Sputtering is a versatile and widely used thin-film deposition technique with numerous advantages. It allows for the deposition of a wide range of materials, including those with high melting points and low vapor pressure, and produces films with excellent adhesion, uniformity, and purity. The process is highly controllable, enabling precise tuning of film properties and thickness. Additionally, sputtering is suitable for various substrates, operates at reduced temperatures, and can achieve high deposition rates without compromising film quality. It is also maintenance-free and compatible with ultrahigh vacuum applications, making it ideal for advanced industrial and research applications.
Key Points Explained:
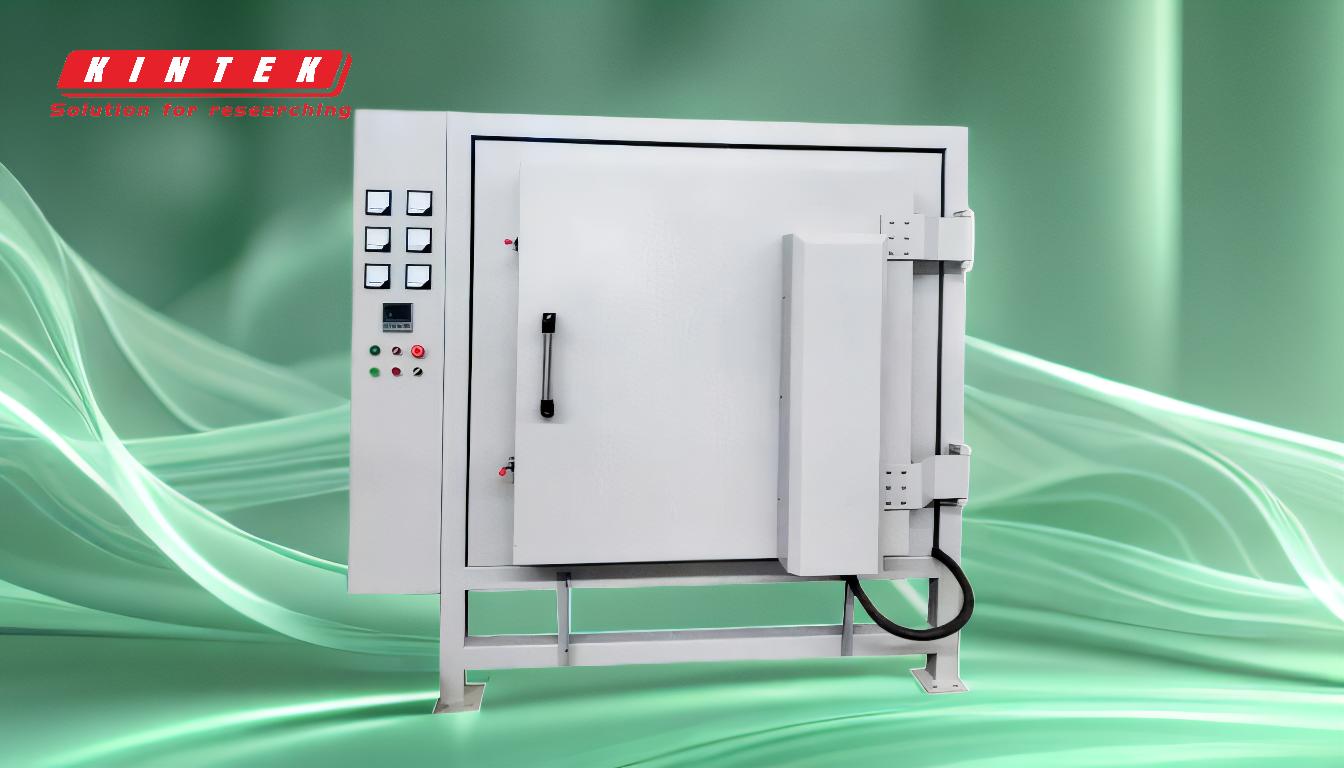
-
Versatility in Material Deposition:
- Sputtering can deposit virtually any material, including metals, semiconductors, insulators, compounds, and mixtures. This makes it suitable for a wide range of applications, from electronics to optics.
- It is particularly advantageous for materials with high melting points and low vapor pressure, which are difficult to deposit using other methods like evaporation.
- Example: Materials like tungsten and ceramics, which have high melting points, can be easily sputtered.
