Autoclaving is a critical sterilization process used in various industries, particularly in healthcare and laboratory settings, to eliminate microbial life. The process relies on three fundamental components: pressure, temperature, and time. These components work synergistically to create saturated steam, which effectively kills microorganisms, including resistant spore forms. Pressure increases the boiling point of water, allowing higher temperatures to be achieved, while the moisture in the steam denatures microbial proteins, ensuring thorough sterilization. Understanding these components is essential for optimizing autoclave performance and achieving reliable sterilization outcomes.
Key Points Explained:
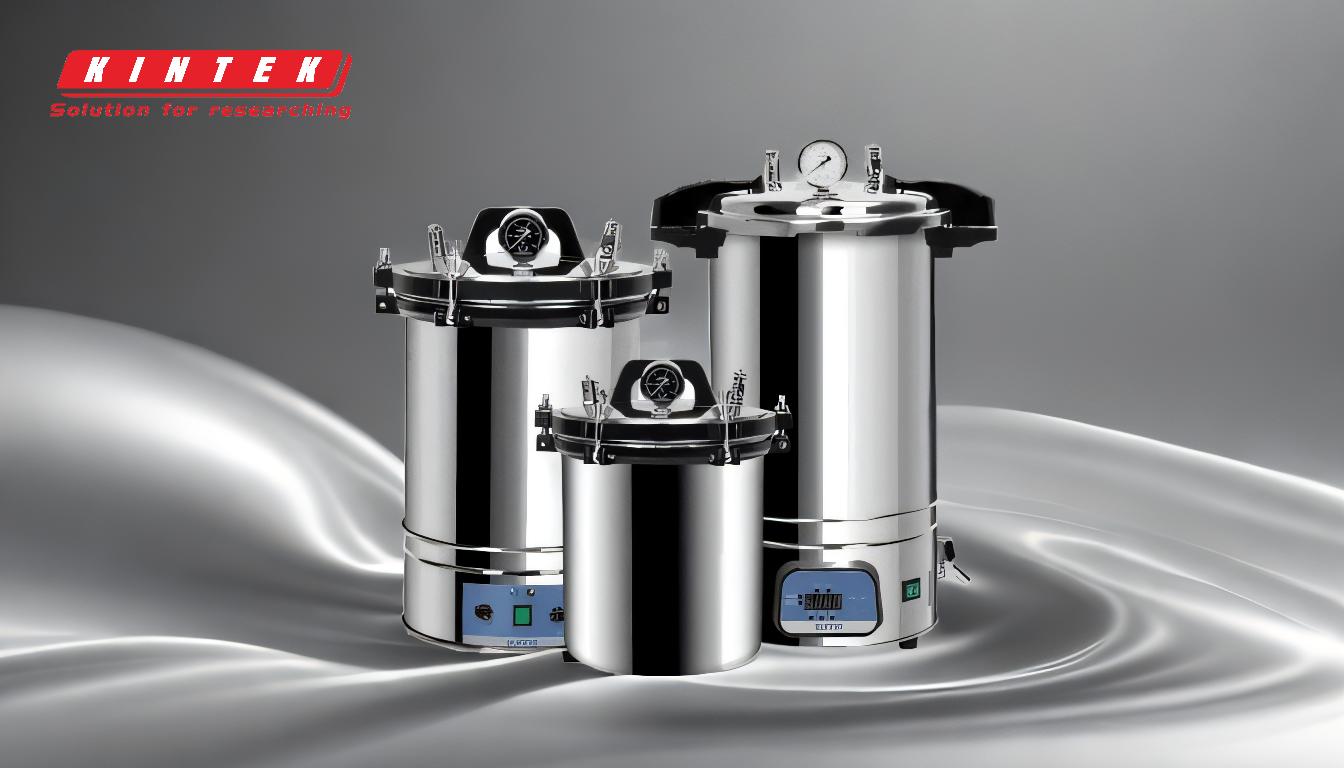
-
Pressure:
- Role in Autoclaving: Pressure is a critical factor in autoclaving because it directly influences the boiling point of water. By increasing the pressure inside the autoclave chamber, the boiling point of water rises above its normal 100°C (212°F). This allows the autoclave to achieve higher temperatures, typically around 121°C (250°F) or 132°C (270°F), which are necessary for effective sterilization.
