Sputtering is a physical vapor deposition (PVD) technique used to deposit thin films of materials onto substrates. It involves bombarding a target material with high-energy ions, typically from an inert gas like argon, in a vacuum environment. The ions transfer energy to the target atoms, causing them to be ejected from the surface. These ejected atoms then travel through the vacuum and condense on the substrate, forming a thin film. Sputtering is widely used in industries such as semiconductors, optics, and coatings due to its ability to deposit high-quality, uniform films of a wide range of materials, including metals, alloys, and insulators.
Key Points Explained:
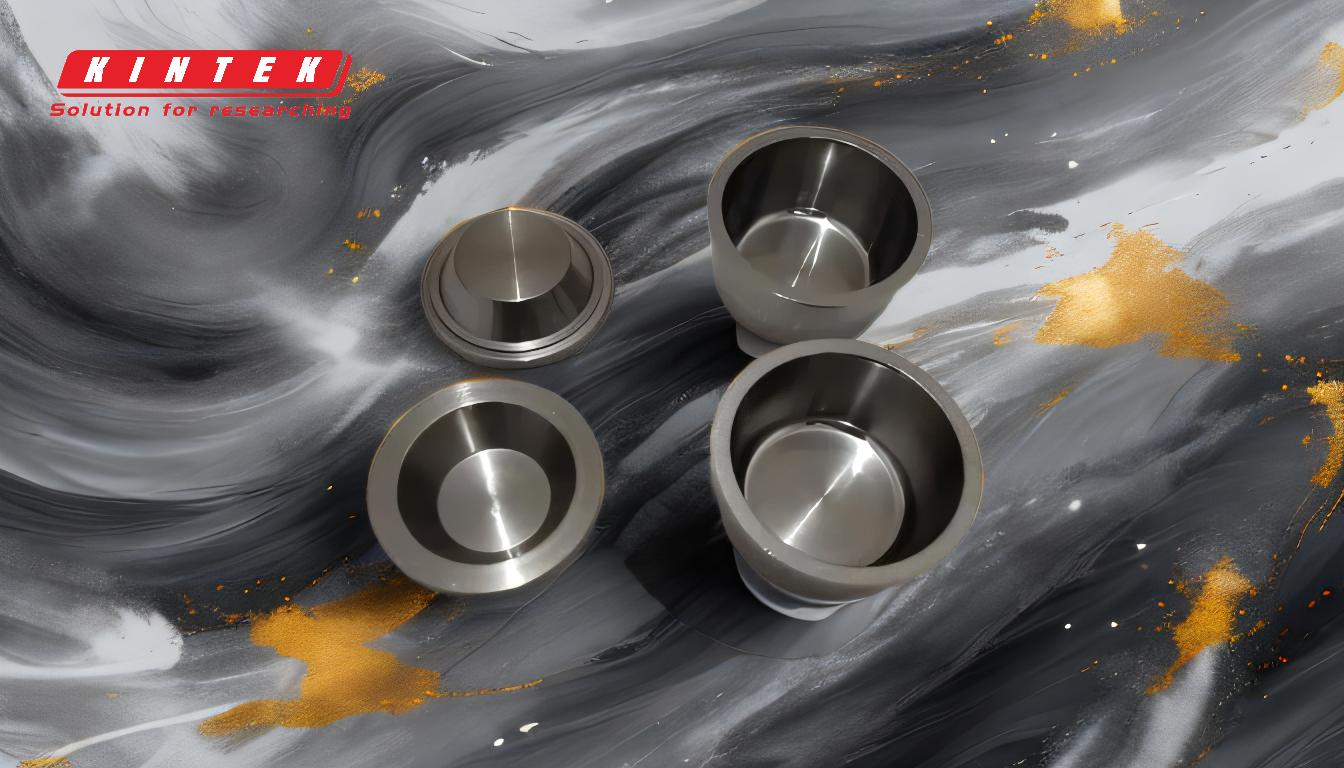
-
Definition of Sputtering:
- Sputtering is a physical process where atoms are ejected from a solid target material due to bombardment by high-energy ions.
- It is a key technique in thin film deposition, commonly used in manufacturing and research.
-
Mechanism of Sputtering:
- Ion Bombardment: High-energy ions (usually from an inert gas like argon) are accelerated towards the target material.
- Energy Transfer: The ions collide with the target atoms, transferring energy and dislodging them from the surface.
- Ejection of Atoms: The target atoms are ejected as neutral particles, forming a vapor cloud.
- Deposition: The ejected atoms travel through the vacuum and condense onto the substrate, forming a thin film.
-
Vacuum Environment:
- Sputtering requires a vacuum to minimize collisions between the ejected atoms and gas molecules, ensuring a clean and uniform deposition.
- The vacuum also prevents contamination and allows precise control over the deposition process.
-
Types of Sputtering:
- DC Sputtering: Used for conductive materials. A direct current (DC) power source generates the plasma.
- RF Sputtering: Used for insulating materials. A radio frequency (RF) power source is required to create the plasma.
- Magnetron Sputtering: Uses magnetic fields to enhance the efficiency of the sputtering process, allowing for higher deposition rates and better film quality.
-
Materials Suitable for Sputtering:
- Metals and Alloys: Commonly used for their conductivity and durability.
- Insulators: Can be deposited using RF sputtering.
- High Melting Point Materials: Sputtering is effective for materials like carbon and silicon, which are difficult to deposit using other methods.
-
Advantages of Sputtering:
- Uniform Films: Produces highly uniform and dense films with excellent adhesion to the substrate.
- Versatility: Can deposit a wide range of materials, including metals, alloys, and insulators.
- High-Quality Films: Results in films with minimal defects and high purity.
- Scalability: Suitable for both small-scale research and large-scale industrial production.
-
Applications of Sputtering:
- Semiconductors: Used to deposit thin films in the fabrication of integrated circuits and microelectronics.
- Optics: Used to create anti-reflective coatings, mirrors, and other optical components.
- Coatings: Applied to improve the durability, corrosion resistance, and aesthetic properties of various materials.
- Solar Cells: Used to deposit thin films in the production of photovoltaic cells.
-
Challenges and Considerations:
- Target Material: The choice of target material affects the quality and properties of the deposited film.
- Substrate Preparation: The substrate must be clean and properly prepared to ensure good adhesion of the film.
- Process Control: Precise control of parameters such as pressure, temperature, and ion energy is crucial for achieving the desired film properties.
In summary, sputtering is a versatile and widely used technique for depositing thin films of various materials. Its ability to produce high-quality, uniform films makes it essential in many high-tech industries, from semiconductors to optics. Understanding the principles and applications of sputtering can help in selecting the right materials and processes for specific deposition needs.
Summary Table:
Aspect | Details |
---|---|
Definition | Physical process where atoms are ejected from a target material by ion bombardment. |
Mechanism | Ion bombardment → Energy transfer → Ejection of atoms → Deposition on substrate. |
Vacuum Environment | Ensures clean, uniform deposition and prevents contamination. |
Types | DC Sputtering, RF Sputtering, Magnetron Sputtering. |
Materials | Metals, alloys, insulators, high melting point materials. |
Advantages | Uniform films, versatility, high-quality results, scalability. |
Applications | Semiconductors, optics, coatings, solar cells. |
Challenges | Target material selection, substrate preparation, precise process control. |
Discover how sputtering can enhance your thin film processes—contact our experts today!