Blown film extrusion is a widely used manufacturing process for producing continuous plastic films, primarily utilized in packaging applications. The process involves melting plastic in an extruder, shaping the molten polymer into a tube through an annular die head, and then inflating it into a bubble using air pressure. This bubble is then cooled, flattened, and wound into rolls. The method is highly versatile, allowing for the production of films with varying thicknesses, widths, and properties. It is particularly valued for its efficiency, scalability, and ability to produce high-quality films suitable for a wide range of applications.
Key Points Explained:
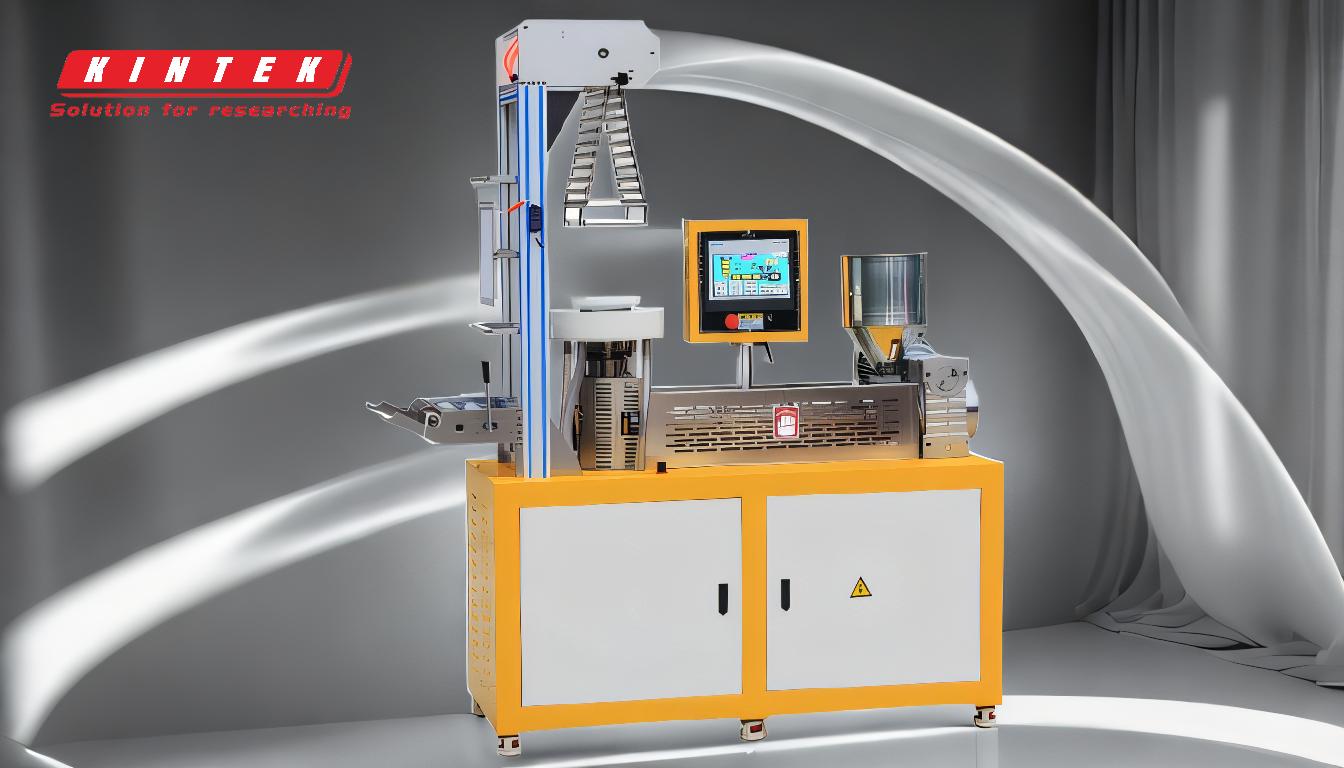
-
Overview of Blown Film Extrusion:
- Blown film extrusion is a continuous process used to manufacture plastic films.
- It is predominantly employed in the packaging industry due to its ability to produce thin, flexible, and durable films.
-
The Extrusion Process:
- Melting the Plastic: The process begins with the plastic resin being fed into an extruder, where it is heated and melted.
- Forming the Tube: The molten polymer is then forced through an annular die, which shapes it into a tubular form.
-
Formation of the Bubble:
- Inflation: Air is introduced into the center of the tubular film, causing it to inflate into a bubble.
- Controlled Expansion: The size of the bubble is controlled by adjusting the air pressure, which determines the film's thickness and width.
-
Cooling and Solidification:
- Cooling Process: The inflated bubble is cooled using air rings or other cooling circulator systems to solidify the film.
- Stabilization: The cooling process ensures that the film maintains its shape and properties as it is pulled upwards.
-
Flattening and Winding:
- Flattening the Bubble: Once cooled, the bubble is collapsed into a flat film using nip rolls.
- Winding: The flattened film is then wound onto rolls for storage, transportation, or further processing.
-
Advantages of Blown Film Extrusion:
- Versatility: The process can produce films with a wide range of thicknesses, widths, and properties.
- Efficiency: It is a continuous process, allowing for high production rates and minimal downtime.
- Scalability: The method can be scaled to produce films for both small and large-scale applications.
-
Applications of Blown Film Extrusion:
- Packaging: The primary application is in the production of packaging materials, including bags, wraps, and liners.
- Industrial Films: It is also used to produce films for industrial applications, such as agricultural films, construction films, and more.
-
Material Considerations:
- Polymer Selection: The choice of polymer (e.g., polyethylene, polypropylene) affects the film's properties, such as strength, flexibility, and barrier properties.
- Additives: Various additives can be incorporated to enhance the film's performance, such as UV stabilizers, anti-fog agents, and colorants.
-
Quality Control:
- Thickness Uniformity: Ensuring consistent film thickness is critical for performance and application suitability.
- Surface Quality: The film must be free from defects such as bubbles, gels, or streaks, which can affect its appearance and functionality.
-
Environmental Considerations:
- Recyclability: Many films produced by blown film extrusion are recyclable, contributing to sustainability efforts.
- Energy Efficiency: Advances in technology have led to more energy-efficient extrusion processes, reducing the environmental impact.
In summary, blown film extrusion is a highly efficient and versatile method for producing plastic films, particularly for packaging. The process involves melting plastic, forming it into a tube, inflating it into a bubble, cooling, and then flattening and winding it into rolls. The method offers numerous advantages, including versatility, efficiency, and scalability, making it a preferred choice for a wide range of applications.
Summary Table:
Key Aspect | Details |
---|---|
Process Overview | Continuous production of plastic films via extrusion and inflation. |
Main Applications | Packaging (bags, wraps) and industrial films (agricultural, construction). |
Advantages | Versatility, efficiency, scalability, and high-quality film production. |
Material Considerations | Polymers (e.g., polyethylene) and additives (e.g., UV stabilizers). |
Environmental Impact | Recyclable films and energy-efficient processes. |
Discover how blown film extrusion can enhance your production—contact us today!