Biorefineries face a multitude of challenges that span technical, operational, and socio-economic domains. These challenges include the difficulty in reforming biomass-derived liquids due to their larger molecular size and higher carbon content, the need for better catalysts to improve yields and selectivity, and the high costs associated with biomass-derived liquids and capital equipment. Additionally, constructing biomass plants requires large areas, which are hard to find in urban regions, and these plants often have lower productivity compared to other energy sources. Feedstock availability and variability, technological barriers, policy and regulatory frameworks, and the need for continuous research and development further complicate the landscape. Biochemical methods of biomass conversion are also cost-intensive, especially when dealing with lignin-rich biomass, and are relatively slow and sporadic, resulting in diluted products.
Key Points Explained:
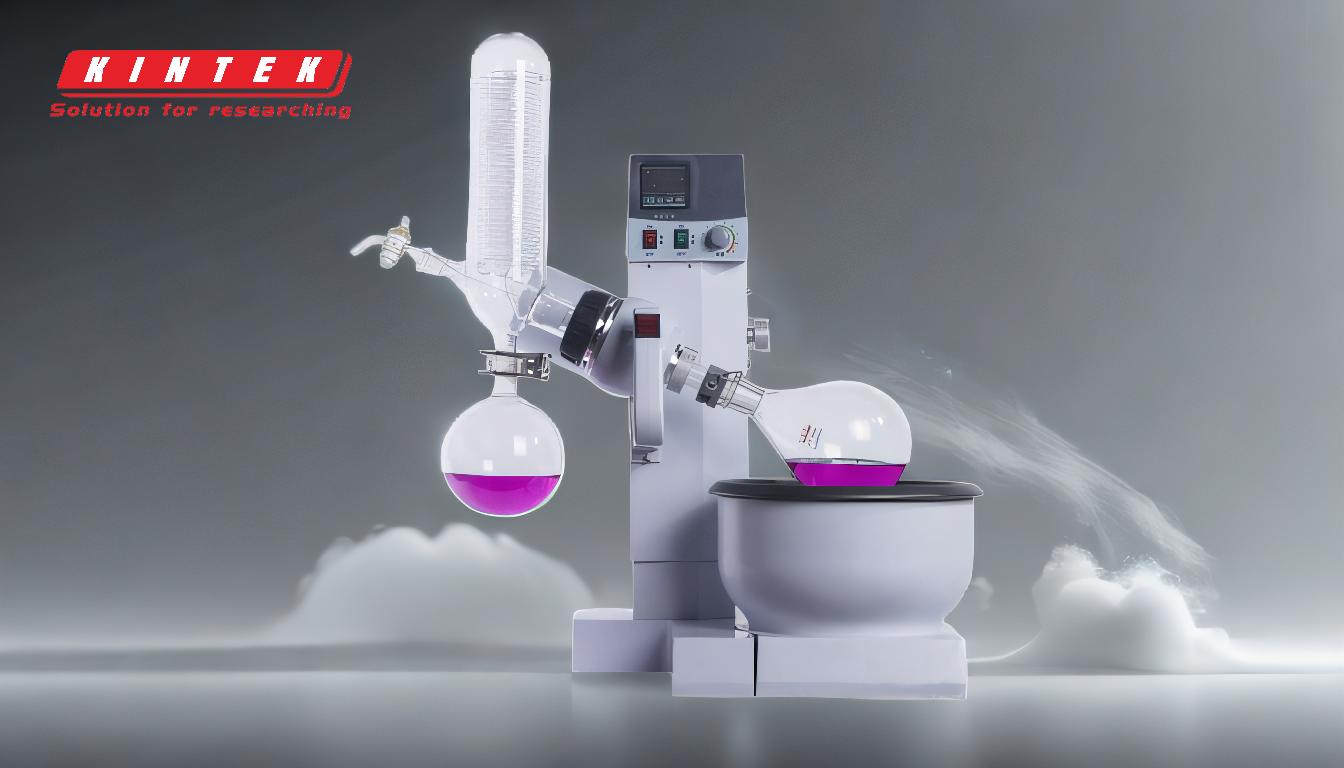
-
Technical Challenges:
- Reforming Biomass-Derived Liquids: Biomass-derived liquids have larger molecular sizes and higher carbon content compared to natural gas, making them more difficult to reform. This necessitates the development of better catalysts to improve yields and selectivity.
