DC sputtering, while a widely used thin-film deposition technique, has several limitations that can impact its efficiency, quality, and applicability. These limitations include challenges with insulating materials, potential film contamination, lower deposition rates, and difficulties in controlling process parameters. Additionally, issues such as substrate heating, arcing, and target poisoning further complicate the process. Advanced techniques like magnetron sputtering have been developed to mitigate some of these issues, but DC sputtering still faces inherent challenges that limit its effectiveness in certain applications.
Key Points Explained:
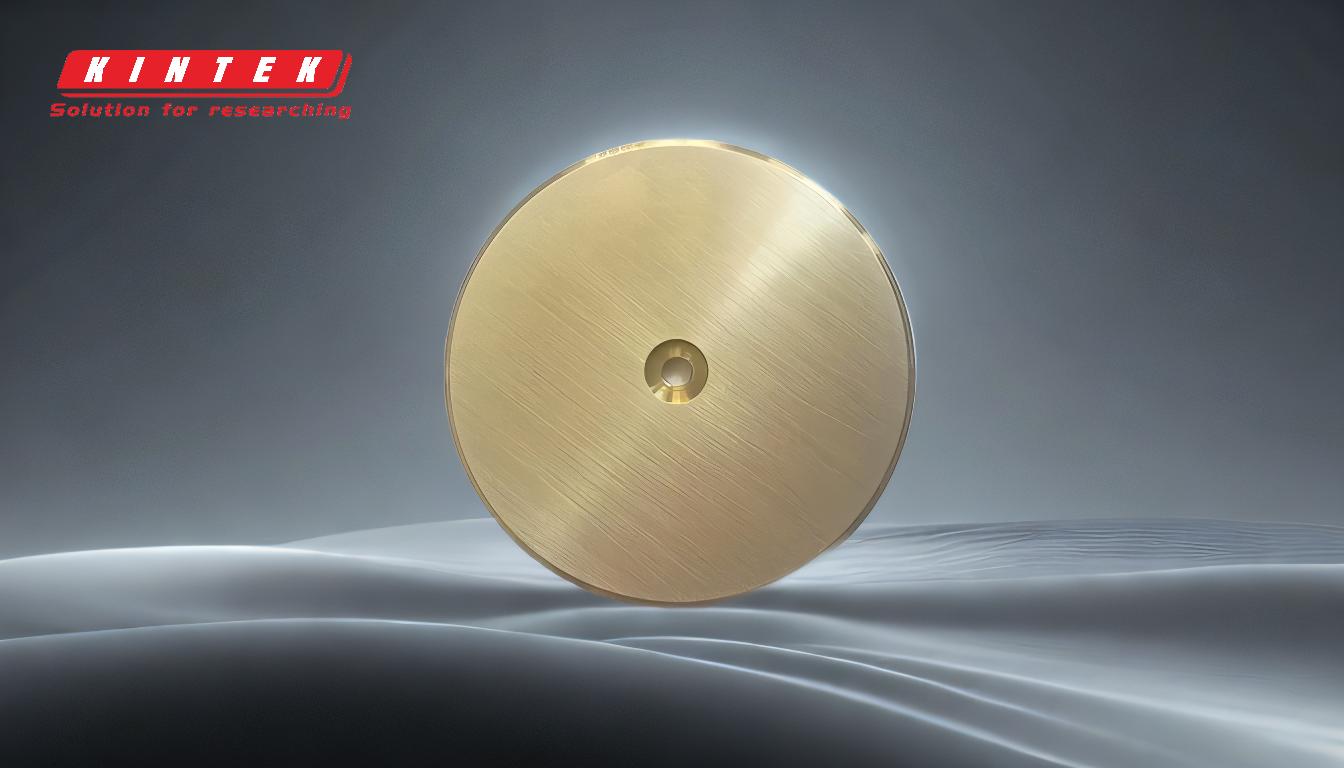
-
Challenges with Insulating Materials:
- Charge Buildup: Non-conducting dielectric materials can accumulate charge over time, leading to arcing or target poisoning. This disrupts the sputtering process and can halt it entirely.
- Arcing and Power Supply Damage: The buildup of charge can cause small and macro arcs, which not only damage the power supply but also result in uneven atom removal from the target material.
-
Film Contamination:
- Impurity Diffusion: During the sputtering process, impurities from the source materials can diffuse into the film, leading to contamination.
- Melting Temperature Constraints: The selection of coating materials is limited by their melting temperatures, which can restrict the range of materials that can be effectively sputtered.
-
Lower Deposition Rates:
- Plasma Density: DC sputtering generally has lower plasma densities compared to more advanced techniques like High Power Impulse Magnetron Sputtering (HIPIMS), resulting in lower deposition rates.
- Gas Density: Higher gas densities in DC sputtering further contribute to lower deposition rates.
-
Process Control and Parameter Sensitivity:
- Parameter Sensitivity: Accurate control of process parameters such as gas pressure, target-substrate distance, and voltage is crucial for optimal results. Small deviations can significantly impact the quality of the deposited film.
- High Operating Pressures: Traditional sputtering processes often require high operating pressures, which can affect the quality and efficiency of the thin film deposition.
-
Substrate Heating:
- Thermal Effects: The sputtering process can cause significant heating of the substrate, which may not be desirable for temperature-sensitive materials or applications.
-
Cooling System Requirements:
- Energy Costs: The need for a cooling system to manage substrate heating decreases the production rate and increases energy costs, making the process less efficient and more expensive.
-
Chamber Contamination:
- Non-Conducting Coatings: Sputtering of dielectric materials can coat the vacuum chamber walls with non-conducting material, trapping electric charges and leading to arcing and other quality issues.
-
Shielding and Permeation Issues:
- Elastomer Seals: Permeation through elastomer seals and issues related to shielding can further complicate the sputtering process, affecting the overall quality of the deposited film.
In summary, while DC sputtering is a valuable technique for thin-film deposition, it is not without its limitations. These challenges necessitate careful consideration of process parameters, material selection, and the use of advanced techniques to mitigate some of the inherent issues. Understanding these limitations is crucial for optimizing the sputtering process and achieving high-quality thin films.
Summary Table:
Limitation | Key Challenges |
---|---|
Insulating Materials | Charge buildup, arcing, and power supply damage |
Film Contamination | Impurity diffusion, melting temperature constraints |
Lower Deposition Rates | Low plasma density, high gas density |
Process Control | Parameter sensitivity, high operating pressures |
Substrate Heating | Thermal effects on temperature-sensitive materials |
Cooling System Requirements | Increased energy costs and reduced production rates |
Chamber Contamination | Non-conducting coatings leading to arcing and quality issues |
Shielding and Permeation | Elastomer seal permeation and shielding complications |
Need help optimizing your thin-film deposition process? Contact our experts today for tailored solutions!