DC sputtering is a widely used physical vapor deposition (PVD) technique for creating thin films of metal on substrates. It involves bombarding a metal target with ionized gas molecules, typically argon, in a vacuum chamber. The gas ions collide with the target, ejecting (or sputtering) atoms from the target material. These atoms then travel through the plasma and deposit onto a nearby substrate, forming a thin film. DC sputtering is particularly effective for conductive materials and is widely used in industries such as semiconductors, jewelry, and optical components due to its simplicity, cost-effectiveness, and ability to produce uniform coatings.
Key Points Explained:
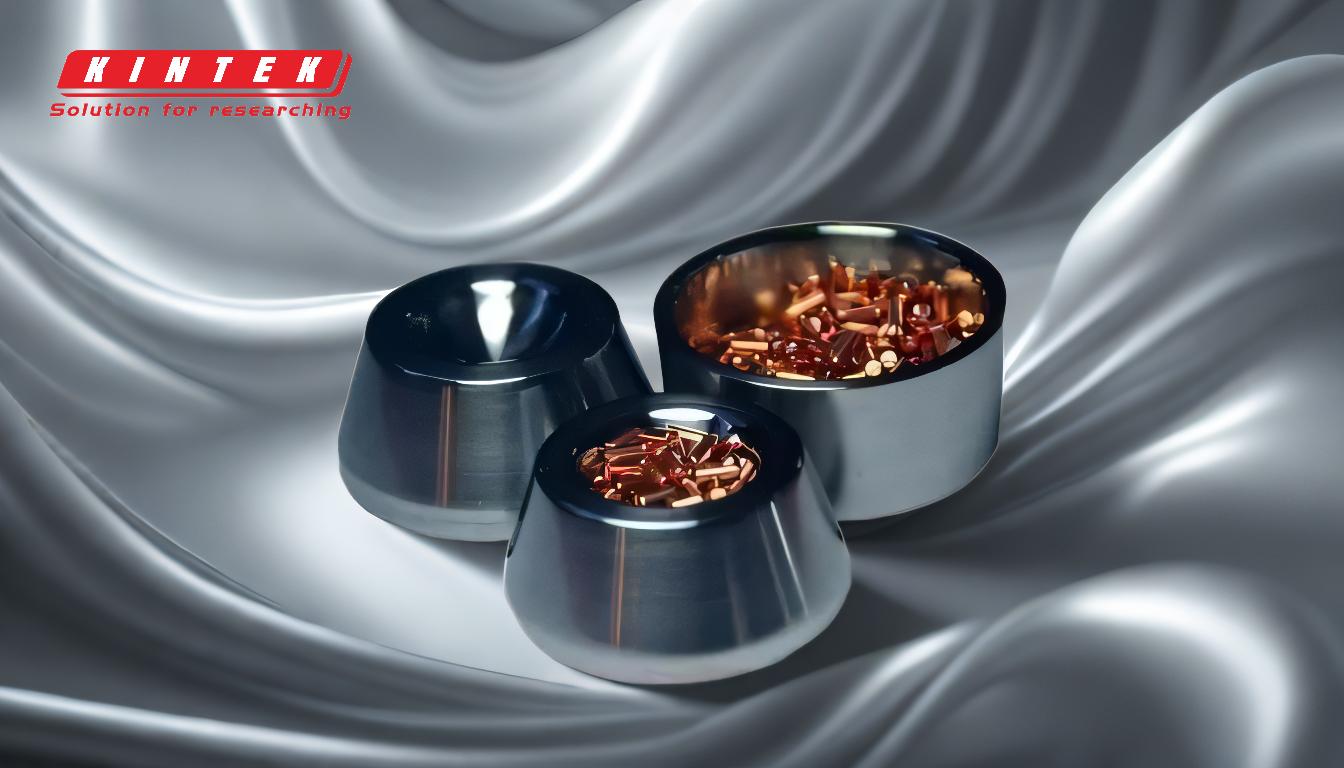
-
Definition of DC Sputtering:
- DC sputtering is a type of physical vapor deposition (PVD) process.
- It involves using a direct current (DC) voltage to create a plasma in a low-pressure inert gas environment, typically argon.
- The process ejects atoms from a metal target, which then deposit onto a substrate to form a thin film.
-
Mechanism of DC Sputtering:
- A vacuum chamber is used to create a low-pressure environment, preventing contamination from air or other gases.
- Argon gas is introduced into the chamber and ionized to form a plasma.
- A DC voltage is applied between the target (cathode) and the substrate (anode).
- Ionized argon atoms are accelerated toward the target, colliding with it and ejecting target atoms.
- The ejected atoms travel through the plasma and deposit onto the substrate, forming a thin film.
-
Key Components of the DC Sputtering System:
- Vacuum Chamber: Ensures a clean, low-pressure environment for the process.
- Target Material: The metal or conductive material to be sputtered.
- Substrate: The surface onto which the thin film is deposited.
- Argon Gas: Used to create the plasma and ionize the gas molecules.
- DC Power Supply: Provides the voltage needed to ionize the gas and accelerate ions toward the target.
-
Advantages of DC Sputtering:
- Cost-Effective: It is one of the simplest and most economical PVD techniques.
- Uniform Coatings: Produces highly uniform thin films with precise control over thickness.
- Versatility: Suitable for a wide range of conductive materials, including metals and alloys.
- Low Temperature: The process operates at low temperatures, making it suitable for heat-sensitive substrates like plastics.
-
Applications of DC Sputtering:
- Semiconductors: Used for depositing conductive layers in microelectronics.
- Jewelry: Creates durable and decorative coatings on jewelry pieces.
- Optical Components: Produces anti-reflective and protective coatings on lenses and mirrors.
- Decorative Coatings: Used for coating consumer products with metallic finishes.
-
Limitations of DC Sputtering:
- Conductive Materials Only: DC sputtering is not suitable for non-conductive materials because the process relies on electron flow.
- Target Erosion: The target material erodes over time, requiring periodic replacement.
- Plasma Instability: At higher pressures, the plasma can become unstable, affecting the quality of the coating.
-
Comparison with Other Sputtering Techniques:
- DC Sputtering vs. RF Sputtering: DC sputtering is limited to conductive materials, while RF sputtering can be used for both conductive and non-conductive materials.
- DC Sputtering vs. Magnetron Sputtering: Magnetron sputtering uses magnetic fields to enhance the efficiency of the sputtering process, making it faster and more energy-efficient than standard DC sputtering.
-
Process Parameters:
- Gas Pressure: The pressure of the argon gas must be carefully controlled to maintain plasma stability.
- Voltage and Current: The applied DC voltage and current determine the energy of the ions and the rate of sputtering.
- Target-Substrate Distance: The distance between the target and substrate affects the uniformity and density of the deposited film.
By understanding these key points, one can appreciate the simplicity, effectiveness, and limitations of DC sputtering as a thin-film deposition technique. Its widespread use in various industries highlights its importance in modern manufacturing and materials science.
Summary Table:
Aspect | Details |
---|---|
Definition | A PVD process using DC voltage to create plasma and deposit thin films. |
Mechanism | Ionized argon atoms collide with a target, ejecting atoms onto a substrate. |
Key Components | Vacuum chamber, target material, substrate, argon gas, DC power supply. |
Advantages | Cost-effective, uniform coatings, versatile, low-temperature operation. |
Applications | Semiconductors, jewelry, optical components, decorative coatings. |
Limitations | Limited to conductive materials, target erosion, plasma instability. |
Process Parameters | Gas pressure, voltage/current, target-substrate distance. |
Discover how DC sputtering can enhance your manufacturing process—contact our experts today for a consultation!