Glass reactors are essential equipment in chemical, pharmaceutical, and research laboratories, designed to handle a variety of reactions under controlled conditions. The primary types of glass reactors include single-layer, double-layer, and three-layer glass reactors, each offering distinct features and applications. Additionally, specialized reactors like jacketed glass reactors, glass-lined reactors, and photochemical reactors cater to specific reaction requirements. The choice of reactor depends on factors such as temperature control, pressure resistance, and the nature of the chemicals involved. Below, we explore the different types of glass reactors in detail, their unique characteristics, and their applications.
Key Points Explained:
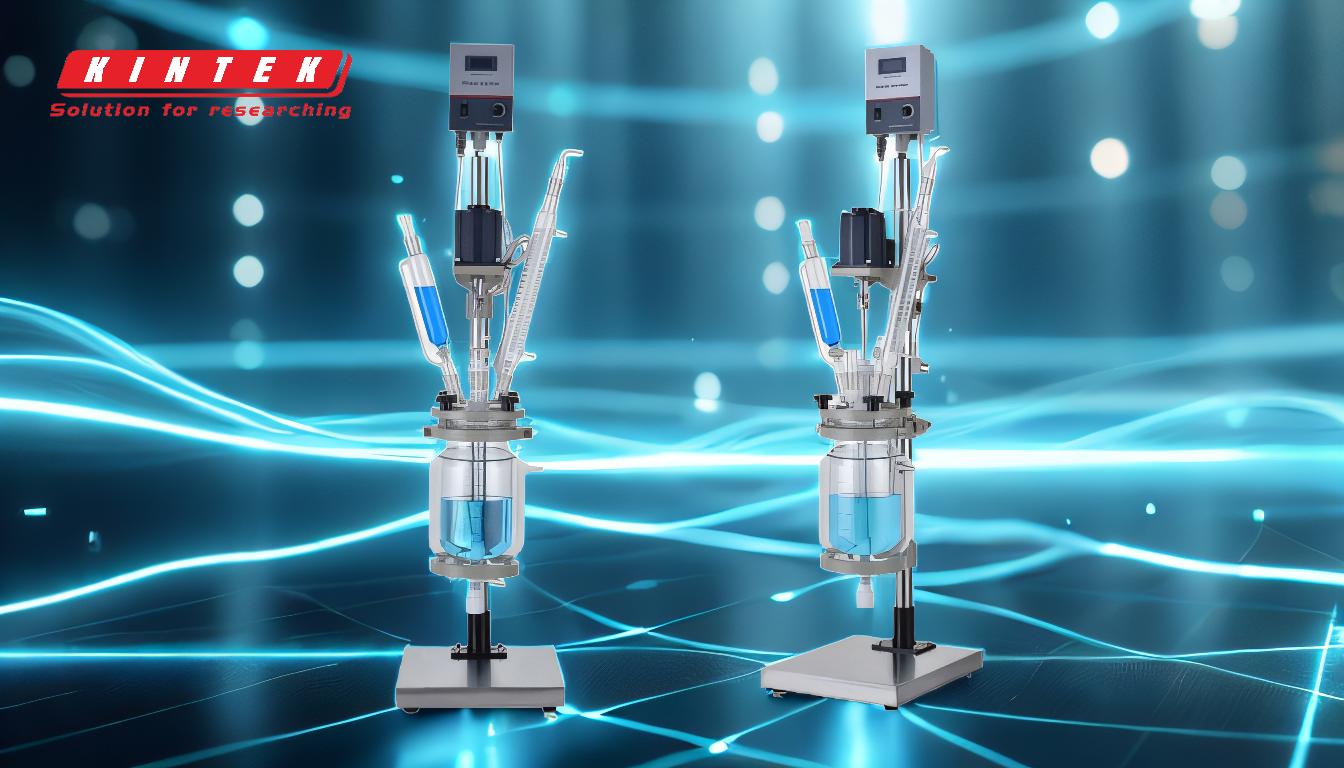
-
Single-Layer Glass Reactors
- Description: Single-layer glass reactors consist of a single glass vessel without additional layers or insulation.
- Applications: These reactors are multifunctional and widely used in chemical industries for processes such as mixing, dissolving, and crystallization.
-
Advantages:
- Simple design and cost-effective.
- Easy to clean and maintain.
- Suitable for reactions that do not require precise temperature control.
-
Limitations:
- Limited thermal insulation, making them less suitable for reactions requiring strict temperature regulation.
-
Double-Layer Glass Reactors
- Description: Double-layer glass reactors feature an inner glass vessel surrounded by an outer layer, creating a space for a heating or cooling medium (e.g., water or oil).
- Applications: Ideal for reactions requiring temperature control, such as distillation, reflux, and condensation.
