A wiped film evaporator (WFE) is a specialized distillation system designed to efficiently separate components in a mixture by creating a thin, turbulent film of liquid on a heated surface. This process maximizes surface area and heat transfer, enabling precise separations even at low temperatures. The key components of a wiped film evaporator include a check valve, reservoir, feed pump, residue pump, motor, wiper, condenser, heater, vacuum condenser, cold finger, vacuum system, window, and distillate pump. Each component plays a critical role in ensuring the system operates effectively, from feeding the crude material to collecting the separated distillate and residue. The process involves optimizing parameters such as temperature, vacuum, and feed rate to achieve the desired separation efficiency.
Key Points Explained:
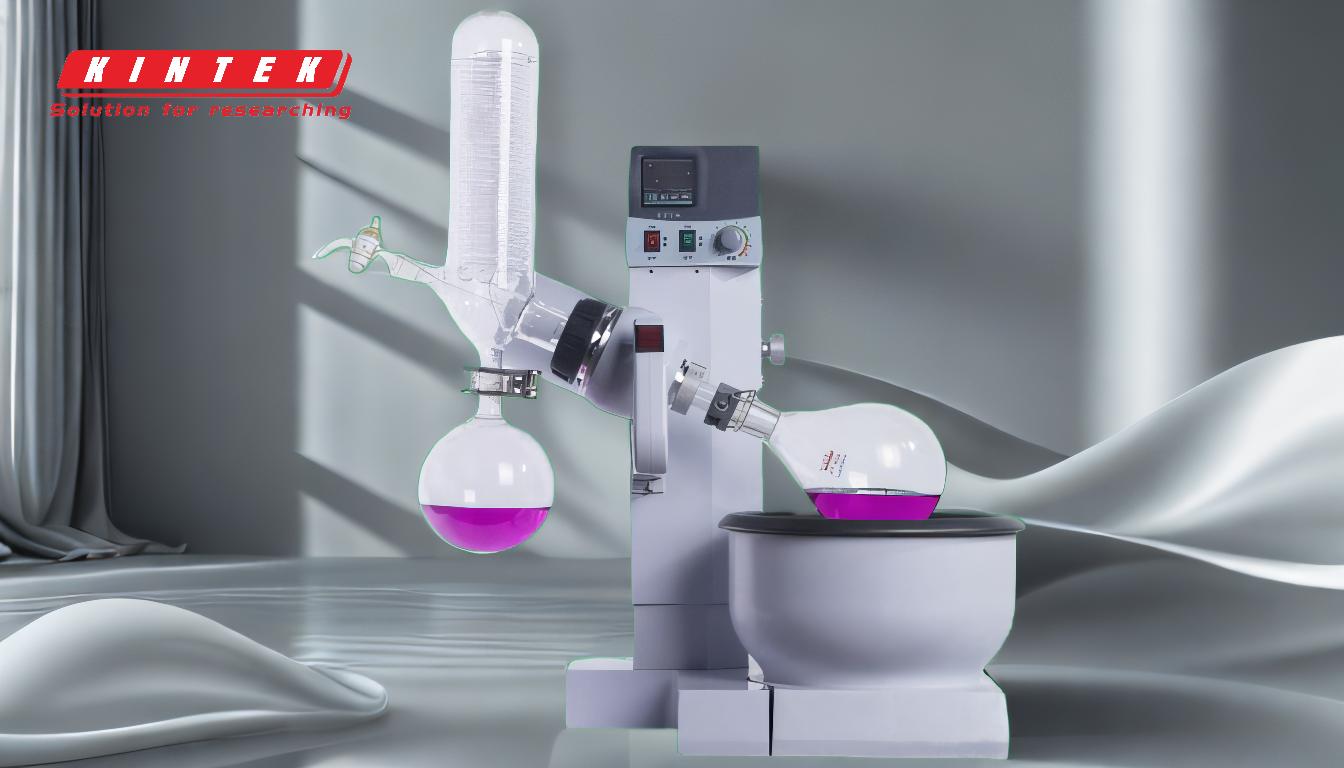
-
Check Valve:
- Ensures unidirectional flow of the feed material into the system, preventing backflow and maintaining process integrity.
