The blown film extrusion technique is a widely used manufacturing process in the plastics industry for producing thin, flexible plastic films. It involves melting plastic pellets and extruding them through a circular die. As the molten plastic emerges, air is blown into the center of the die, inflating the plastic into a bubble or tube. This bubble is then cooled, collapsed, and wound into rolls for further processing or use. The technique is versatile, allowing for the production of films with varying thicknesses, widths, and properties, making it suitable for applications such as packaging, agricultural films, and industrial liners.
Key Points Explained:
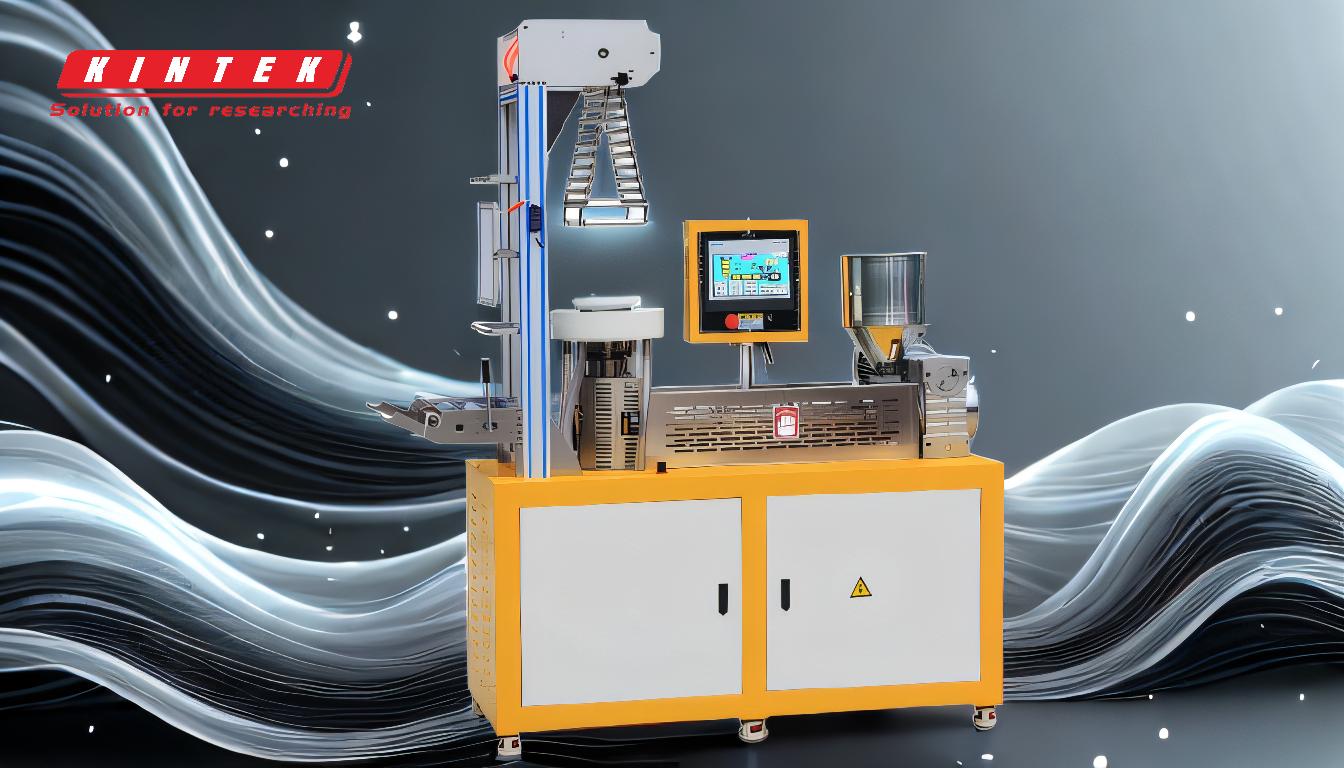
-
Process Overview:
- Melting Plastic Pellets: The process begins with plastic pellets being fed into an extruder, where they are heated and melted.
- Circular Die Extrusion: The molten plastic is forced through a circular die, forming a continuous tube of plastic.
- Air Inflation: Compressed air is introduced into the center of the die, inflating the plastic tube into a bubble. This step determines the film's thickness and width.
- Cooling and Collapsing: The bubble is cooled using air rings or other cooling systems, solidifying the plastic. It is then collapsed into a flat film.
- Winding: The flattened film is wound onto rolls for storage or further processing.
-
Key Components of the Process:
- Extruder: The machine that melts and pushes the plastic through the die.
- Circular Die: Shapes the molten plastic into a tube.
- Air Ring: Provides cooling and stabilizes the bubble.
- Nip Rolls: Flatten the bubble into a double-layered film.
- Wind-Up System: Collects the finished film into rolls.
-
Advantages of Blown Film Extrusion:
- Versatility: Can produce films of various thicknesses, widths, and properties.
- Cost-Effectiveness: High production rates and minimal material waste.
- Customizability: Allows for the addition of additives, colors, or multiple layers (co-extrusion) to achieve specific film properties.
- Uniformity: Produces films with consistent thickness and strength.
-
Applications of Blown Film Extrusion:
- Packaging: Used for food packaging, shrink wrap, and bags.
- Agriculture: Produces greenhouse films, mulch films, and silage bags.
- Industrial: Creates liners, protective films, and construction materials.
- Medical: Used for sterile packaging and barrier films.
-
Factors Influencing Film Quality:
- Material Selection: The type of plastic (e.g., LDPE, HDPE, LLDPE) affects flexibility, strength, and clarity.
- Processing Parameters: Temperature, extrusion speed, and air pressure must be carefully controlled.
- Cooling Efficiency: Proper cooling ensures uniform thickness and prevents defects.
- Die Design: The shape and size of the die influence the film's dimensions and properties.
-
Challenges and Considerations:
- Thickness Control: Maintaining uniform thickness across the film can be challenging.
- Bubble Stability: Ensuring the bubble remains stable during inflation and cooling is critical.
- Material Limitations: Some plastics may not be suitable for blown film extrusion due to their melting or cooling characteristics.
By understanding these key points, purchasers of equipment and consumables can make informed decisions about the materials and machinery required for blown film extrusion, ensuring optimal production efficiency and film quality.
Summary Table:
Aspect | Details |
---|---|
Process Overview | Melting pellets, extruding through a die, inflating into a bubble, cooling, and winding. |
Key Components | Extruder, circular die, air ring, nip rolls, wind-up system. |
Advantages | Versatility, cost-effectiveness, customizability, uniformity. |
Applications | Packaging, agriculture, industrial, medical. |
Factors Affecting Quality | Material selection, processing parameters, cooling efficiency, die design. |
Challenges | Thickness control, bubble stability, material limitations. |
Ready to optimize your plastic film production? Contact our experts today for tailored solutions!