The sputtering process, while widely used for thin film deposition, has several limitations that impact its efficiency, quality, and applicability. These limitations include low deposition rates, high substrate heating effects, challenges with insulating materials, film contamination, difficulty in controlling film thickness, and issues related to vacuum system realities. Additionally, sputtering faces constraints in material selection, temperature management, and achieving uniform coatings. These factors collectively affect the process's suitability for certain applications and its overall production efficiency.
Key Points Explained:
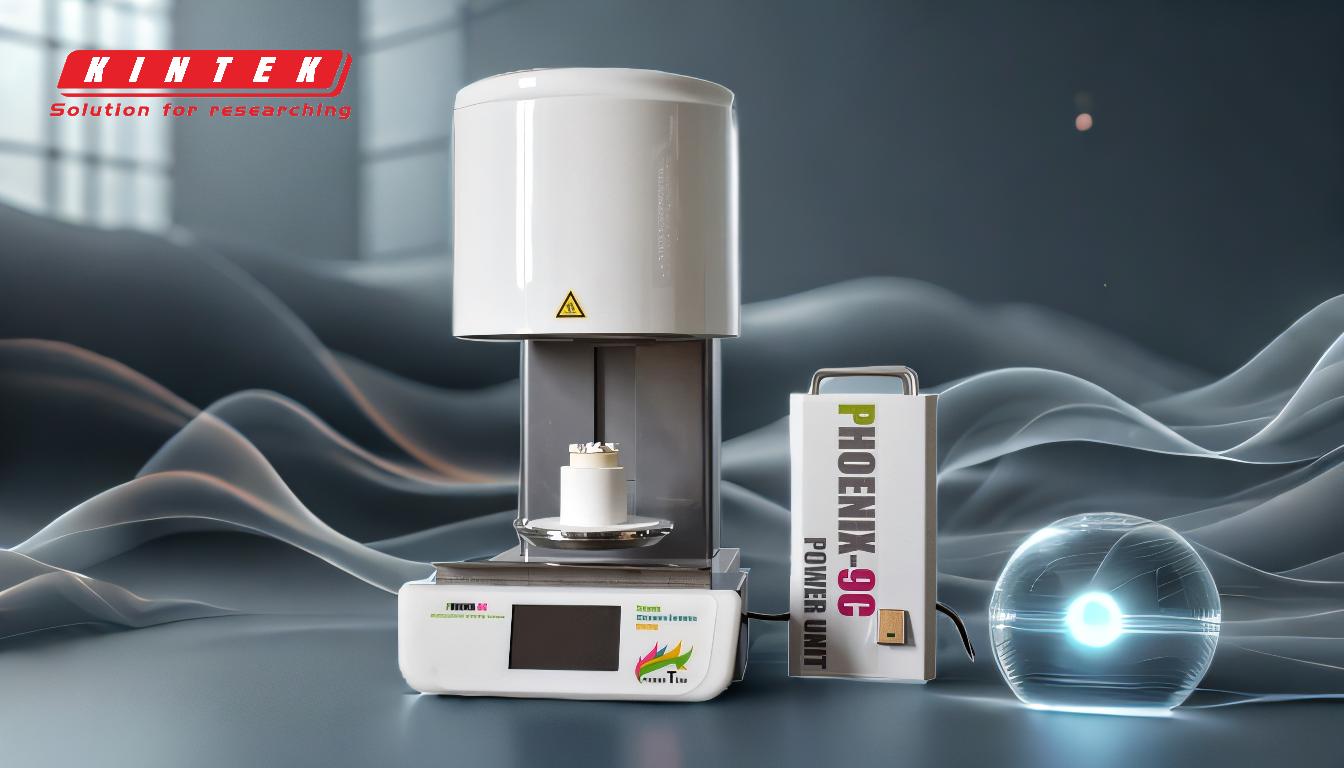
-
Low Deposition Rates:
- Sputtering typically has lower deposition rates compared to other thin film deposition techniques like evaporation. This can lead to longer processing times, reducing throughput and increasing production costs.
