtering is extensively used in integrated circuit (IC) processing to deposit thin films of various materials.
- It plays a critical role in manufacturing semiconductors, enabling the precise layering of conductive and insulating materials.
-
Data Storage:
- One of the earliest and most important applications of sputtering is in the production of computer hard disks.
- It is also used in the fabrication of CDs and DVDs, where thin metal layers are deposited to store data.
-
Optical Applications:
- Sputtering is used to create optical coatings, such as anti-reflective films on glass and lenses.
- It is also employed in manufacturing optical waveguides and photovoltaic solar cells, enhancing their efficiency and performance.
-
Durable Coatings:
- The process is used to coat cutting tools with nitrides, increasing their hardness and wear resistance.
- It is also applied in the automotive industry for anodizing aluminum wheels and cookware, providing a uniform, shiny surface and resistance to food sticking.
-
Surface Physics and Analysis:
- Sputtering is used as a cleaning method to prepare high-purity surfaces for research and industrial applications.
- It is also a technique for analyzing the chemical composition of surfaces, aiding in material characterization.
-
Advanced Materials and Coatings:
- Researchers and engineers use sputtering to develop advanced materials and coatings for smaller, lighter, and more durable products.
- The process is key to innovations in electronics, optics, and renewable energy technologies.
-
Historical and Commercial Use:
- Thomas Edison was one of the first to use sputtering commercially in 1904 to apply thin metal layers to wax phonograph recordings.
- This historical application laid the groundwork for modern sputtering techniques.
By leveraging the sputtering process, industries can achieve precise, high-performance coatings and materials, driving advancements in technology and manufacturing.
Summary Table:
Application | Key Use Cases |
---|---|
Thin-Film Deposition | Anti-reflective coatings, low-emissivity windows, metalizing plastics |
Semiconductor Industry | Integrated circuit processing, conductive and insulating material layering |
Data Storage | Hard disks, CDs, DVDs |
Optical Applications | Anti-reflective films, optical waveguides, photovoltaic solar cells |
Durable Coatings | Cutting tools, automotive wheels, cookware |
Surface Physics and Analysis | High-purity surface preparation, chemical composition analysis |
Advanced Materials | Electronics, optics, renewable energy innovations |
Historical Use | Thomas Edison's phonograph recordings |
Unlock the potential of sputtering for your industry—contact our experts today to learn more!