Continuous flow reactors are a category of chemical reactors designed for processes where reactants flow continuously through the system, offering advantages such as higher efficiency, better control over reaction conditions, and scalability. The three primary types of continuous flow reactors are Plug Flow Reactors (PFR), Continuous Stirred-Tank Reactors (CSTR), and Loop Reactors. Each type has unique characteristics and applications, making them suitable for different industrial and laboratory processes. Below, we explore these reactors in detail, highlighting their design, functionality, and advantages.
Key Points Explained:
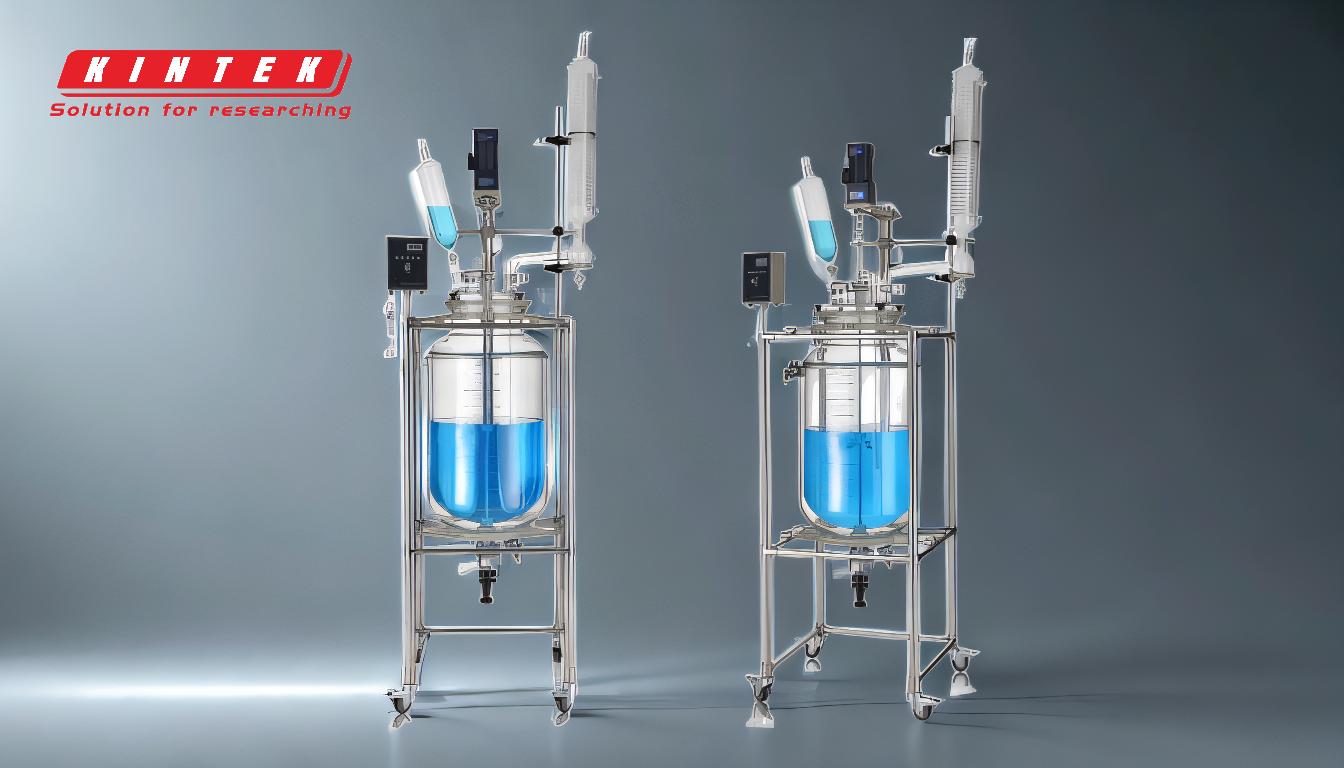
-
Plug Flow Reactor (PFR)
-
Design and Functionality:
- A PFR is a tubular reactor where reactants flow through a pipe or tube, and the reaction progresses as the mixture moves along the length of the reactor.
