RF sputtering of oxide materials is a specialized thin-film deposition technique that uses radio frequency (RF) energy to create high-quality films, particularly for insulating or dielectric materials like oxides. This method alternates the electrical potential at radio frequencies, preventing charge buildup on insulating targets and enabling the deposition of uniform, high-quality films. It is widely used in industries such as semiconductors, optics, and photonics for applications like optical planar waveguides, photonic microcavities, and 1-D photonic crystals. The process involves alternating positive and negative cycles, where electrons and ions are alternately attracted to the target and substrate, ensuring consistent material deposition without arcing or process interruption.
Key Points Explained:
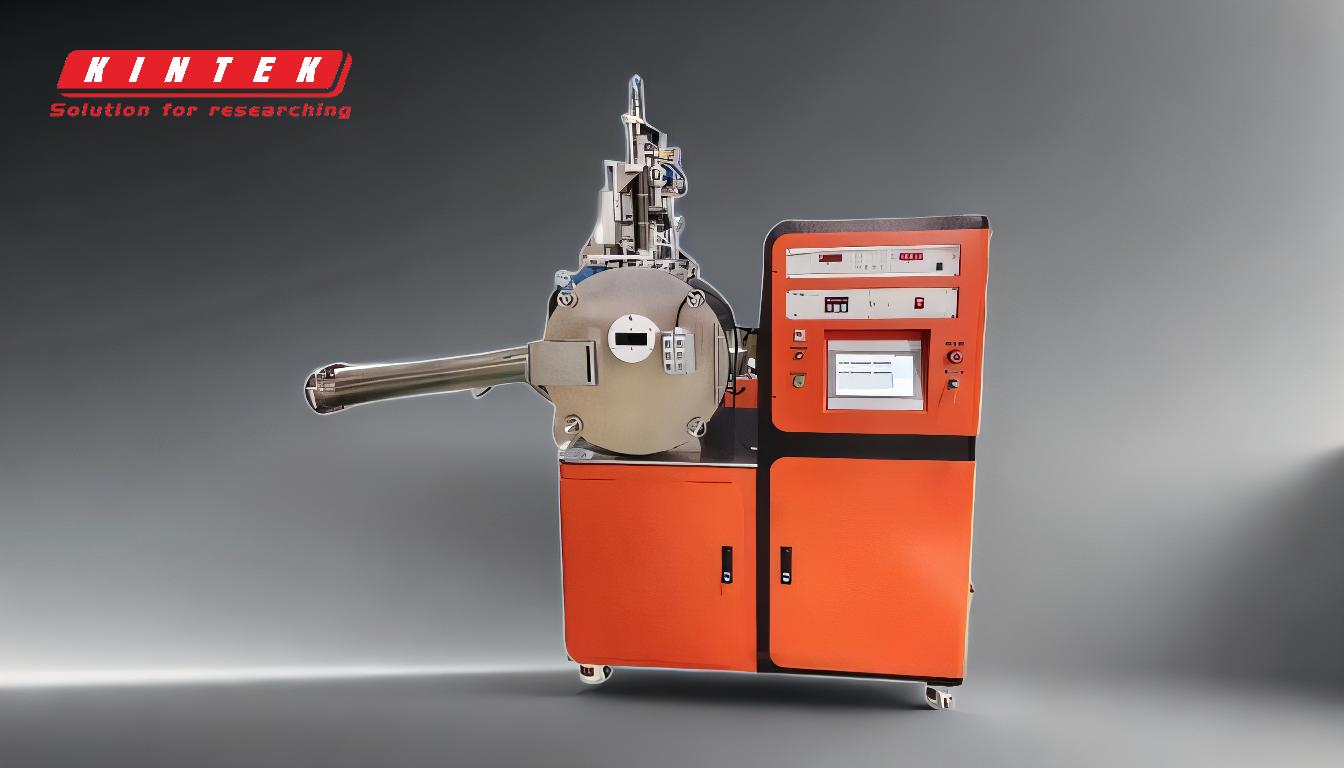
-
Definition and Purpose of RF Sputtering:
- RF sputtering is a thin-film deposition technique that uses radio frequency energy to deposit materials, particularly insulating or dielectric materials like oxides, onto a substrate.