- Mechanism: The pressure chamber, a core component of the autoclave, is designed to withstand high pressures. It consists of an inner chamber where the items to be sterilized are placed and an outer jacket that helps maintain the pressure and temperature. The pressure gauge monitors the internal pressure, ensuring it remains within safe and effective limits.
- Impact on Sterilization: Higher pressure ensures that the steam remains in a saturated state, which is essential for penetrating and sterilizing porous materials, such as fabrics or surgical instruments. Without adequate pressure, the steam would not reach the required temperature, compromising the sterilization process.
-
Temperature:
- Role in Autoclaving: Temperature is the primary agent of sterilization in an autoclave. The high temperatures achieved under pressure are lethal to microorganisms, including bacteria, viruses, fungi, and spores. The heat denatures proteins and disrupts cellular structures, rendering the microbes non-viable.
- Optimal Range: For most sterilization processes, the temperature is maintained between 121°C and 132°C. The exact temperature depends on the type of autoclave and the materials being sterilized. The steam generator, another key component, heats water to produce the superheated steam required to achieve these temperatures.
- Control and Monitoring: The control panel and thermometer ensure that the temperature is accurately regulated and maintained throughout the sterilization cycle. Consistent temperature control is crucial to avoid under-sterilization, which could leave contaminants alive, or over-sterilization, which might damage sensitive materials.
-
Time:
- Role in Autoclaving: Time is the third critical component, as it determines how long the materials are exposed to the high-pressure, high-temperature steam. The duration of exposure ensures that all microbial life, including heat-resistant spores, is effectively killed.
- Sterilization Cycle: The sterilization cycle typically lasts between 15 to 30 minutes, depending on the load size, type of materials, and the specific autoclave settings. The cycle includes phases such as heating, holding (maintaining the desired temperature and pressure), and cooling. Proper timing ensures that heat penetrates all parts of the load, including the center of dense materials.
- Importance of Timing: Insufficient exposure time can result in incomplete sterilization, while excessive time may damage heat-sensitive items. The autoclave's control system, including timers and software, ensures that the process adheres to the required time parameters.
Integration of Components:
The three components—pressure, temperature, and time—are interdependent and must be carefully balanced to achieve effective sterilization. For example, higher pressure allows for higher temperatures, which in turn reduces the required sterilization time. However, each component must be precisely controlled to avoid compromising the process. Modern autoclaves are equipped with advanced control systems, including sensors and software, to automate and optimize these parameters, ensuring consistent and reliable sterilization outcomes.
Practical Considerations for Equipment Purchasers:
When selecting an autoclave, it is essential to consider how well the equipment manages these three components. Look for features such as:
- Precise Pressure and Temperature Controls: Ensure the autoclave can maintain consistent pressure and temperature levels throughout the cycle.
- Programmable Timers: The ability to set and adjust sterilization times for different loads.
- Safety Features: Pressure release valves, safety valves, and cooling systems to prevent accidents and ensure user safety.
- Capacity and Compatibility: Choose an autoclave with a chamber size and configuration suitable for your specific needs, whether for laboratory glassware, surgical instruments, or other materials.
By understanding the interplay of pressure, temperature, and time, purchasers can make informed decisions and select autoclaves that meet their sterilization requirements effectively and efficiently.
Summary Table:
Component | Role in Autoclaving | Key Details |
---|---|---|
Pressure | Increases boiling point of water for higher temperatures. | - Maintains saturated steam for penetration. |
Temperature | Primary agent for killing microorganisms. | - Optimal range: 121°C to 132°C. |
Time | Ensures exposure to high-pressure, high-temperature steam for complete sterilization. | - Cycle duration: 15-30 minutes depending on load. |
Ready to optimize your sterilization process? Contact us today to find the perfect autoclave for your needs!