- The concentration of reactants decreases along the length of the reactor, while the concentration of products increases.
- The flow is ideally "plug-like," meaning there is minimal mixing in the axial direction, but perfect mixing in the radial direction.
-
Advantages:
- High conversion rates due to the continuous gradient of reactant concentration.
- Suitable for reactions requiring precise control of residence time.
- Ideal for gas-phase reactions and large-scale industrial processes.
-
Applications:
- Petrochemical industries, such as cracking of hydrocarbons.
- Polymerization processes.
- Environmental engineering, such as wastewater treatment.
-
Design and Functionality:
-
Continuous Stirred-Tank Reactor (CSTR)
-
Design and Functionality:
- A CSTR consists of a tank with an agitator to ensure uniform mixing of reactants.
- Reactants are continuously fed into the tank, and the product mixture is continuously removed.
- The composition of the mixture is uniform throughout the reactor due to thorough mixing.
-
Advantages:
- Easy to control and maintain steady-state conditions.
- Suitable for reactions requiring constant temperature and concentration.
- Scalable for industrial applications.
-
Applications:
- Fermentation processes in biotechnology.
- Chemical synthesis, such as production of esters and other organic compounds.
- Waste treatment processes.
-
Design and Functionality:
-
Loop Reactor
-
Design and Functionality:
- A loop reactor is a hybrid design that combines features of both PFR and CSTR.
- It consists of a closed-loop system where reactants circulate continuously through a loop, often with a pump or agitator to maintain flow.
- The reaction occurs as the mixture circulates, and the system can be designed to achieve specific mixing and residence time characteristics.
-
Advantages:
- Enhanced heat and mass transfer due to continuous circulation.
- Flexible design for optimizing reaction conditions.
- Suitable for reactions requiring high mixing efficiency.
-
Applications:
- Polymerization processes, such as production of polyethylene.
- Hydrogenation reactions in the pharmaceutical industry.
- Continuous fermentation in biotechnology.
-
Design and Functionality:
Comparison of Continuous Flow Reactors:
Feature | Plug Flow Reactor (PFR) | Continuous Stirred-Tank Reactor (CSTR) | Loop Reactor |
---|---|---|---|
Mixing | Minimal axial mixing | Perfect mixing | Controlled mixing in a loop |
Residence Time | Variable along the reactor | Uniform throughout the reactor | Adjustable via circulation rate |
Scalability | High | Moderate to high | High |
Applications | Gas-phase reactions, large-scale | Fermentation, chemical synthesis | Polymerization, hydrogenation |
Why Choose Continuous Flow Reactors?
- Efficiency: Continuous flow reactors often achieve higher yields and faster reaction times compared to batch reactors.
- Control: They offer precise control over reaction parameters such as temperature, pressure, and residence time.
- Scalability: These reactors are well-suited for scaling up from laboratory to industrial production.
- Cost-Effectiveness: Reduced downtime and lower manufacturing costs make them economically advantageous for high-volume production.
By understanding the unique features and applications of PFRs, CSTRs, and loop reactors, equipment purchasers can make informed decisions tailored to their specific process requirements.
Summary Table:
Feature | Plug Flow Reactor (PFR) | Continuous Stirred-Tank Reactor (CSTR) | Loop Reactor |
---|---|---|---|
Mixing | Minimal axial mixing | Perfect mixing | Controlled mixing in a loop |
Residence Time | Variable along the reactor | Uniform throughout the reactor | Adjustable via circulation rate |
Scalability | High | Moderate to high | High |
Applications | Gas-phase reactions, large-scale | Fermentation, chemical synthesis | Polymerization, hydrogenation |
Ready to choose the right continuous flow reactor for your needs? Contact us today for expert guidance!