- Critical for maintaining pressure and flow consistency in the distillation process.
-
Reservoir:
- Stores the crude oil or feed material before it is introduced into the distillation system.
- Acts as a buffer to ensure a steady supply of material to the feed pump.
-
Feed Pump:
- Transports the crude oil or feed material from the reservoir into the distillation column.
- Ensures a controlled and consistent flow rate, which is essential for maintaining process stability.
-
Residue Pump:
- Collects and removes the heavier, non-volatile residues from the bottom of the distillation column.
- Prevents buildup of residue, which could otherwise hinder the efficiency of the distillation process.
-
Motor:
- Drives the rotation of the wiper blades or rollers inside the distillation column.
- Ensures the creation of a thin, turbulent film of liquid on the heated surface, which is critical for efficient heat transfer and separation.
-
Wiper (Wiper Blades or Rollers):
- Made from materials like PTFE or PBI, these components create a thin film of liquid on the heated inner wall of the distillation column.
- Enhances mass transfer and separation efficiency by continuously mixing the liquid and exposing it to the heated surface.
-
Condenser:
- Cools and condenses the vaporized components into a liquid distillate.
- Internal condensers are typically used for primary condensation, while external condensers may capture specific fractions like terpenes.
-
Heater:
- Provides the necessary heat to the outer wall of the distillation column, enabling the evaporation of lighter fractions.
- Maintains precise temperature control to ensure optimal separation of components.
-
Vacuum Condenser:
- Operates under vacuum conditions to lower the boiling points of the components, allowing for low-temperature distillations.
- Enhances the efficiency of the condensation process by reducing thermal degradation of sensitive materials.
-
Cold Finger:
- A secondary condensation device used to capture specific volatile components that may not condense in the primary condenser.
- Often used in conjunction with the vacuum system to improve separation efficiency.
-
Vacuum System:
- Creates and maintains a vacuum within the distillation column, lowering the boiling points of the components and enabling low-temperature distillations.
- Reduces the risk of thermal degradation and improves the overall efficiency of the separation process.
-
Window:
- Provides visual access to the inside of the distillation column, allowing operators to monitor the process and ensure proper operation.
- Useful for troubleshooting and process optimization.
-
Distillate Pump:
- Collects and transfers the condensed distillate from the condenser to the receiving vessel.
- Ensures the efficient and continuous removal of the separated components.
Each of these components works in harmony to create a highly efficient and precise distillation process. The wiped film evaporator is particularly effective for separating heat-sensitive materials, as it minimizes exposure to high temperatures and reduces the risk of degradation. By optimizing parameters such as temperature, vacuum, and feed rate, the system achieves fine separations and high productivity, making it a valuable tool in industries such as chemical processing, pharmaceuticals, and cannabis extraction.
Summary Table:
Component | Function |
---|---|
Check Valve | Ensures unidirectional flow, maintaining process integrity. |
Reservoir | Stores feed material, ensuring a steady supply. |
Feed Pump | Transports feed material into the column at a controlled rate. |
Residue Pump | Removes heavy residues, preventing buildup. |
Motor | Drives wiper blades to create a thin, turbulent film for efficient heating. |
Wiper | Enhances mass transfer by continuously mixing the liquid on the heated wall. |
Condenser | Cools and condenses vaporized components into distillate. |
Heater | Provides precise heat for evaporation of lighter fractions. |
Vacuum Condenser | Lowers boiling points, enabling low-temperature distillations. |
Cold Finger | Captures volatile components not condensed in the primary condenser. |
Vacuum System | Maintains vacuum, reducing thermal degradation and improving efficiency. |
Window | Allows visual monitoring for troubleshooting and optimization. |
Distillate Pump | Collects and transfers distillate to the receiving vessel. |
Ready to enhance your distillation process? Contact us today to learn more about wiped film evaporators!