Sputtering, while a widely used technique for thin film deposition, has several notable limitations that impact its efficiency, cost, and the quality of the deposited films. These limitations include issues such as film contamination, low deposition rates, high energy consumption, difficulties in controlling film thickness, and challenges in material selection. Additionally, the process can be expensive due to the need for specialized equipment and maintenance, and it may not be suitable for all types of materials or applications. Understanding these limitations is crucial for optimizing the sputtering process and selecting the appropriate deposition method for specific needs.
Key Points Explained:
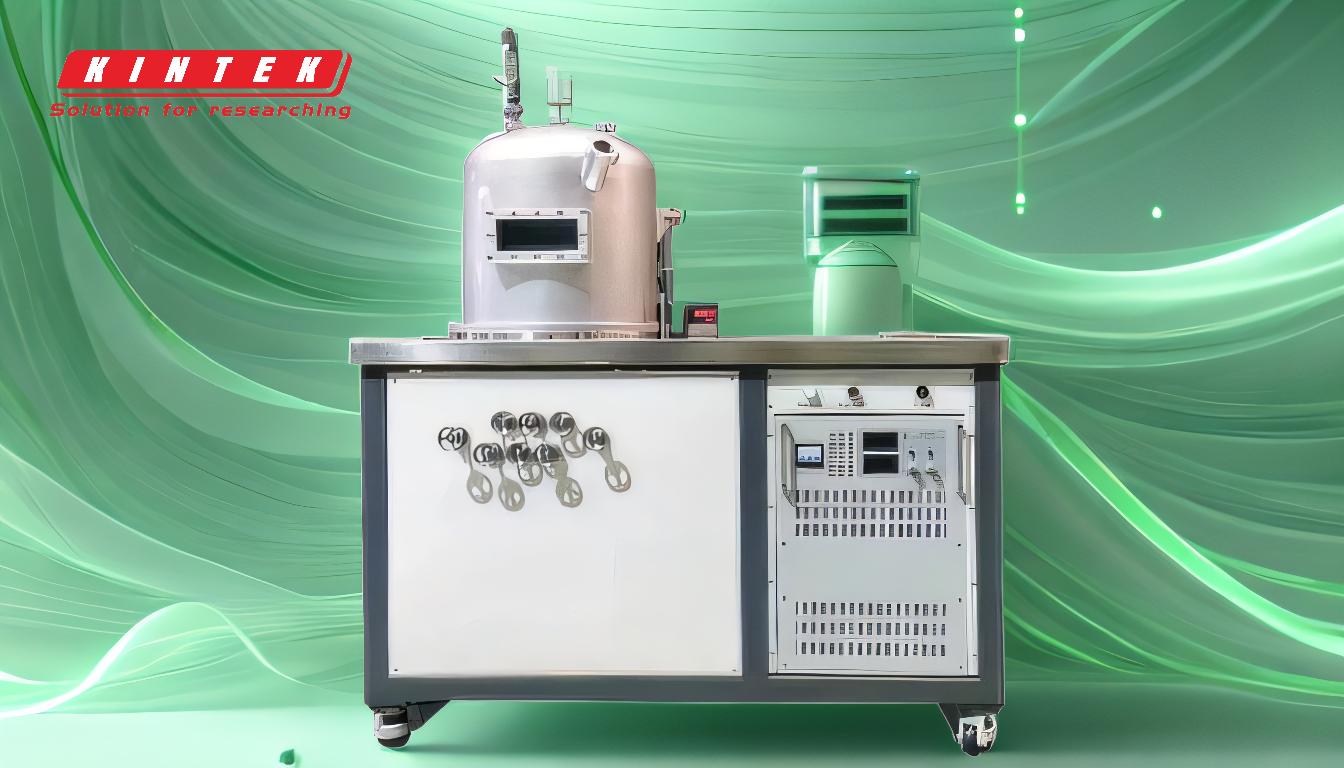
-
Film Contamination:
- Impurities from Source Materials: During the sputtering process, impurities from the source materials can diffuse into the film, leading to contamination. This is particularly problematic when the source materials contain volatile impurities that evaporate and deposit onto the substrate.
