The blown film extrusion process involves several key components that work together to produce high-quality plastic films. These components include the die, material feeding system, air ring, film winding unit, control system, and safety system. Each element plays a critical role in shaping, cooling, and winding the plastic film, ensuring consistency, precision, and safety throughout the process. Below, we will explore these components in detail, explaining their functions and importance in the blown film extrusion line.
Key Points Explained:
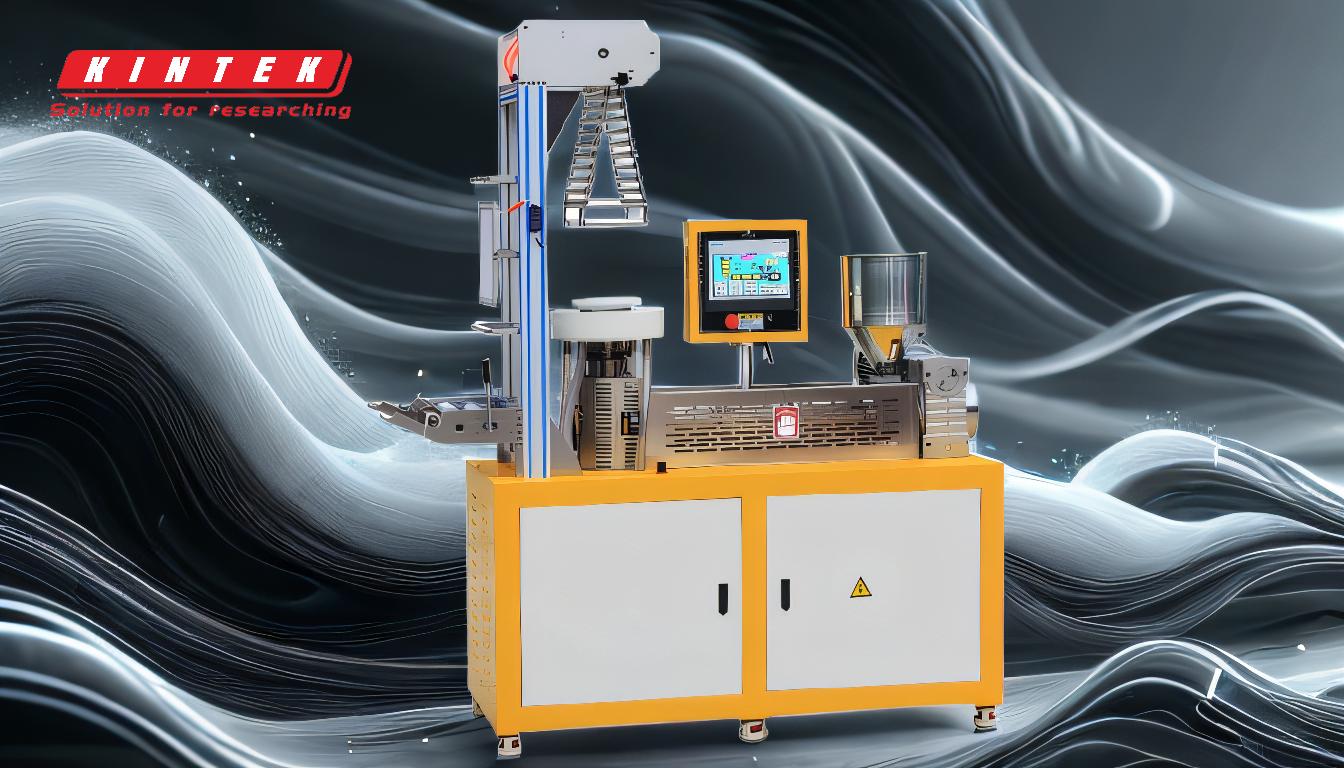
-
Die: Shaping the Melted Plastic
- The die is a crucial component that shapes the melted plastic into a tubular form. It is designed to distribute the molten plastic evenly, ensuring uniform thickness and consistency in the final film.
- The die's design and precision directly impact the quality of the film, making it a critical element in the extrusion process.
-
Material Feeding System: Keeping the Flow Consistent
- The material feeding system is responsible for delivering raw plastic material (usually in pellet or granular form) to the extruder. It ensures a consistent and controlled flow of material, which is essential for maintaining uniform film quality.
- This system often includes hoppers, feeders, and conveyors, all working together to prevent interruptions or inconsistencies in the extrusion process.
-
Air Ring: Cooling and Expanding the Film
- The air ring is used to cool the extruded plastic tube as it exits the die. It blows air onto the film to solidify it while maintaining its tubular shape.
- This component also helps control the bubble size (diameter) of the film, which is critical for achieving the desired film dimensions and properties.
-
Film Winding Unit: The Final Touches
- The film winding unit collects and winds the finished film onto rolls. It ensures that the film is wound evenly and tightly, preventing wrinkles, tears, or other defects.
- This unit often includes tension control mechanisms to maintain consistent winding pressure, which is essential for producing high-quality rolls of film.
-
Control System: Precision and Optimization
- The control system is the brain of the blown film extrusion line. It monitors and regulates various parameters, such as temperature, pressure, and speed, to ensure optimal performance.
- Modern control systems often feature automation and real-time monitoring, allowing operators to make adjustments and maintain consistent film quality.
-
Safety System: Protection First
- The safety system is designed to protect both the equipment and operators. It includes emergency stops, alarms, and protective barriers to prevent accidents or damage during operation.
- Safety is a top priority in blown film extrusion, as the process involves high temperatures, pressures, and moving parts.
By understanding these essential components, equipment and consumable purchasers can make informed decisions when selecting or maintaining blown film extrusion lines. Each element plays a vital role in ensuring the efficiency, quality, and safety of the film production process.
Summary Table:
Component | Function | Importance |
---|---|---|
Die | Shapes melted plastic into a tubular form with uniform thickness. | Ensures consistent film quality and precision. |
Material Feeding System | Delivers raw plastic material to the extruder consistently. | Maintains uniform film quality and prevents interruptions. |
Air Ring | Cools and solidifies the extruded plastic tube while controlling bubble size. | Achieves desired film dimensions and properties. |
Film Winding Unit | Collects and winds finished film onto rolls evenly and tightly. | Prevents defects like wrinkles or tears in the final product. |
Control System | Monitors and regulates temperature, pressure, and speed for optimal performance. | Ensures precision and consistency in film production. |
Safety System | Protects equipment and operators with emergency stops and alarms. | Prioritizes safety in high-temperature, high-pressure environments. |
Ready to optimize your blown film extrusion process? Contact our experts today for tailored solutions!