A sputtered film is a thin layer of material deposited onto a substrate using the sputtering process, a physical vapor deposition (PVD) technique. In this method, a target material (the source of the film) is bombarded with high-energy ions in a vacuum chamber filled with an inert gas, typically argon. The collision of ions with the target ejects atoms or molecules, which then travel through the chamber and deposit onto a substrate, forming a thin, uniform film. Sputtered films are widely used in industries such as electronics, optics, automotive, and decorative applications due to their excellent uniformity, density, purity, and adhesion properties. The process allows precise control over film thickness and can be performed at relatively low temperatures, making it suitable for a variety of materials and applications.
Key Points Explained:
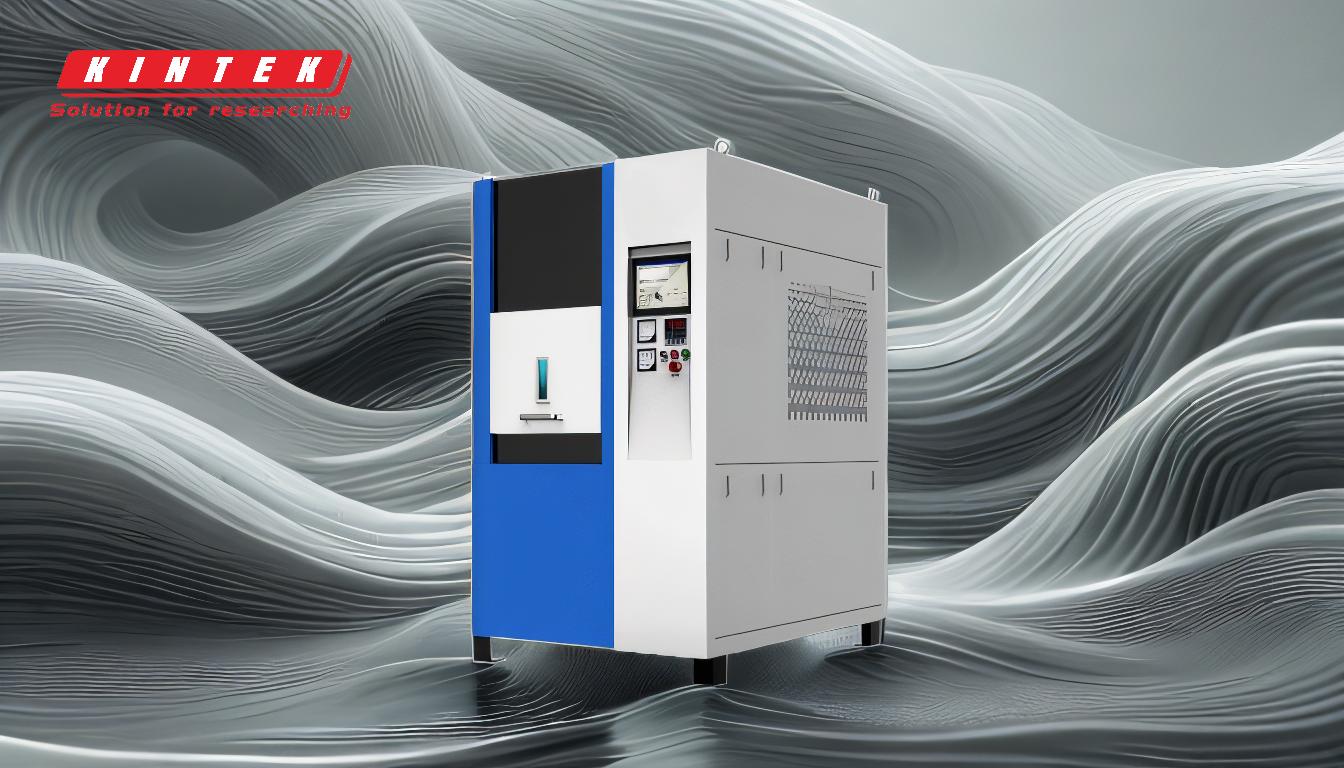
-
Definition of Sputtered Film:
- A sputtered film is a thin layer of material deposited onto a substrate using the sputtering process, a type of physical vapor deposition (PVD).
- The process involves bombarding a target material with high-energy ions, causing atoms or molecules to be ejected and deposited onto a substrate.
-
Sputtering Process:
- Vacuum Chamber: The process takes place in a vacuum chamber to minimize contamination and ensure a controlled environment.
- Inert Gas: An inert gas, typically argon, is introduced into the chamber and ionized to form a plasma.
- Target Material: The target material, which is the source of the film, is placed on a cathode and bombarded with the ionized gas particles.
- Film Formation: The ejected atoms or molecules travel through the chamber and deposit onto the substrate, forming a thin, uniform film.
-
Advantages of Sputtered Films:
- Uniformity: Sputtered films are highly uniform, which is crucial for applications requiring precise thickness control.
- Density: The films are dense, reducing porosity and improving mechanical and optical properties.
- Purity: The process can produce films with high purity, as it occurs in a controlled vacuum environment.
- Adhesion: Sputtered films exhibit excellent adhesion to the substrate, ensuring durability and longevity.
-
Applications of Sputtered Films:
- Electronics: Used for thin-film wiring on chips, recording heads, and magnetic and magneto-optic recording media.
- Optics: Reflective films for architectural glass and decorative films for automotive plastics.
- Decorative: Applications in watchbands, eyeglasses, and jewelry.
- Packaging: Thin plastic films for food packaging.
-
Historical Context:
- Thomas Edison was one of the first to use sputtering commercially in 1904 to apply a thin layer of metal to wax phonograph recordings.
- The process has evolved significantly since then, with advancements in technology and materials.
-
Variations of Sputtering:
- Anodizing: A variation of sputtering used to give aluminum surfaces a uniform, shiny finish and resistance to food sticking.
- Plasma Sputtering: Used in the electronics industry to deposit thin metal films on wafers, which can be etched into wires.
-
Control and Precision:
- The thickness of the sputtered film can be precisely controlled by adjusting the deposition time.
- The process can be performed at lower temperatures, making it suitable for temperature-sensitive materials.
-
Mechanism of Film Formation:
- The sputtering process involves a collision cascade, where ionized gas particles collide with the target material, ejecting atoms or molecules.
- These ejected particles form a vapor stream that deposits onto the substrate, creating a thin film.
-
Material Versatility:
- Sputtering can be used with a wide range of materials, including metals, alloys, and ceramics.
- This versatility makes it suitable for various industrial applications.
-
Future Prospects:
- Ongoing research and development are focused on improving the efficiency and capabilities of the sputtering process.
- Potential future applications include advanced electronics, renewable energy technologies, and biomedical devices.
In summary, sputtered films are a critical component in many modern technologies, offering a combination of precision, versatility, and high-quality film properties. The sputtering process continues to evolve, driven by advancements in materials science and engineering, and holds promise for future innovations across a wide range of industries.
Summary Table:
Aspect | Details |
---|---|
Definition | Thin layer of material deposited using the sputtering process (PVD). |
Process | Bombard target material with ions in a vacuum chamber filled with argon. |
Advantages | Uniformity, density, purity, and excellent adhesion properties. |
Applications | Electronics, optics, automotive, decorative, and packaging industries. |
Control & Precision | Precise thickness control, low-temperature process. |
Material Versatility | Metals, alloys, and ceramics. |
Future Prospects | Advanced electronics, renewable energy, and biomedical devices. |
Interested in sputtered films for your industry? Contact us today to learn more!