- The slow deposition rate is due to the physical nature of the sputtering process, where atoms are ejected from a target material and then deposited onto a substrate.
-
High Substrate Heating Effects:
- The sputtering process generates significant heat, which can cause thermal stress and damage to temperature-sensitive substrates.
- High substrate heating may also lead to undesirable changes in the material properties of the deposited film, such as increased grain size or altered crystallinity.
-
Unsuitability for Insulating Materials:
- Sputtering is less effective for depositing insulating materials because the buildup of charge on the target surface can disrupt the process.
- This limitation necessitates the use of additional techniques, such as RF (radio frequency) sputtering, which increases complexity and cost.
-
Film Contamination:
- Impurities from the target material or the sputtering environment can contaminate the deposited film, affecting its purity and performance.
- Contamination can arise from the diffusion of impurities during the sputtering process or from the use of inert sputtering gases that may become trapped in the film.
-
Difficulty in Controlling Film Thickness:
- Achieving precise control over film thickness is challenging in sputtering due to the diffuse nature of the ejected atoms.
- This lack of control can lead to non-uniform coatings, which may not meet the stringent requirements of certain applications.
-
Vacuum System Limitations:
- The sputtering process requires a high vacuum environment, which imposes limitations on process parameters and increases operational complexity.
- Maintaining the vacuum system and ensuring its proper functioning can be costly and time-consuming.
-
Material Selection Constraints:
- The choice of coating materials is limited by their melting temperatures and other physical properties.
- Materials with very high melting points may not be suitable for sputtering, restricting the range of applications.
-
Temperature Constraints and Stress Issues:
- Temperature management during deposition is critical, as excessive heat can cause undesirable stresses during cooling.
- These stresses can lead to film cracking or delamination, compromising the integrity of the coating.
-
Challenges in Achieving Uniform Thickness and Purity:
- Uniformity in film thickness and purity is difficult to achieve, especially over large areas or complex geometries.
- Non-uniform coatings can result in inconsistent performance and may require additional post-processing steps to correct.
-
Integration with Lift-Off Processes:
- Sputtering is not easily combined with lift-off processes used for patterning films, as the diffuse transport of sputtered atoms makes full shadowing impossible.
- This limitation can lead to contamination and patterning issues, reducing the effectiveness of the sputtering process for certain applications.
-
Energy and Maintenance Costs:
- The need for cooling systems to manage substrate heating increases energy consumption and production costs.
- Regular maintenance of the vacuum system and other components further adds to the operational expenses.
In summary, while sputtering is a versatile and widely used technique for thin film deposition, it is not without its limitations. These include issues related to deposition rates, substrate heating, material selection, film contamination, and process control. Understanding these limitations is crucial for optimizing the sputtering process and selecting the most appropriate deposition method for specific applications.
Summary Table:
Limitation | Description |
---|---|
Low Deposition Rates | Slower than other methods, increasing production time and costs. |
High Substrate Heating Effects | Causes thermal stress and alters material properties. |
Unsuitability for Insulators | Requires RF sputtering, adding complexity and cost. |
Film Contamination | Impurities affect film purity and performance. |
Difficulty in Thickness Control | Leads to non-uniform coatings, impacting application suitability. |
Vacuum System Limitations | High vacuum requirements increase operational complexity and costs. |
Material Selection Constraints | Limited by melting temperatures and physical properties. |
Temperature and Stress Issues | Excessive heat causes film cracking or delamination. |
Uniformity Challenges | Hard to achieve over large areas or complex geometries. |
Integration with Lift-Off | Difficult to combine with patterning processes, leading to contamination. |
Energy and Maintenance Costs | Cooling systems and vacuum maintenance increase operational expenses. |
Need help optimizing your sputtering process? Contact our experts today for tailored solutions!