Rapid Thermal Annealing (RTA) is a specialized heat treatment process used primarily in semiconductor manufacturing to enhance the properties of materials, particularly silicon films. It involves rapidly heating the material to high temperatures using intense light sources, holding it at that temperature for a short duration, and then cooling it quickly. This process improves material uniformity, reduces defects, and lowers production costs compared to traditional annealing methods. RTA is particularly effective in altering a material's physical and chemical properties by relieving internal stresses and promoting recrystallization.
Key Points Explained:
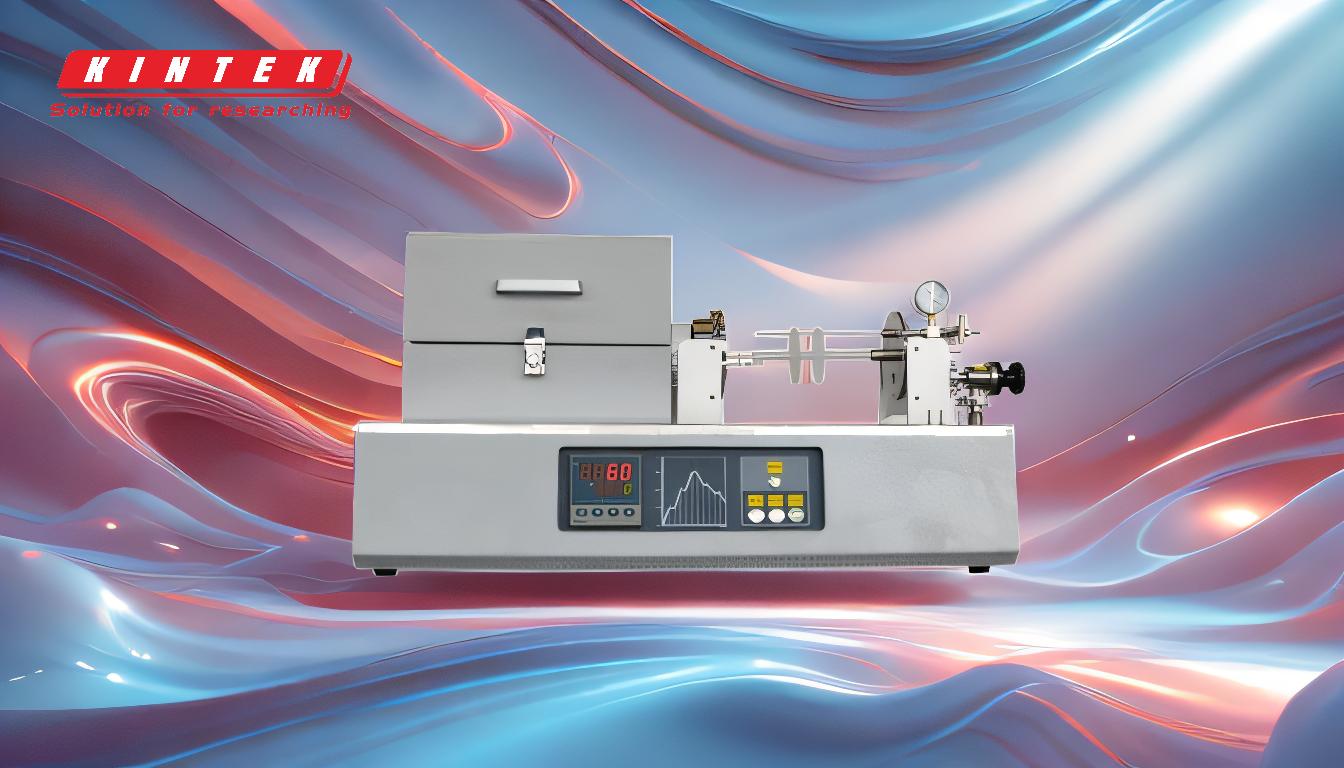
-
Definition and Purpose of RTA:
- RTA Overview: Rapid Thermal Annealing (RTA) is a heat treatment process that uses intense light sources to quickly heat materials, such as silicon films, to high temperatures.
- Purpose: The primary goal of RTA is to improve material properties, such as uniformity and crystallinity, while reducing internal stresses and defects. This is achieved by heating the material above its recrystallization temperature, holding it at that temperature, and then cooling it rapidly.
-
How RTA Works:
- Heating Mechanism: RTA employs high-intensity light sources, such as halogen lamps or lasers, to rapidly heat the material. This allows for precise control over the temperature and heating duration.
- Temperature Control: The material is heated to a temperature above its recrystallization point, typically in the range of 600°C to 1200°C, depending on the material and desired outcome.
- Cooling Process: After the material is held at the desired temperature for a short period (usually a few seconds to minutes), it is rapidly cooled. This rapid cooling helps to lock in the improved material properties.
-
Benefits of RTA:
- Improved Material Uniformity: RTA ensures that the material is heated uniformly, leading to consistent properties across the entire sample.
- Reduced Defects: The rapid heating and cooling process minimizes the formation of defects, such as dislocations and grain boundaries, which can degrade material performance.
- Lower Production Costs: RTA is more efficient than traditional annealing methods, reducing the time and energy required for the process, which in turn lowers production costs.
-
Applications of RTA:
- Semiconductor Manufacturing: RTA is widely used in the semiconductor industry to improve the quality of silicon wafers and thin films. It is essential for processes such as doping, oxidation, and crystallization.
- Material Science: Beyond semiconductors, RTA is used in material science to enhance the properties of various materials, including metals, ceramics, and polymers.
-
Comparison with Traditional Annealing:
- Speed: RTA is significantly faster than traditional annealing methods, which can take hours or even days. RTA completes the process in seconds to minutes.
- Precision: RTA offers better control over the heating and cooling rates, allowing for more precise manipulation of material properties.
- Energy Efficiency: The rapid nature of RTA means that less energy is consumed compared to traditional annealing, making it a more environmentally friendly option.
-
Challenges and Considerations:
- Thermal Stress: Rapid heating and cooling can introduce thermal stress, which may lead to cracking or warping in some materials. Careful control of the process parameters is necessary to mitigate these risks.
- Equipment Costs: The specialized equipment required for RTA, such as high-intensity light sources and precise temperature control systems, can be expensive. However, the long-term savings in production costs often justify the initial investment.
In summary, Rapid Thermal Annealing (RTA) is a highly efficient and effective heat treatment process used to improve the properties of materials, particularly in semiconductor manufacturing. Its ability to rapidly heat and cool materials leads to improved uniformity, reduced defects, and lower production costs. While there are challenges associated with the process, the benefits often outweigh the drawbacks, making RTA a valuable tool in modern material science and manufacturing.
Summary Table:
Aspect | Details |
---|---|
Definition | A heat treatment process using intense light for rapid heating and cooling. |
Purpose | Improves material uniformity, reduces defects, and lowers production costs. |
Temperature Range | 600°C to 1200°C, depending on material and desired outcomes. |
Key Benefits | Uniform heating, reduced defects, energy efficiency, and cost savings. |
Applications | Semiconductor manufacturing, material science (metals, ceramics, polymers). |
Challenges | Thermal stress, high equipment costs. |
Ready to enhance your material processing with RTA? Contact our experts today to learn more!