Diffusion pumps, while highly effective for creating high vacuum levels, have several notable disadvantages. These include the use of toxic oils that require careful disposal, potential explosion risks with hydrocarbon-based oils, and the need for regular maintenance to ensure proper operation. Additionally, traditional oil-sealed designs can release oil mist into the environment, and the alignment of heater components in limited spaces can be challenging. Despite their durability and reliability due to the absence of moving parts, these drawbacks make diffusion pumps less ideal for certain applications, especially where safety and environmental concerns are paramount.
Key Points Explained:
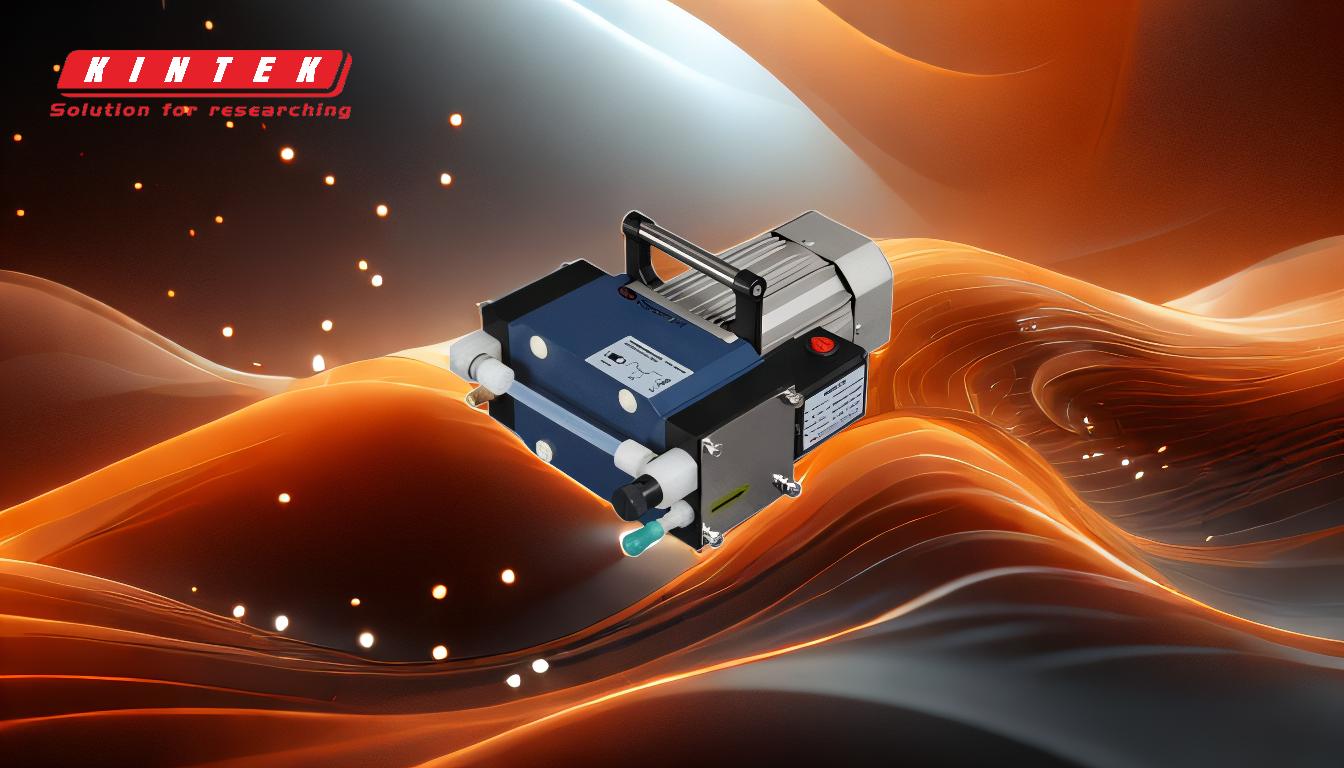
-
Toxic Oil Waste Disposal:
- Diffusion pumps often use hydrocarbon or silicone-based oils, which can be toxic and require proper disposal methods to avoid environmental contamination.
- The disposal process can be complex and costly, adding to the operational expenses of using diffusion pumps.
-
Explosion Risks with Hydrocarbon Oils:
- Hydrocarbon-based oils used in diffusion pumps can break down into lighter fractions, which may escape the pump and pose an explosion risk, especially in environments with ignition sources.
- Silicone-based oils are safer in this regard, but the risk still exists if the pump is not properly maintained or if the fill port is opened while the pump is operating.
-
Regular Maintenance Requirements:
- Diffusion pumps require regular maintenance to ensure the appropriate oil level and operational heaters.
- Proper alignment of heater components, especially in limited spaces, can be challenging and time-consuming.
- Traditional heater designs with tubular elements, crush plates, and clamping plates add to the complexity of maintenance.
-
Oil Mist Release:
- Despite updated oil filter hardware, traditional oil-sealed diffusion pumps can still release oil mist into the laboratory environment.
- This can lead to contamination and health risks for laboratory personnel, necessitating additional safety measures.
-
High Operational Temperatures:
- Diffusion pumps operate at high temperatures (up to 240ºC or 464ºF), which can cause hydrocarbon-based oils to produce vapors that react explosively with air.
- This necessitates strict safety protocols, such as never opening the fill port while the pump is operating.
-
Cost and Complexity of Spare Parts:
- Finding replacement spare parts for diffusion pumps can be difficult, especially for older models.
- This can lead to increased downtime and higher costs for maintaining the pump.
-
Environmental and Safety Concerns:
- The use of toxic oils and the potential for oil mist release make diffusion pumps less environmentally friendly and pose safety risks.
- These concerns are particularly relevant in sensitive environments such as laboratories and industrial settings where safety and environmental regulations are stringent.
-
Durability and Reliability:
- Despite these disadvantages, diffusion pumps are durable and reliable due to the absence of moving parts.
- They are capable of producing high vacuum levels (10^-2 to 10^-10 torr) and are widely used in applications like electron-beam microscopy, vacuum deposition, coatings, and vacuum furnaces.
In summary, while diffusion pumps are effective for achieving high vacuum levels, their disadvantages, including toxic oil disposal, explosion risks, and high maintenance requirements, make them less suitable for certain applications. Careful consideration of these factors is essential when selecting a vacuum pump for specific needs.
Summary Table:
Disadvantages | Details |
---|---|
Toxic Oil Waste Disposal | Hydrocarbon or silicone-based oils require costly and complex disposal. |
Explosion Risks | Hydrocarbon oils can break down, posing explosion risks in certain environments. |
Regular Maintenance | High maintenance needs, including heater alignment and oil level checks. |
Oil Mist Release | Traditional designs may release oil mist, causing contamination risks. |
High Operational Temperatures | Temperatures up to 240°C can cause explosive vapor reactions with air. |
Cost and Complexity of Spare Parts | Difficulty in finding replacement parts, leading to downtime and higher costs. |
Environmental and Safety Concerns | Toxic oils and oil mist release pose environmental and safety risks. |
Durability and Reliability | Despite drawbacks, diffusion pumps are durable and reliable with no moving parts. |
Need help selecting the right vacuum pump for your needs? Contact our experts today to find the best solution!