- Catalyst Development: Research is ongoing to identify catalysts that can enhance the efficiency of biomass conversion processes, which is crucial for improving the overall yield and selectivity of desired products.
- Process Efficiency: Improving the efficiency of biomass conversion processes is essential to reduce operational costs and enhance the economic viability of biorefineries.
-
Operational Challenges:
- Feedstock Availability and Variability: The availability and consistency of biomass feedstock can vary significantly, posing challenges for continuous and efficient operation of biorefineries. This variability can affect the quality and quantity of the final products.
- Technological Barriers and Scale-Up: Scaling up laboratory-scale processes to industrial-scale operations often encounters technological barriers. Ensuring that the technology can handle larger volumes without compromising efficiency is a significant challenge.
- High Costs: The cost of biomass-derived liquids and the capital equipment required for biorefineries are high. Reducing these costs is crucial for making biorefineries economically competitive with traditional energy sources.
-
Socio-Economic Challenges:
- Land Requirements: Constructing biomass plants requires large areas for plant growth, which are difficult to find in urban regions. This limits the potential locations for biorefineries and can lead to conflicts over land use.
- Lower Productivity: Biomass plants often have lower productivity compared to other energy sources, which can affect their economic viability and attractiveness to investors.
- Policy and Regulatory Frameworks: The development and operation of biorefineries are influenced by policy and regulatory frameworks. Inconsistent or unfavorable policies can hinder the growth and adoption of biorefinery technologies.
-
Biochemical Conversion Challenges:
- Cost-Intensive Processes: Biochemical methods of biomass conversion are cost-intensive, particularly when dealing with lignin-rich biomass. The high costs associated with these methods can limit their widespread adoption.
- Sporadic and Slow Processes: Biochemical conversion processes are often sporadic and relatively slow, which can affect the overall efficiency and output of biorefineries.
- Diluted Products: The products of biochemical conversion are often diluted with a significant amount of water, which can complicate downstream processing and reduce the overall value of the products.
-
Continuous Research and Development:
- Innovation and Improvement: Continuous research and development are essential to overcome the technical and operational challenges faced by biorefineries. Innovations in catalyst development, process efficiency, and feedstock management are crucial for the long-term success of biorefineries.
- Adaptation to New Feedstocks: As new types of biomass become available, biorefineries must adapt their processes to efficiently convert these feedstocks into valuable products. This requires ongoing research and development efforts.
In summary, the challenges of biorefineries are multifaceted and require a comprehensive approach to address. Technical advancements, operational improvements, and supportive socio-economic policies are all critical for overcoming these challenges and realizing the full potential of biorefineries.
Summary Table:
Category | Challenges |
---|---|
Technical Challenges | - Reforming biomass-derived liquids |
- Catalyst development for better yields | |
- Improving process efficiency | |
Operational Challenges | - Feedstock availability and variability |
- Technological barriers and scale-up | |
- High costs of biomass-derived liquids and equipment | |
Socio-Economic Challenges | - Large land requirements |
- Lower productivity compared to other energy sources | |
- Policy and regulatory hurdles | |
Biochemical Challenges | - Cost-intensive processes for lignin-rich biomass |
- Slow and sporadic conversion processes | |
- Diluted products complicating downstream processing | |
R&D Needs | - Continuous innovation in catalysts, processes, and feedstock adaptation |
Ready to tackle biorefinery challenges? Contact our experts today for tailored solutions!