The sputtering rate is a critical parameter in thin film deposition processes, representing the rate at which target material is ejected and deposited onto a substrate. It is influenced by factors such as the sputter yield (number of atoms ejected per incident ion), the properties of the target material (molar weight, density), and the ion current density. The sputtering rate can be calculated using a specific formula that incorporates these variables. Understanding and controlling the sputtering rate is essential for achieving uniform and high-quality thin films in applications such as semiconductor manufacturing, optical coatings, and surface engineering.
Key Points Explained:
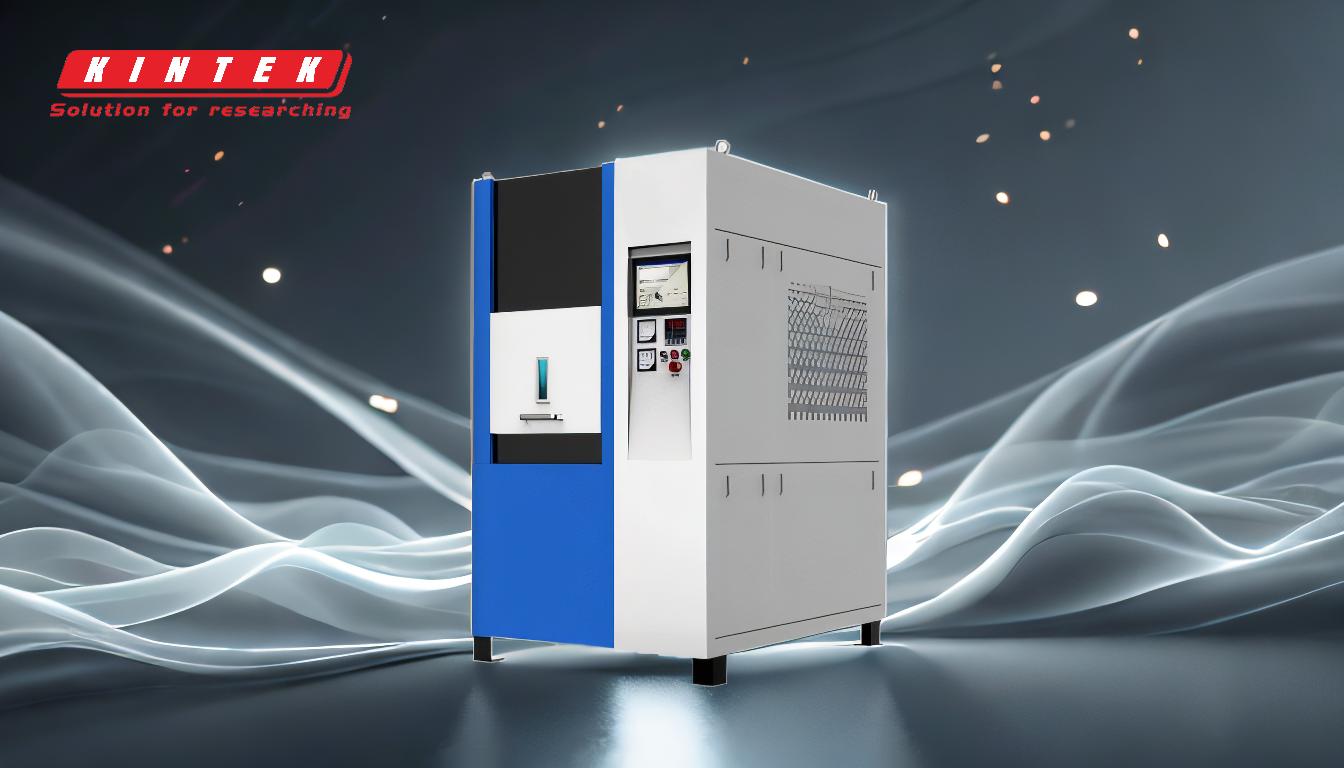
-
Definition of Sputtering Rate:
- The sputtering rate is defined as the number of monolayers per second that are sputtered from a target's surface. It quantifies how quickly material is removed from the target and deposited onto the substrate.
- It is a crucial parameter in thin film deposition processes, as it directly impacts the thickness and uniformity of the deposited film.
-
Factors Influencing Sputtering Rate:
- Sputter Yield (S): The number of target atoms ejected per incident ion. This depends on factors such as the energy of the incident ions, the masses of the ions and target atoms, the angle of incidence, and the binding energy of atoms in the target material.
- Molar Weight of the Target (M): Heavier target atoms generally result in a lower sputtering rate, as more energy is required to eject them from the target.
- Material Density (p): Denser materials may require higher energy to achieve the same sputtering rate as less dense materials.
- Ion Current Density (j): Higher ion current density increases the number of ions bombarding the target, leading to a higher sputtering rate.
-
Mathematical Representation:
- The sputtering rate can be calculated using the formula:
[
\text{Sputtering rate} = \frac{MSj}{pN_A e}
]
where:
- ( M ) = molar weight of the target material,
- ( S ) = sputter yield,
- ( j ) = ion current density,
- ( p ) = density of the target material,
- ( N_A ) = Avogadro's number,
- ( e ) = electron charge.
- This equation provides a quantitative way to predict and control the sputtering rate for specific materials and conditions.
- The sputtering rate can be calculated using the formula:
[
\text{Sputtering rate} = \frac{MSj}{pN_A e}
]
where:
-
Practical Implications:
- Uniform Deposition: A consistent sputtering rate is essential for achieving uniform thin films. Variations in the sputtering rate can lead to uneven film thickness and defects.
- Material Compatibility: Different materials have different sputtering rates due to variations in their physical properties (e.g., density, binding energy). Understanding these differences is crucial for selecting the right target material for a specific application.
- Process Optimization: By controlling factors such as ion energy, ion current density, and chamber pressure, manufacturers can optimize the sputtering rate to achieve desired film properties.
-
Role of Equipment and Process Parameters:
- Power Source (DC or RF): The type of power source used in sputtering affects the deposition rate and material compatibility. DC sputtering is typically used for conductive materials, while RF sputtering is suitable for insulating materials.
- Chamber Pressure: Adjusting the chamber pressure can improve the coverage and uniformity of the deposited film by controlling the kinetic energy and direction of the sputtered particles.
- Kinetic Energy of Emitted Particles: Higher kinetic energy can increase surface mobility, leading to better film quality and adhesion.
-
Applications and Importance:
- The sputtering rate is a key consideration in industries such as semiconductor manufacturing, where precise control over film thickness and uniformity is critical.
- It is also important in optical coatings, where the quality of the deposited film directly impacts the performance of the coating (e.g., reflectivity, durability).
- In surface engineering, controlling the sputtering rate allows for the creation of tailored surface properties, such as hardness, wear resistance, and corrosion resistance.
By understanding and controlling the sputtering rate, manufacturers can ensure the production of high-quality thin films with the desired properties for a wide range of applications.
Summary Table:
Key Aspect | Description |
---|---|
Definition | Rate at which target material is ejected and deposited onto a substrate. |
Key Factors | Sputter yield, molar weight, material density, ion current density. |
Formula | Sputtering rate = (M × S × j) / (p × N_A × e) |
Applications | Semiconductor manufacturing, optical coatings, surface engineering. |
Importance | Ensures uniform film thickness, material compatibility, and process optimization. |
Optimize your thin film deposition process—contact our experts today for tailored solutions!