Vacuum evaporation, while widely used in thin-film deposition, has several notable disadvantages that can impact its effectiveness and applicability in various industrial and research settings. These drawbacks include challenges in depositing certain materials, poor surface coverage on complex geometries, limited control over film properties, low material efficiency, and high operational costs due to the need for large vacuum chambers and specialized equipment. Additionally, contamination risks, poor step coverage, and potential damage from electron beam evaporation further limit its utility. Understanding these limitations is crucial for selecting the appropriate deposition method for specific applications.
Key Points Explained:
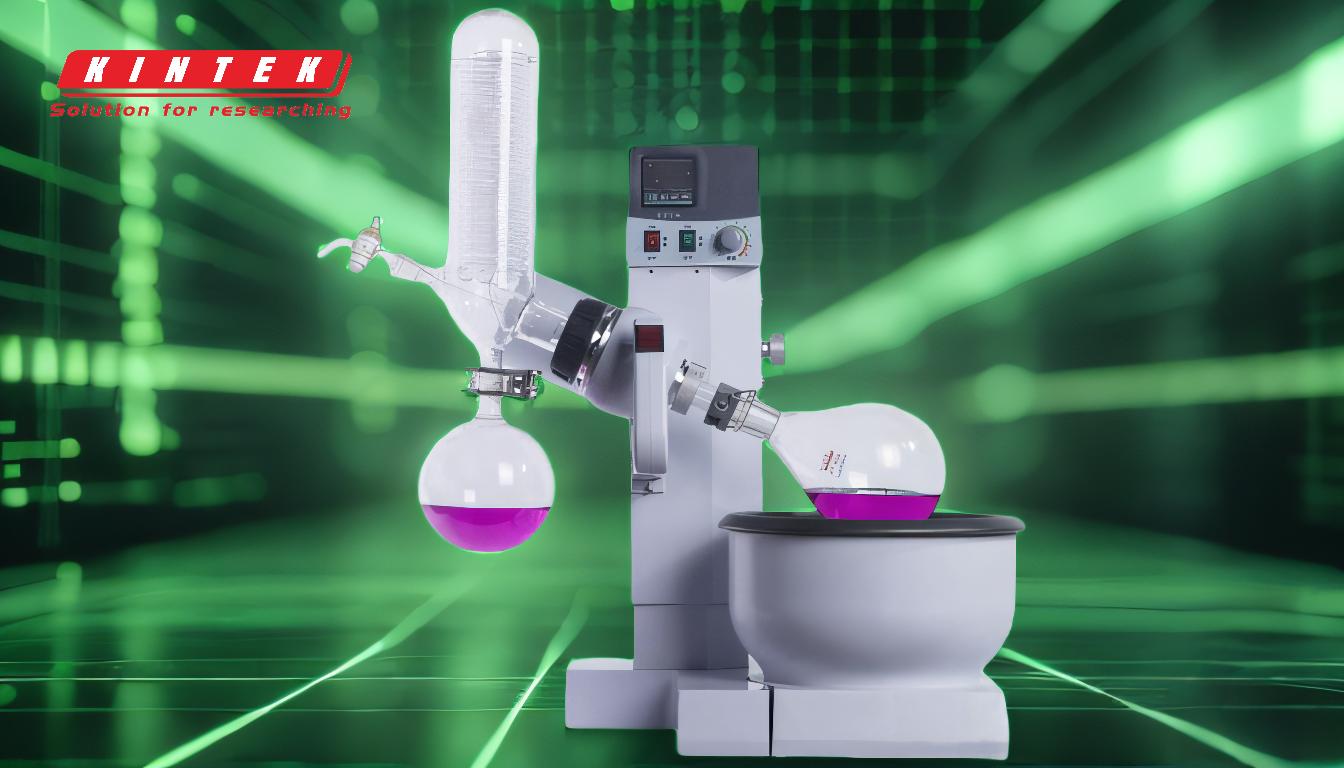
-
Difficulty in Depositing Compounds and Alloys
- Vacuum evaporation struggles with depositing many compounds and alloys due to differences in vapor pressures among the constituent elements. This can lead to non-uniform compositions in the deposited film, making it unsuitable for applications requiring precise stoichiometry.
