A centrifuge is a laboratory instrument that uses centrifugal force to separate components of a solution based on their densities. When a solution is placed in a centrifuge and spun at high speeds, the denser particles move outward and settle at the bottom, while less dense components remain closer to the top. This process is essential for isolating specific substances, such as cells, proteins, or DNA, from a mixture. Centrifugation is widely used in scientific research, medical diagnostics, and industrial applications to purify, concentrate, or analyze materials. The efficiency of separation depends on factors like rotor speed, solution viscosity, and particle size.
Key Points Explained:
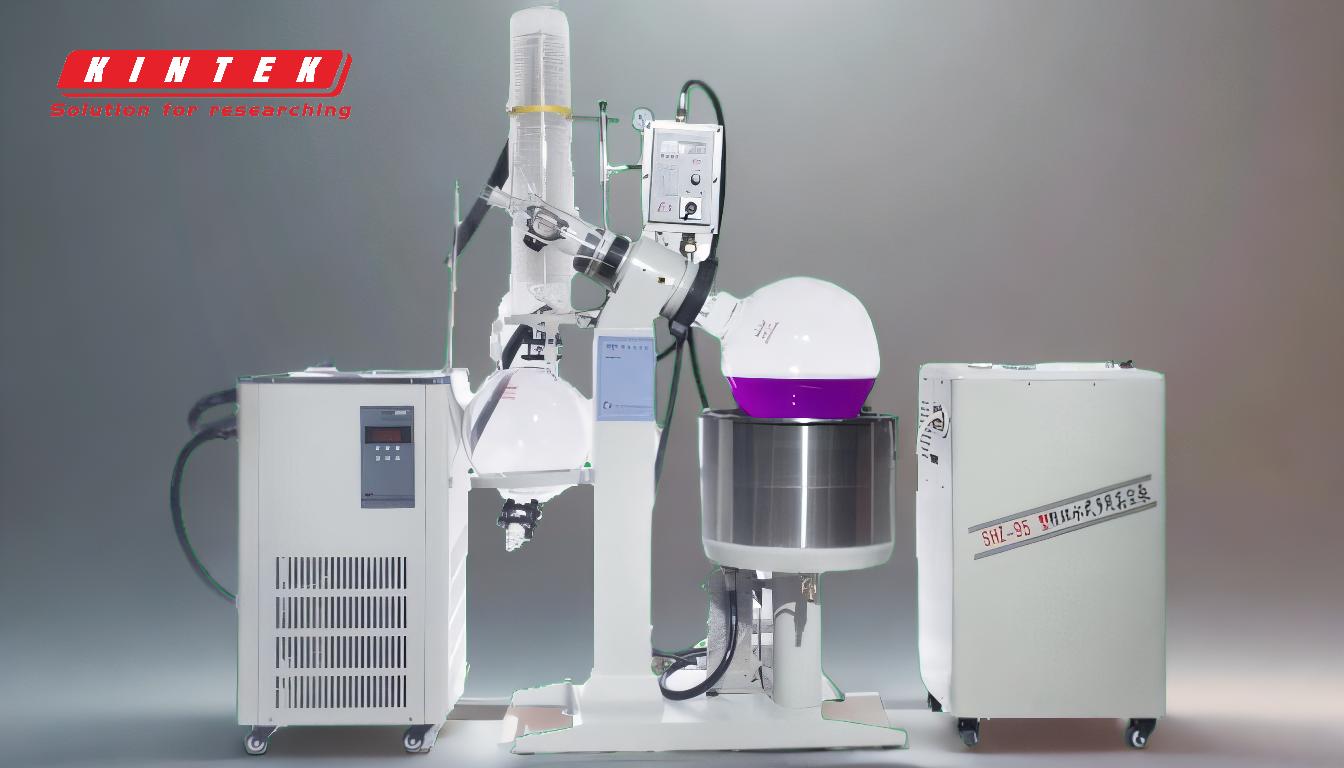
-
Principle of Centrifugation:
- Centrifugation relies on the principle of centrifugal force, which is the outward force experienced by an object moving in a circular path. When a solution is spun in a centrifuge, this force causes denser particles to move outward and settle at the bottom of the tube, while lighter components remain suspended or float.
- This separation is based on differences in density, size, and shape of the particles in the solution.
-
Components of a Centrifuge:
- A centrifuge consists of a rotor, which holds the sample tubes, and a motor that spins the rotor at high speeds. The rotor can be fixed-angle or swinging-bucket, depending on the application.
- The speed of the rotor, measured in revolutions per minute (RPM) or relative centrifugal force (RCF), determines the effectiveness of the separation.
-
Applications of Centrifugation:
- Biological Research: Used to separate cells, organelles, and macromolecules like DNA, RNA, and proteins from complex mixtures.
- Medical Diagnostics: Employed in blood tests to separate plasma or serum from blood cells.
- Industrial Processes: Utilized in wastewater treatment, oil refining, and pharmaceutical manufacturing to isolate specific components.
-
Types of Centrifugation:
- Differential Centrifugation: Separates particles based on size and density differences. Commonly used in cell biology to isolate organelles.
- Density Gradient Centrifugation: Uses a gradient medium (e.g., sucrose or cesium chloride) to separate particles with similar densities. Ideal for purifying viruses or nucleic acids.
- Ultracentrifugation: Operates at extremely high speeds to separate very small particles, such as proteins or lipoproteins.
-
Factors Affecting Centrifugation:
- Rotor Speed: Higher speeds generate greater centrifugal force, improving separation efficiency.
- Solution Viscosity: Thicker solutions require longer centrifugation times or higher speeds.
- Particle Size and Density: Larger or denser particles settle faster than smaller or less dense ones.
-
Advantages of Centrifugation:
- Provides a quick and efficient method for separating components in a solution.
- Can handle small to large sample volumes, depending on the centrifuge type.
- Versatile and applicable across various scientific and industrial fields.
-
Limitations of Centrifugation:
- High-speed centrifugation can generate heat, potentially damaging sensitive samples.
- Requires careful balancing of tubes to avoid rotor damage or imbalance.
- Not suitable for separating particles with very similar densities.
-
Safety Considerations:
- Always balance the centrifuge by placing tubes of equal weight opposite each other.
- Use appropriate rotor speeds and centrifugation times to prevent sample degradation.
- Regularly inspect and maintain the centrifuge to ensure safe operation.
By understanding how a centrifuge works and its applications, users can effectively separate and analyze components in a solution, making it an indispensable tool in laboratories and industries.
Summary Table:
Aspect | Details |
---|---|
Principle | Uses centrifugal force to separate particles by density, size, and shape. |
Components | Rotor (fixed-angle or swinging-bucket) and motor for high-speed spinning. |
Applications | Biological research, medical diagnostics, and industrial processes. |
Types | Differential, density gradient, and ultracentrifugation. |
Factors Affecting | Rotor speed, solution viscosity, particle size, and density. |
Advantages | Quick, efficient, and versatile separation for various sample sizes. |
Limitations | Heat generation, requires balancing, and limited for similar densities. |
Safety Considerations | Balance tubes, use appropriate speeds, and maintain equipment regularly. |
Need a centrifuge for your lab? Contact us today to find the perfect solution!