- It is designed to prevent charge buildup on insulating targets, which can cause arcing and disrupt the sputtering process.
- This method is widely used in industries such as semiconductors, optics, and photonics for creating high-quality, uniform films.
-
How RF Sputtering Works:
- The process involves alternating the electrical potential at radio frequencies (typically 13.56 MHz) in a vacuum environment.
- The target material and substrate holder act as two electrodes.
- In the positive cycle, electrons are attracted to the target (cathode), creating a negative bias.
- In the negative cycle, the target acts as a cathode, ejecting gas ions and target atoms toward the substrate to form a film.
- This alternating cycle prevents charge buildup on insulating materials, ensuring a stable and continuous deposition process.
-
Advantages of RF Sputtering for Oxide Materials:
- Prevents Charge Buildup: The alternating current avoids constant negative voltage on the cathode, which is critical for insulating oxide materials.
- High-Quality Films: RF sputtering produces uniform, high-quality films with controlled thickness and refractive index, making it ideal for optical and photonic applications.
- Low Substrate Temperature: It allows for deposition at low temperatures, which is beneficial for temperature-sensitive substrates.
- Versatility: Suitable for depositing alternating layers of different materials, enabling the fabrication of complex structures like 1-D photonic crystals and planar waveguides.
-
Applications of RF Sputtering:
- Optical Planar Waveguides: RF sputtering is used to create waveguides that operate in the visible and near-infrared (NIR) regions.
- Photonic Microcavities: It is ideal for fabricating dielectric microcavities with precise control over refractive index and thickness.
- 1-D Photonic Crystals: The technique is used to deposit alternating layers of materials with different refractive indices, creating high-quality photonic crystals.
- Semiconductor and Computer Industries: RF sputtering is commonly used to deposit thin films in semiconductor devices and computer components.
-
Comparison with DC Sputtering:
- Unlike DC sputtering, which is limited to conductive materials, RF sputtering can deposit insulating materials like oxides.
- RF sputtering avoids the issue of charge buildup, which can cause arcing and disrupt the deposition process in DC sputtering.
- The alternating current in RF sputtering ensures a more stable and consistent deposition process for dielectric materials.
-
Process Parameters and Control:
- Frequency: The RF energy is typically applied at 13.56 MHz, a standard frequency for industrial and scientific applications.
- Gas Environment: An inert gas (e.g., argon) is used to create plasma, which ionizes and strikes the target material.
- Power and Pressure: The RF power and chamber pressure are carefully controlled to optimize film quality and deposition rate.
- Substrate Temperature: Low-temperature deposition is achieved by controlling the RF power and gas flow, making it suitable for temperature-sensitive substrates.
-
Challenges and Considerations:
- Complex Equipment: RF sputtering requires specialized equipment, including RF generators and impedance matching networks, which can increase costs.
- Process Optimization: Achieving the desired film properties (e.g., thickness, uniformity, refractive index) requires careful tuning of process parameters.
- Material Compatibility: While RF sputtering is ideal for oxides and insulators, it may not be as efficient for highly conductive materials compared to DC sputtering.
-
Future Trends and Innovations:
- Advanced Materials: RF sputtering is being explored for depositing novel materials, such as complex oxides and 2D materials, for next-generation electronic and photonic devices.
- Hybrid Techniques: Combining RF sputtering with other deposition methods (e.g., pulsed laser deposition) to enhance film quality and functionality.
- Scalability: Efforts are underway to scale up RF sputtering for large-area deposition, making it more viable for industrial applications.
By understanding these key points, equipment and consumable purchasers can better evaluate the suitability of RF sputtering for their specific applications and make informed decisions about the necessary equipment and materials.
Summary Table:
Key Aspect | Details |
---|---|
Definition | RF sputtering uses radio frequency energy to deposit insulating oxide films. |
Advantages | Prevents charge buildup, produces uniform films, low substrate temperature. |
Applications | Optical waveguides, photonic microcavities, 1-D photonic crystals. |
Process Parameters | Frequency: 13.56 MHz, inert gas (argon), controlled power and pressure. |
Comparison with DC Sputtering | Suitable for insulators, avoids arcing, stable deposition process. |
Discover how RF sputtering can enhance your thin-film applications—contact our experts today!