Distillation, while a widely used separation technique, has several disadvantages that limit its efficiency, scalability, and applicability in certain contexts. These drawbacks include the loss of volatile solvents, challenges in handling heat-sensitive compounds like cannabinoids, high equipment costs, and limitations in separation efficiency and production time. Additionally, traditional distillation methods often involve complex setups and maintenance, making them less practical for continuous or large-scale operations. Below, the key disadvantages of distillation are explained in detail, focusing on both technical and practical limitations.
Key Points Explained:
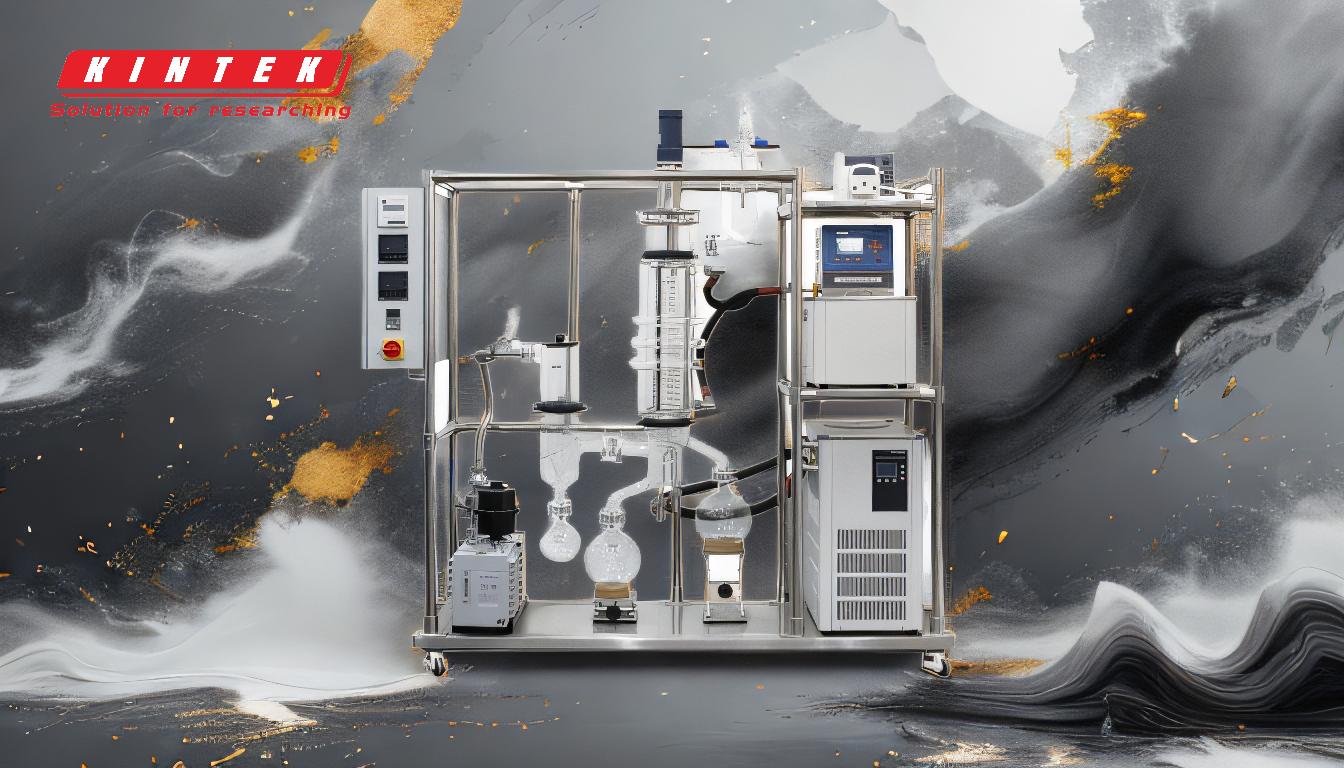
-
Loss of Volatile Solvents
- In short-path distillation, the short distance between the evaporation flask and the receiving flask can lead to the loss of volatile solvents. This is particularly problematic when working with compounds that have low boiling points or are highly volatile.
- The loss of solvents not only reduces the yield but also limits the market growth of short-path distillation systems, as industries seek more efficient and reliable methods for solvent recovery.
-
Heat Degradation of Sensitive Compounds
- Distillation often requires high temperatures to separate compounds based on their boiling points. However, this can be detrimental to heat-sensitive compounds like cannabinoids (e.g., CBD).
- For example, CBD is prone to degradation at high temperatures, which can alter its chemical structure and reduce its efficacy. While short-path distillation at low pressure can mitigate this issue, it adds complexity and cost to the process.
-
Limitations in Batch Size and Scalability
- Traditional short-path distillation systems are often limited to small batch sizes, making them unsuitable for large-scale industrial applications.
- The lack of continuous feed capability further restricts their utility, as industries often require continuous processing to meet production demands.
-
Low Separation Efficiency and Time Consumption
- Molecular distillation, a specialized form of distillation, faces challenges in separation efficiency. The design of molecular stills often results in low separation rates, which can compromise the purity of the final product.
- Additionally, the process is time-consuming, making it less efficient for industries that require high throughput and rapid production cycles.
-
High Equipment Costs and Complexity
- Molecular distillation systems require high vacuum systems and precise material sealing, which significantly increase the cost of equipment.
- The design and maintenance of evaporation and condensation surfaces are complex, requiring specialized expertise and adding to operational challenges.
- Maintaining a high vacuum degree further complicates the process, as it demands advanced technology and rigorous maintenance protocols.
-
Tedious Setup and Cleaning Procedures
- Simple distillation methods, such as solvent removal, are often tedious due to the complexity of setting up and cleaning the apparatus.
- These procedures can be labor-intensive and time-consuming, reducing the overall efficiency of the process and increasing operational costs.
-
Inconsistencies in Small-Scale Systems
- Small-scale distillation systems, such as those used in traditional short-path distillation, are prone to inconsistencies. These inconsistencies can arise from variations in temperature, pressure, or flow rates, leading to unreliable results.
- Such limitations make small-scale systems less attractive for industries that require consistent and reproducible outcomes.
In summary, while distillation is a valuable technique for separating and purifying compounds, its disadvantages—ranging from heat degradation and solvent loss to high costs and scalability issues—highlight the need for alternative or complementary methods in certain applications. Industries must carefully weigh these drawbacks against the benefits of distillation when selecting separation techniques for their specific needs.
Summary Table:
Disadvantage | Description |
---|---|
Loss of Volatile Solvents | Short-path distillation leads to solvent loss, reducing yield and efficiency. |
Heat Degradation of Compounds | High temperatures can degrade heat-sensitive compounds like cannabinoids. |
Batch Size and Scalability Issues | Limited to small batches, unsuitable for large-scale or continuous operations. |
Low Separation Efficiency | Molecular distillation has low separation rates, compromising purity and speed. |
High Equipment Costs | Requires expensive vacuum systems and complex maintenance. |
Tedious Setup and Cleaning | Labor-intensive procedures increase operational costs and reduce efficiency. |
Inconsistencies in Small Systems | Small-scale systems often produce unreliable results due to variability. |
Need a more efficient separation solution? Contact our experts today to explore alternatives tailored to your needs!