-
Excellent Film Adhesion:
- Sputtered atoms have high kinetic energy, which enhances their adhesion to the substrate. This results in stronger bonds and the formation of a diffusion layer at the interface.
- Better adhesion is critical for applications where mechanical durability and long-term stability are required.
- Example: Sputtered films are less likely to peel or delaminate compared to evaporated films.
-
High Film Purity and Density:
- The sputtering process avoids contamination from evaporation sources, leading to films with high purity and density.
- Fewer pinholes and defects are observed in sputtered films, making them ideal for applications requiring high-quality coatings.
- Example: Sputtered films are often used in semiconductor manufacturing due to their high purity.
-
Precise Control Over Film Thickness and Uniformity:
- Film thickness can be precisely controlled by adjusting the target current, ensuring reproducibility and uniformity across large areas.
- This level of control is essential for applications like optical coatings and microelectronics.
- Example: Sputtering is used to create uniform anti-reflective coatings on lenses and displays.
-
Ability to Deposit Complex Materials:
- Sputtering can deposit elements, alloys, and compounds, including reactive materials, by incorporating reactive gases into the process.
- This allows for the creation of tailored films with specific properties, such as hardness, conductivity, or optical characteristics.
- Example: Reactive sputtering is used to deposit titanium nitride (TiN) for wear-resistant coatings.
-
Low-Temperature Deposition:
- Sputtering can be performed at reduced temperatures, making it suitable for temperature-sensitive substrates like plastics and organics.
- This expands its applicability to industries like flexible electronics and biomedical devices.
- Example: Sputtering is used to deposit thin films on polymer substrates for flexible displays.
-
Molecular-Level Precision:
- The process enables precise control at the molecular level, allowing for the creation of pristine interfaces and the tuning of film properties.
- This is crucial for advanced applications in nanotechnology and materials science.
- Example: Sputtering is used to fabricate multilayer structures in quantum devices.
-
High Deposition Rates and Scalability:
- Sputtering offers high deposition rates without thickness limitations, making it suitable for industrial-scale production.
- The process can be scaled up to coat large areas uniformly, which is beneficial for applications like solar panels and architectural glass.
- Example: Sputtering is used to deposit transparent conductive oxides (TCOs) on large glass panels.
-
Maintenance-Free and Vacuum-Compatible:
- Sputtering systems are maintenance-free and compatible with ultrahigh vacuum environments, ensuring clean and reliable operation.
- This is particularly important for applications in aerospace, semiconductors, and research laboratories.
- Example: Sputtering is used in the fabrication of thin-film solar cells in vacuum environments.
-
Improved Surface Morphology:
- Sputtering produces films with superior morphological quality, including reduced roughness and controlled grain size.
- This is advantageous for applications where surface smoothness and stoichiometry are critical.
- Example: Sputtering is used to create smooth, high-quality coatings for optical components.
-
Reduced Residual Stresses:
- The low or medium temperature deposition process minimizes residual stresses on the substrate, preserving its structural integrity.
- This is beneficial for delicate substrates or applications requiring mechanical stability.
- Example: Sputtering is used to deposit thin films on silicon wafers without inducing stress-related defects.
-
In-Situ Cleaning and Deposition:
- Sputtering systems can clean substrates and deposit coatings in the same vacuum chamber, improving efficiency and film quality.
- This reduces contamination and ensures better adhesion.
- Example: In-situ cleaning is used in the production of magnetic storage media to enhance performance.
In summary, sputtering offers a unique combination of versatility, precision, and quality, making it a preferred choice for a wide range of industrial and research applications. Its ability to deposit complex materials, control film properties, and operate under various conditions ensures its continued relevance in advanced manufacturing and technology development.
Summary Table:
Advantage | Key Benefit |
---|---|
Versatility in Material Deposition | Deposits metals, semiconductors, insulators, and compounds with high melting points. |
Excellent Film Adhesion | Strong bonds and diffusion layers ensure durability and stability. |
High Film Purity and Density | Contamination-free films with fewer defects, ideal for semiconductor manufacturing. |
Precise Control Over Thickness | Adjustable target current ensures uniform, reproducible film thickness. |
Low-Temperature Deposition | Suitable for temperature-sensitive substrates like plastics and organics. |
High Deposition Rates | Scalable for industrial production with no thickness limitations. |
Maintenance-Free Operation | Compatible with ultrahigh vacuum environments for clean, reliable performance. |
Interested in leveraging sputtering for your next project? Contact our experts today to learn more!