Bioreactor design involves several key components, each playing a critical role in ensuring optimal conditions for cell growth, product formation, and process control. The main parts include the vessel, agitator, sparger, temperature control system, pH control system, foam control system, and sensors. The vessel provides a sterile environment for the culture, while the agitator ensures proper mixing and oxygen distribution. The sparger introduces air or oxygen into the culture, and the temperature and pH control systems maintain optimal growth conditions. Foam control prevents overflow, and sensors monitor critical parameters like dissolved oxygen, temperature, and pH. Together, these components ensure efficient and controlled bioprocessing.
Key Points Explained:
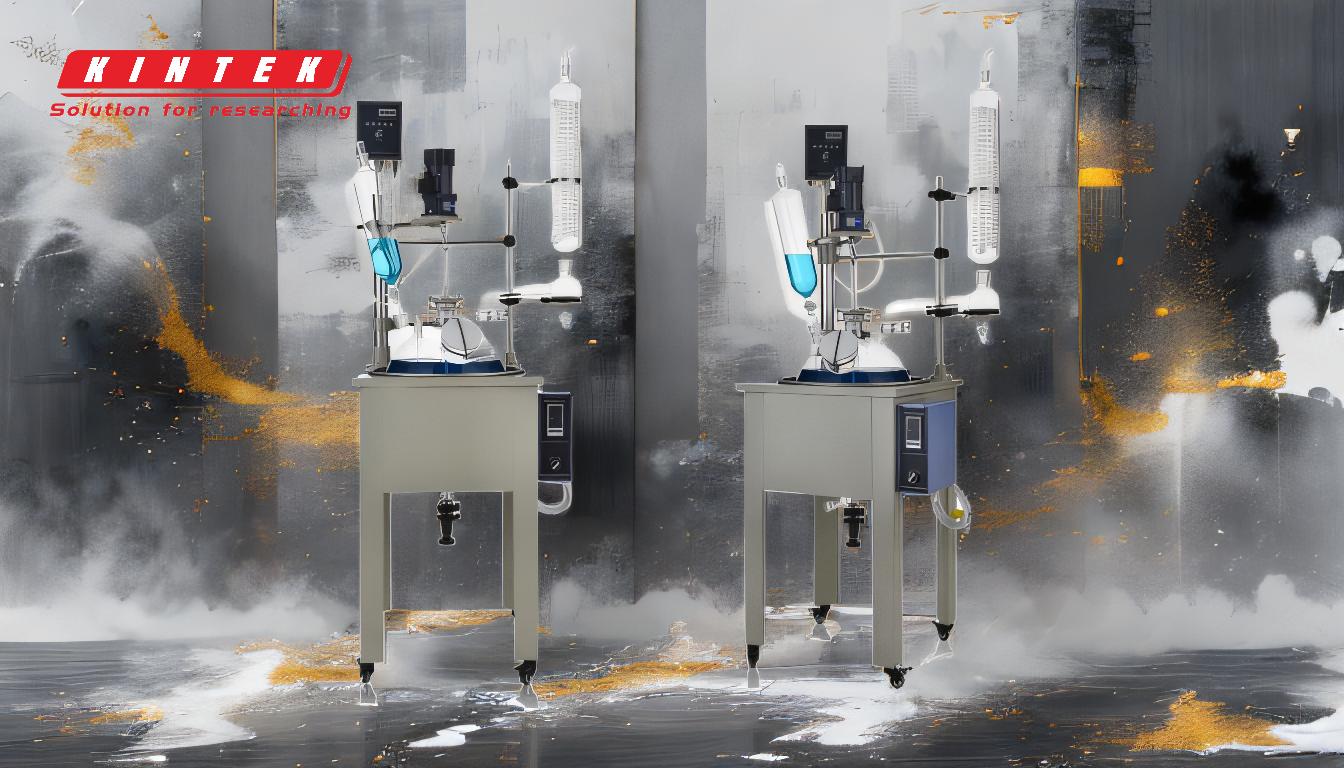
-
Vessel
- Function: The vessel is the core component of a bioreactor, providing a sterile and controlled environment for cell or microbial culture. It is typically made of stainless steel or glass to ensure durability and sterility.
- Importance: The vessel must withstand sterilization processes (e.g., autoclaving) and maintain aseptic conditions to prevent contamination. Its design also influences mixing efficiency and heat transfer.
-
Agitator (Impeller)
- Function: The agitator ensures uniform mixing of the culture medium, preventing sedimentation and maintaining homogeneity. It also aids in oxygen transfer by creating turbulence.
