Sputter damage refers to the unintended harm caused to a substrate during the sputtering process, which is a technique used to deposit thin films of material onto a surface. This damage typically occurs when highly energetic particles, such as ions, bombard the substrate during the deposition process. These energetic particles can disrupt the atomic structure of the substrate, leading to surface defects, reduced performance, or even failure of the device being fabricated. Sputter damage is particularly problematic in the fabrication of optoelectronic devices, such as solar panels or displays, where maintaining the integrity of the substrate is crucial for optimal performance.
Key Points Explained:
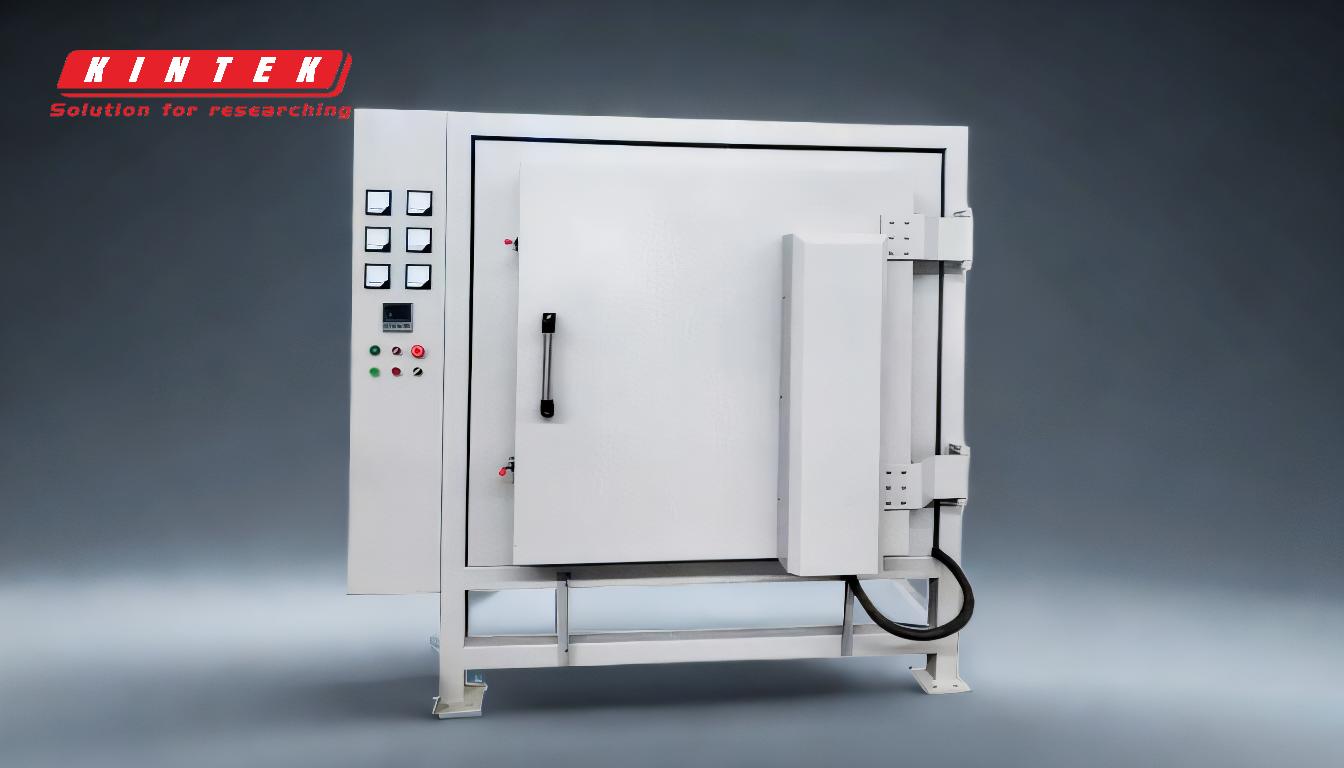
-
What is Sputtering?
- Sputtering is a physical vapor deposition (PVD) technique used to deposit thin films of material onto a substrate.
- It involves bombarding a target material with high-energy ions, usually from a noble gas like argon, in a vacuum chamber.
- The energy from the ions causes atoms from the target material to be ejected and deposited onto a nearby substrate.
-
Mechanism of Sputter Damage:
- During the sputtering process, highly energetic ions collide with the substrate surface.
- These collisions can transfer enough energy to the substrate atoms to overcome their binding energy, causing them to be displaced or ejected.
- This bombardment can lead to surface defects, such as pits, cracks, or changes in the crystalline structure of the substrate material.
-
Causes of Sputter Damage:
- High Energy Ions: The primary cause of sputter damage is the high kinetic energy of the ions used in the sputtering process. If the energy of these ions is too high, it can cause significant damage to the substrate.
- Ion Flux: The rate at which ions bombard the substrate (ion flux) can also contribute to damage. A high ion flux increases the likelihood of collisions and subsequent damage.
- Substrate Sensitivity: Some materials are more susceptible to damage than others. For example, delicate materials used in optoelectronic devices, such as organic semiconductors or thin-film transistors, are particularly vulnerable to sputter damage.
-
Effects of Sputter Damage:
- Surface Roughness: Sputter damage can increase the surface roughness of the substrate, which can negatively affect the performance of the deposited film.
- Electrical Properties: In electronic devices, sputter damage can alter the electrical properties of the substrate, leading to increased resistance or reduced conductivity.
- Optical Properties: For optoelectronic devices, such as solar panels or displays, sputter damage can reduce the transparency or alter the refractive index of the substrate, affecting light absorption or emission.
-
Mitigation Strategies:
- Optimizing Ion Energy: Reducing the energy of the ions used in the sputtering process can minimize damage. This can be achieved by adjusting the voltage or using lower-energy ions.
- Protective Layers: Applying a protective layer to the substrate before sputtering can help shield it from damage. This layer can be removed or left in place, depending on the application.
- Substrate Cooling: Cooling the substrate during the sputtering process can reduce the thermal energy transferred during ion bombardment, thereby minimizing damage.
- Alternative Deposition Techniques: In some cases, alternative deposition techniques, such as chemical vapor deposition (CVD) or atomic layer deposition (ALD), may be used to avoid sputter damage altogether.
-
Applications and Relevance:
- Sputter damage is particularly relevant in the fabrication of optoelectronic devices, such as solar cells, LEDs, and displays, where the integrity of the substrate is critical for device performance.
- It is also a concern in the deposition of transparent conductive oxides (TCOs), which are used in touchscreens, solar panels, and other applications requiring both transparency and conductivity.
In summary, sputter damage is an unintended consequence of the sputtering process, where highly energetic ions bombard the substrate, causing surface defects and potentially compromising the performance of the device. Understanding the causes and effects of sputter damage, as well as implementing mitigation strategies, is crucial for the successful fabrication of high-performance optoelectronic devices.
Summary Table:
Aspect | Details |
---|---|
What is Sputtering? | A PVD technique using high-energy ions to deposit thin films on substrates. |
Mechanism | Energetic ions collide with the substrate, causing atomic displacement. |
Causes | High ion energy, high ion flux, and substrate sensitivity. |
Effects | Surface roughness, altered electrical/optical properties. |
Mitigation | Optimize ion energy, use protective layers, cool substrates, or use CVD/ALD. |
Need help minimizing sputter damage in your fabrication process? Contact our experts today!