A carbon regeneration kiln is a sophisticated piece of equipment designed to restore the adsorptive capacity of activated carbon by removing contaminants through thermal regeneration. The kiln consists of several critical components that work together to ensure efficient and controlled regeneration. These include structural elements like the base frame and heating cabinet, functional components such as the heat source and retort tube, and operational systems like the dewatering feed screw arrangement and control panel. Each part plays a vital role in the overall functionality and performance of the kiln.
Key Points Explained:
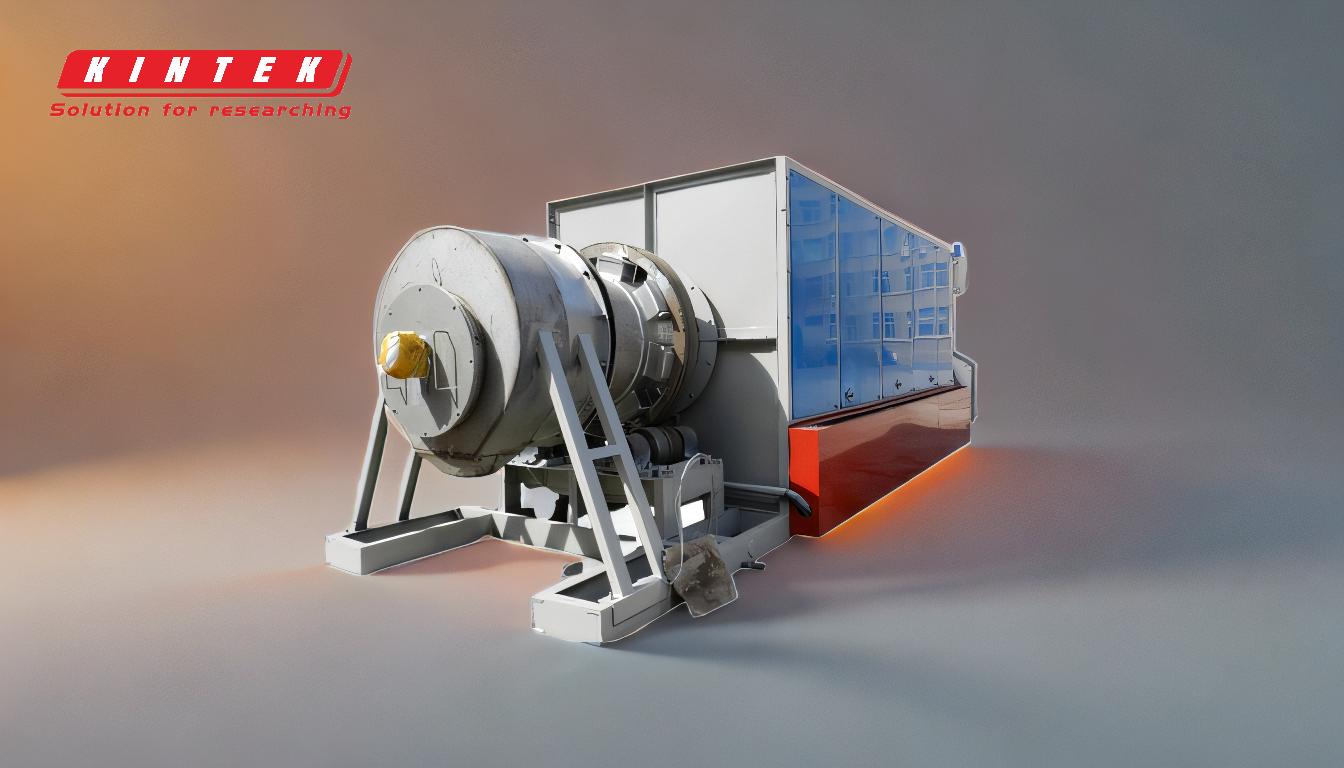
-
Base Frame
- The base frame serves as the foundational structure of the kiln, providing stability and support for all other components.
- It is typically constructed from durable materials like steel to withstand high temperatures and mechanical stress.
- The design ensures proper alignment and integration of other parts, such as the heating cabinet and support rollers.
-
Heating Cabinet
- The heating cabinet houses the heat source and other critical elements responsible for generating and maintaining the high temperatures required for carbon regeneration.
- It is insulated to minimize heat loss and improve energy efficiency.
- The cabinet's design allows for controlled airflow and temperature distribution, ensuring uniform heating of the carbon.
-
Heat Source
- The heat source is the core component responsible for generating the thermal energy needed to remove contaminants from the activated carbon.
- Common heat sources include electric heaters, gas burners, or indirect heating systems.
- The choice of heat source depends on factors like energy efficiency, cost, and the specific requirements of the regeneration process.
-
Dewatering Feed Screw Arrangement
- This system is designed to feed the spent carbon into the kiln while removing excess moisture.
- It includes a variable throughput drive, allowing operators to adjust the feed rate based on the carbon's condition and the desired regeneration parameters.
- The dewatering process ensures that the carbon enters the kiln in an optimal state, reducing energy consumption and improving regeneration efficiency.
-
Discharge Hopper
- The discharge hopper collects the regenerated carbon after it exits the retort tube.
- It is designed to handle high temperatures and prevent contamination of the regenerated carbon.
- The hopper may include cooling mechanisms to reduce the carbon's temperature before further processing or storage.
-
Main and Back-Up Drive Units
- These units are responsible for driving the retort tube and other moving parts within the kiln.
- The main drive unit operates during normal conditions, while the back-up drive ensures continuous operation in case of a failure.
- Both units are designed for reliability and precise control, ensuring smooth and consistent operation of the kiln.
-
Retort Tube
- The retort tube is the chamber where the actual regeneration of the carbon takes place.
- It is typically made from heat-resistant materials like stainless steel or ceramic to withstand high temperatures and chemical reactions.
- The tube's design ensures uniform heating and controlled residence time, critical for effective regeneration.
-
Support Rollers
- Support rollers are used to stabilize and rotate the retort tube during operation.
- They are designed to handle the weight of the tube and the carbon load while minimizing friction and wear.
- Proper alignment and maintenance of the rollers are essential for the kiln's smooth operation.
-
Fully Integrated Control Panel
- The control panel is the brain of the kiln, providing operators with the tools to monitor and adjust key parameters such as temperature, feed rate, and residence time.
- It includes sensors, displays, and control interfaces to ensure precise and automated operation.
- The integration of advanced control systems enhances the kiln's efficiency, safety, and ease of use.
Each of these components plays a crucial role in ensuring the carbon regeneration kiln operates efficiently and delivers high-quality regenerated carbon. Understanding the function and importance of each part helps in making informed decisions during the selection, operation, and maintenance of the equipment.
Summary Table:
Component | Function |
---|---|
Base Frame | Provides structural stability and support for the kiln. |
Heating Cabinet | Houses the heat source and ensures uniform heating of the carbon. |
Heat Source | Generates thermal energy to remove contaminants from the carbon. |
Dewatering Feed Screw | Feeds spent carbon into the kiln while removing excess moisture. |
Discharge Hopper | Collects regenerated carbon and may include cooling mechanisms. |
Main/Back-Up Drive Units | Drives the retort tube and ensures continuous operation. |
Retort Tube | Chamber where carbon regeneration occurs, ensuring uniform heating. |
Support Rollers | Stabilize and rotate the retort tube during operation. |
Control Panel | Monitors and adjusts temperature, feed rate, and residence time. |
Discover how a carbon regeneration kiln can enhance your operations—contact our experts today!