- Gaseous Contaminants: The plasma used in sputtering can activate gaseous contaminants, which then become incorporated into the growing film, further increasing the risk of contamination.
- Inert Gas Impurities: Inert sputtering gases, such as argon, can also become impurities in the film if they are not effectively removed from the deposition chamber.
-
Low Deposition Rates:
- Compared to Thermal Evaporation: Sputtering generally has lower deposition rates compared to thermal evaporation techniques. This can result in longer processing times, which may not be suitable for high-throughput production environments.
- Non-Uniform Deposition Flux: The distribution of sputtered atoms is often non-uniform, requiring the use of moving fixtures or other methods to achieve a uniform film thickness across the substrate.
-
Energy Consumption and Heat Management:
- High Energy Costs: A significant portion of the energy incident on the target is converted into heat, which must be effectively removed to prevent damage to the equipment and maintain process stability. This necessitates the use of cooling systems, which increase energy consumption and operational costs.
- Cooling System Requirements: The need for cooling systems not only adds to the energy costs but also decreases the overall production rate, as the system must periodically cool down to avoid overheating.
-
Control Over Film Thickness:
- Difficulty in Layer-by-Layer Growth: Sputtering is less effective for achieving precise layer-by-layer growth compared to other deposition methods like pulsed laser deposition. This makes it challenging to control the film thickness accurately, especially for complex multilayer structures.
- Diffuse Transport of Sputtered Atoms: The diffuse nature of the sputtered atom transport makes it difficult to achieve full shadowing, which is necessary for certain film structuring techniques like lift-off processes.
-
Material Selection and Target Costs:
- Limitations Based on Melting Temperature: The selection of coating materials is often limited by their melting temperatures. Materials with very high melting points may not be suitable for sputtering, as they require higher energy input and can lead to increased contamination risks.
- Expensive Targets: Sputtering targets are often expensive, and the material use can be inefficient, as not all of the sputtered material is deposited onto the substrate. This inefficiency increases the overall cost of the process.
-
Process Parameters and Maintenance:
- High Operating Pressures: Traditional sputtering processes typically operate at higher pressures, which can lead to issues such as permeation through elastomer seals and difficulties in maintaining a stable vacuum environment.
- User-Supplied Maintenance: The sputtering process requires regular maintenance, which can be both time-consuming and costly. The need for user-supplied maintenance adds to the operational complexity and can impact the overall efficiency of the process.
-
Reactive Sputtering Challenges:
- Gas Composition Control: In reactive sputter deposition, the gas composition must be carefully controlled to prevent target poisoning, where the target material reacts with the reactive gas, forming a compound that reduces the sputtering rate and affects film quality.
- Uniformity Issues: For large rectangular cathodes (greater than 1 meter), achieving uniform plasma density and, consequently, uniform layer thickness distribution can be challenging. This non-uniformity can lead to variations in film properties across the substrate.
In summary, while sputtering is a versatile and widely used thin film deposition technique, it is not without its limitations. These include issues related to film contamination, low deposition rates, high energy consumption, difficulties in controlling film thickness, and challenges in material selection. Additionally, the process can be expensive due to the need for specialized equipment and maintenance. Understanding these limitations is essential for optimizing the sputtering process and selecting the appropriate deposition method for specific applications.
Summary Table:
Limitation | Key Details |
---|---|
Film Contamination | Impurities from source materials, gaseous contaminants, inert gas impurities. |
Low Deposition Rates | Slower than thermal evaporation, non-uniform deposition flux. |
High Energy Consumption | Significant heat generation, requires cooling systems, increases operational costs. |
Control Over Film Thickness | Difficulty in layer-by-layer growth, diffuse transport of sputtered atoms. |
Material Selection | Limited by melting temperatures, expensive targets, inefficient material use. |
Process Parameters | High operating pressures, user-supplied maintenance, complex operational needs. |
Reactive Sputtering Challenges | Gas composition control, uniformity issues in large cathodes. |
Need help optimizing your sputtering process? Contact our experts today for tailored solutions!