-
Poor Surface Coverage on Complex Surfaces
- Without proper fixturing, vacuum evaporation often results in poor surface coverage on complex or three-dimensional substrates. This is because the process relies on line-of-sight deposition, which can leave shadowed areas inadequately coated.
-
Poor Film-Thickness Uniformity Over Large Areas
- Achieving uniform film thickness across large substrates is challenging with vacuum evaporation. Variations in source-to-substrate distance and evaporation rates can lead to inconsistent coatings, which is problematic for applications requiring precise thickness control.
-
Limited Processing Variables for Film Property Control
- Compared to other deposition methods like sputtering, vacuum evaporation offers fewer variables for controlling film properties such as density, stress, and adhesion. This limits its ability to tailor films for specific applications.
-
Low Source Material Use Efficiency
- Vacuum evaporation is less efficient in terms of material utilization. A significant portion of the source material may be wasted, increasing costs, especially when using expensive or rare materials.
-
High Radiant Heat Loads
- The process generates high radiant heat, which can damage temperature-sensitive substrates or require additional cooling systems, adding complexity and cost to the setup.
-
Need for Large-Volume Vacuum Chambers
- Vacuum evaporation requires large vacuum chambers to maintain the necessary low-pressure environment. These chambers are expensive to build, maintain, and operate, making the process less economical for small-scale or low-budget applications.
-
Contamination Risks
- Contamination from impurities in crucibles or the evaporation source can degrade film quality. High-purity crucibles are expensive, and for high-temperature processes, graphite crucibles may introduce carbon contamination.
-
Poor Step Coverage
- Vacuum evaporation performs poorly in coating steps or features on substrates, as it lacks the directional control and bombardment effects found in sputtering. This makes it less suitable for applications requiring conformal coatings.
-
X-ray Damage from Electron Beam Evaporation
- Electron beam evaporation, a common variant of vacuum evaporation, can generate X-rays that may damage sensitive substrates or components, limiting its use in certain applications.
-
High Impurity Levels and Low-Density Films
- Vacuum evaporation often results in films with higher impurity levels and lower density compared to other PVD methods. While ion-assisted deposition can improve density, it adds complexity and cost to the process.
-
Moderate Film Stress
- Films deposited via vacuum evaporation may exhibit moderate stress, which can affect adhesion and long-term stability. This is a concern for applications requiring durable and robust coatings.
-
No In Situ Substrate Cleaning
- Unlike sputtering, vacuum evaporation lacks the capability for in situ substrate cleaning, which can lead to poorer adhesion and increased contamination risks.
By understanding these disadvantages, users can make informed decisions about whether vacuum evaporation is suitable for their specific needs or if alternative deposition methods might be more appropriate.
Summary Table:
Disadvantage | Impact |
---|---|
Difficulty in depositing compounds/alloys | Non-uniform compositions, unsuitable for precise stoichiometry |
Poor surface coverage on complex surfaces | Shadowed areas inadequately coated |
Poor film-thickness uniformity | Inconsistent coatings, problematic for precise thickness control |
Limited control over film properties | Fewer variables for density, stress, and adhesion control |
Low material efficiency | High material wastage, increased costs |
High radiant heat loads | Damages temperature-sensitive substrates, requires cooling systems |
Need for large vacuum chambers | High operational and maintenance costs |
Contamination risks | Degrades film quality, requires high-purity crucibles |
Poor step coverage | Unsuitable for conformal coatings |
X-ray damage from electron beam evaporation | Damages sensitive substrates |
High impurity levels and low-density films | Films less dense and more impure |
Moderate film stress | Affects adhesion and long-term stability |
No in situ substrate cleaning | Poorer adhesion, increased contamination risks |
Need help selecting the right deposition method for your application? Contact our experts today!