- Types: Common types include Rushton turbines, marine propellers, and pitched blade impellers, each suited for specific mixing requirements.
- Importance: Proper mixing is critical for nutrient distribution, oxygen transfer, and heat dissipation, all of which are essential for cell growth.
-
Sparger
- Function: The sparger introduces air or oxygen into the culture medium, ensuring adequate oxygen supply for aerobic processes. It can also help in mixing the medium.
- Types: Spargers can be porous (e.g., sintered materials) or non-porous (e.g., perforated pipes), depending on the required bubble size and oxygen transfer efficiency.
- Importance: Oxygen is vital for aerobic microorganisms, and the sparger's design directly impacts oxygen transfer rates and overall bioreactor performance.
-
Temperature Control System
- Function: This system maintains the culture at an optimal temperature for cell growth and product formation. It typically includes heating and cooling mechanisms.
- Components: Common components include heating jackets, cooling coils, and temperature sensors.
- Importance: Temperature affects enzyme activity, cell metabolism, and product yield, making precise control essential for consistent bioreactor performance.
-
pH Control System
- Function: The pH control system regulates the acidity or alkalinity of the culture medium, ensuring it remains within the optimal range for cell growth.
- Components: It includes pH probes, acid/base pumps, and controllers.
- Importance: pH influences enzyme activity, nutrient uptake, and cell viability, making its control critical for maintaining a stable culture environment.
-
Foam Control System
- Function: Foam control prevents excessive foam formation, which can lead to contamination, nutrient loss, and overflow.
- Methods: Mechanical foam breakers (e.g., impellers) or chemical antifoaming agents are commonly used.
- Importance: Uncontrolled foam can disrupt operations, damage equipment, and compromise product quality.
-
Sensors and Monitoring Systems
- Function: Sensors monitor critical parameters such as dissolved oxygen, temperature, pH, and biomass concentration in real-time.
- Types: Common sensors include dissolved oxygen probes, pH electrodes, and optical density sensors.
- Importance: Real-time monitoring allows for precise control and optimization of the bioprocess, ensuring consistent product quality and yield.
-
Sterilization System
- Function: Ensures the bioreactor and its components are free from contaminants before and during operation.
- Methods: Common methods include autoclaving, steam sterilization, and chemical sterilization.
- Importance: Sterility is critical to prevent contamination, which can ruin the culture and compromise product integrity.
-
Harvesting System
- Function: Facilitates the collection of the final product, whether it is cells, proteins, or other metabolites.
- Components: Includes pumps, filters, and separation systems (e.g., centrifuges).
- Importance: Efficient harvesting ensures maximum product recovery and minimizes losses.
-
Control System
- Function: Integrates all subsystems (e.g., temperature, pH, agitation) to automate and optimize bioreactor operation.
- Components: Includes programmable logic controllers (PLCs), software interfaces, and feedback loops.
- Importance: Automation improves process consistency, reduces human error, and enhances scalability.
By understanding the function and importance of each bioreactor component, users can make informed decisions when designing or purchasing bioreactors, ensuring they meet specific process requirements and achieve desired outcomes.
Summary Table:
Component | Function | Importance |
---|---|---|
Vessel | Provides a sterile environment for cell or microbial culture. | Ensures durability, sterility, and influences mixing efficiency and heat transfer. |
Agitator (Impeller) | Ensures uniform mixing and oxygen distribution. | Critical for nutrient distribution, oxygen transfer, and heat dissipation. |
Sparger | Introduces air or oxygen into the culture medium. | Vital for aerobic microorganisms and impacts oxygen transfer rates. |
Temperature Control | Maintains optimal temperature for cell growth and product formation. | Affects enzyme activity, cell metabolism, and product yield. |
pH Control | Regulates acidity or alkalinity of the culture medium. | Influences enzyme activity, nutrient uptake, and cell viability. |
Foam Control | Prevents excessive foam formation. | Avoids contamination, nutrient loss, and equipment damage. |
Sensors | Monitors parameters like dissolved oxygen, temperature, and pH in real-time. | Enables precise control and optimization of the bioprocess. |
Sterilization System | Ensures the bioreactor is free from contaminants. | Prevents contamination, ensuring product integrity. |
Harvesting System | Collects the final product (cells, proteins, or metabolites). | Maximizes product recovery and minimizes losses. |
Control System | Automates and integrates all subsystems for optimized operation. | Improves consistency, reduces errors, and enhances scalability. |
Ready to optimize your bioprocessing? Contact our experts today to find the perfect bioreactor solution for your needs!