-
Advantages:
- Enhanced temperature control due to the jacketed design.
- Suitable for vacuum and pressure-sensitive reactions.
- Versatile for a wide range of chemical processes.
-
Limitations:
- More complex design compared to single-layer reactors.
- Higher cost due to additional components.
-
Three-Layer Glass Reactors
- Description: Three-layer glass reactors include an additional insulating layer between the inner and outer glass layers, providing superior thermal insulation and stability.
- Applications: Used for highly sensitive reactions requiring precise temperature control, such as polymerization and crystallization.
-
Advantages:
- Excellent thermal insulation and stability.
- Suitable for high-temperature and high-pressure reactions.
- Reduces heat loss, improving energy efficiency.
-
Limitations:
- Higher cost and more complex maintenance.
- Larger footprint compared to single- and double-layer reactors.
-
Jacketed Glass Reactors
- Description: Jacketed glass reactors are a specialized type of double-layer reactor where the outer layer (jacket) is used to circulate heating or cooling fluids.
- Applications: Commonly used in vacuum and temperature-controlled environments for processes like distillation, extraction, and synthesis.
-
Advantages:
- Precise temperature control for sensitive reactions.
- Compatible with a wide range of solvents and chemicals.
- Durable and resistant to thermal shock.
-
Limitations:
- Requires additional equipment for fluid circulation.
- Higher initial investment and operating costs.
-
Glass-Lined Reactors
- Description: Glass-lined reactors feature a glass coating on the inner surface of a metal vessel, combining the chemical resistance of glass with the structural strength of metal.
- Applications: Used in industries requiring high corrosion resistance, such as pharmaceuticals and fine chemicals.
-
Advantages:
- Excellent chemical resistance and durability.
- Suitable for high-pressure and high-temperature reactions.
- Easy to clean and maintain.
-
Limitations:
- Higher cost due to the specialized manufacturing process.
- Susceptible to damage from mechanical impact.
-
Specialized Glass Reactors
- Continuous Flow Reactors: Designed for continuous chemical processes, these reactors are ideal for large-scale production and reactions requiring constant monitoring.
- Batch Reactors: Used for small-scale or batch processes, allowing precise control over reaction conditions.
- Photochemical Reactors: Equipped with light sources for reactions driven by light, such as photolysis and photopolymerization.
- Hydrothermal Synthesis Reactors: Designed for high-temperature and high-pressure reactions in aqueous solutions.
- Stirring Magnetic Reactors: Feature magnetic stirrers for efficient mixing without mechanical seals.
- Electric Heating Reactors: Use electric heating elements for precise temperature control.
- Steam Reactors: Utilize steam for heating, commonly used in industrial processes.
-
Material Properties of Glass Reactors
- Chemical Resistance: The glass used in reactors is highly resistant to a wide range of chemicals, making it suitable for corrosive substances.
- Thermal Resistance: Reactor glass can withstand extreme temperatures, ensuring stability during heating and cooling processes.
- Transparency: Glass reactors allow visual monitoring of reactions, which is crucial for quality control and process optimization.
-
Comparison with Other Materials
- Stainless Steel Reactors: While stainless steel reactors offer high strength and durability, they lack the chemical resistance and transparency of glass reactors.
- Carbon Steel and Alloy Reactors: These materials are cost-effective but may require additional coatings for chemical resistance.
- Glass-Lined Steel Reactors: Combine the benefits of glass and steel, offering both chemical resistance and structural integrity.
In conclusion, the choice of glass reactor depends on the specific requirements of the chemical process, including temperature control, pressure resistance, and the nature of the reactants. Each type of glass reactor offers unique advantages, making them indispensable tools in modern laboratories and industrial settings.
Summary Table:
Type of Glass Reactor | Key Features | Applications | Advantages | Limitations |
---|---|---|---|---|
Single-Layer | Single glass vessel, no insulation | Mixing, dissolving, crystallization | Cost-effective, easy to clean | Limited thermal insulation |
Double-Layer | Inner and outer glass layers with heating/cooling space | Distillation, reflux, condensation | Enhanced temperature control | Higher cost, complex design |
Three-Layer | Additional insulating layer for superior thermal stability | Polymerization, crystallization | Excellent insulation, energy-efficient | Higher cost, larger footprint |
Jacketed | Outer layer circulates heating/cooling fluids | Distillation, extraction, synthesis | Precise temperature control | Requires additional equipment |
Glass-Lined | Glass coating on metal vessel | Pharmaceuticals, fine chemicals | Chemical resistance, durability | Susceptible to mechanical damage |
Specialized | Includes photochemical, continuous flow, and more | Light-driven reactions, large-scale production | Tailored for specific needs | Higher initial investment |
Need help selecting the right glass reactor for your lab? Contact our experts today for personalized guidance!