The blown film technique is a widely used method in plastic film manufacturing, particularly for producing thin, flexible films used in packaging, agriculture, and other industries. It involves extruding a molten polymer through a circular die, inflating it with pressurized air to form a bubble, cooling the bubble, and then slitting and winding it into rolls. This process allows for the production of seamless, tubular films with uniform thickness and excellent mechanical properties. The technique is versatile, enabling the creation of single-layer or multi-layer films tailored to specific applications.
Key Points Explained:
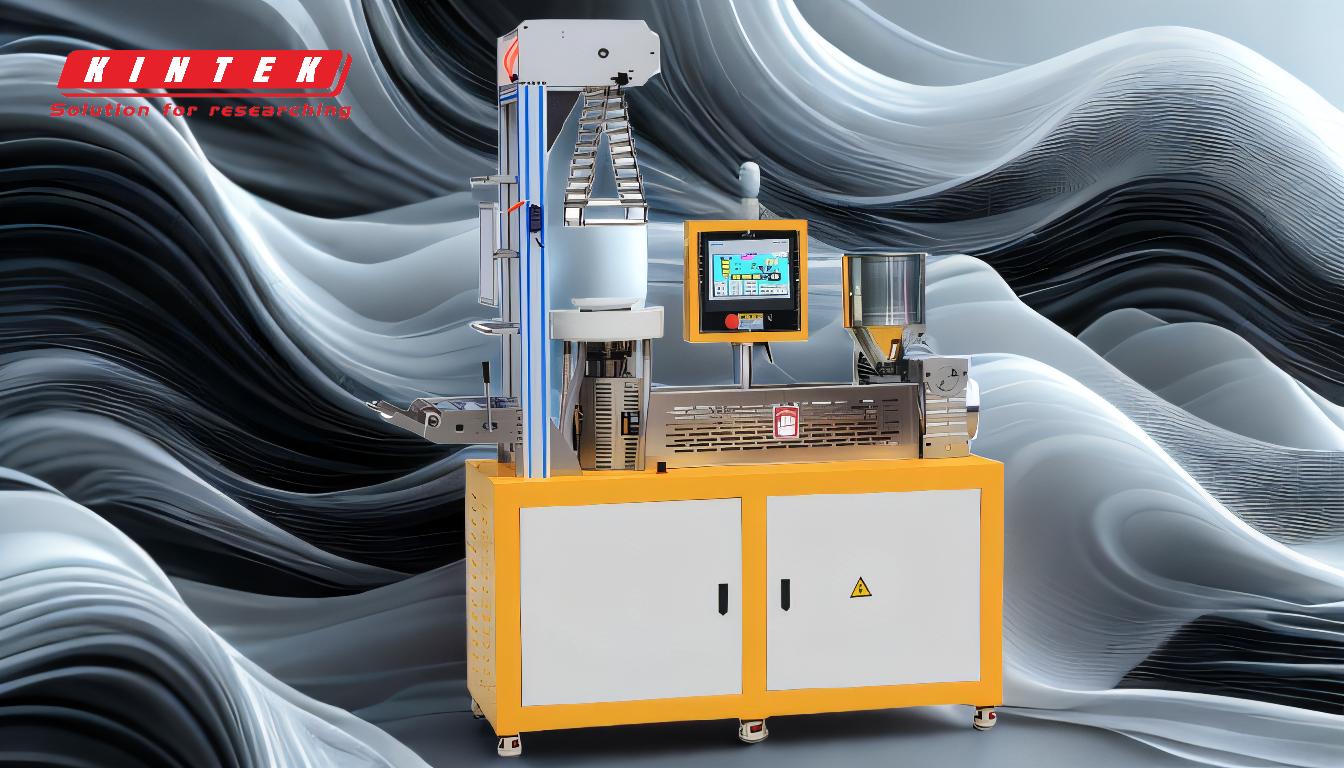
-
Extrusion and Melting
- The process begins with the extrusion of a polymer resin, which is melted and homogenized in an extruder. The molten polymer is then fed into a circular die head.
- The extruder ensures consistent melting and mixing, which is critical for achieving uniform film properties.
-
Formation of the Bubble
- The molten polymer exits the die as a tube and is inflated with pressurized air to form a bubble. The size of the bubble determines the film's width and thickness.
- The air pressure and extrusion rate are carefully controlled to achieve the desired dimensions and mechanical properties.
-
Cooling Process
- The bubble is cooled using air rings or other cooling systems to solidify the polymer into a stable film. Cooling is critical to prevent deformation and ensure consistent thickness.
- Rapid cooling can enhance the film's clarity and mechanical strength.
-
Slitting and Winding
- Once cooled, the bubble is collapsed and slit into flat sheets or left as a tube, depending on the application. The film is then wound onto rolls for further processing or distribution.
- Slitting must be precise to avoid defects and ensure uniformity.
-
Versatility and Applications
- The blown film technique can produce single-layer or multi-layer films by co-extruding different polymers. This allows for customization of properties such as barrier performance, strength, and flexibility.
- Applications include food packaging, agricultural films, shrink films, and industrial liners.
-
Advantages of Blown Film
- Produces seamless, tubular films with uniform thickness.
- Suitable for high-volume production with minimal waste.
- Enables the creation of multi-layer films with tailored properties.
-
Post-Treatment Options
- Depending on the application, the film may undergo additional treatments such as corona treatment (to improve printability) or surface coating (to enhance barrier properties).
The blown film technique is a cornerstone of modern plastic film production, offering flexibility, efficiency, and the ability to meet diverse application requirements. Its adaptability makes it a preferred choice for manufacturers seeking high-quality, customizable films.
Summary Table:
Key Steps | Details |
---|---|
Extrusion and Melting | Polymer resin is melted and homogenized in an extruder for uniform properties. |
Formation of the Bubble | Molten polymer is inflated with air to form a bubble, determining film dimensions. |
Cooling Process | Bubble is cooled using air rings to solidify the film and ensure uniformity. |
Slitting and Winding | Bubble is collapsed, slit, and wound into rolls for further processing. |
Applications | Used in food packaging, agricultural films, shrink films, and industrial liners. |
Advantages | Seamless films, high-volume production, and customizable multi-layer options. |
Ready to enhance your plastic film production? Contact our experts today to learn more about the blown film technique!