Glass Lined Reactors (GLR) and Stainless Steel Reactors (SSR) are both widely used in chemical and pharmaceutical industries, but they differ significantly in their construction, properties, and applications. GLRs are made of steel coated with a layer of glass, offering excellent resistance to corrosion and chemical attack, making them ideal for highly corrosive processes. However, they are brittle and prone to damage under mechanical stress. SSRs, on the other hand, are made entirely of stainless steel, providing high mechanical strength, durability, and resistance to physical damage. They are suitable for processes involving high pressure, temperature, and mechanical agitation but may not perform as well in highly corrosive environments. The choice between GLR and SSR depends on the specific process requirements, including chemical compatibility, temperature, pressure, and mechanical stress.
Key Points Explained:
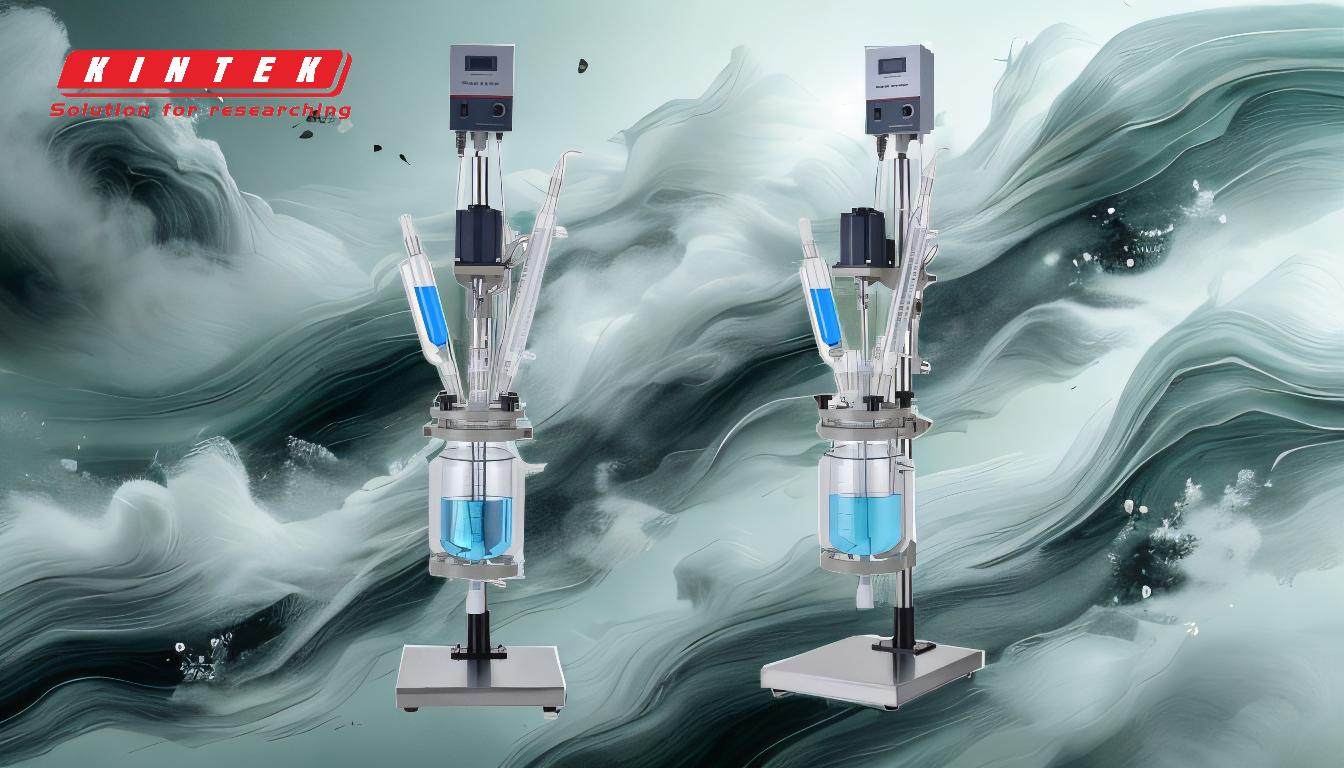
-
Material Composition:
- GLR: Constructed from steel with a glass lining, providing a chemically inert surface.
- SSR: Made entirely of stainless steel, offering robust mechanical properties.
-
Chemical Resistance:
- GLR: Exceptional resistance to a wide range of corrosive chemicals, acids, and bases.
- SSR: Good resistance to many chemicals but may not be suitable for highly corrosive substances.
-
Mechanical Strength:
- GLR: Brittle and susceptible to cracking or chipping under mechanical stress or impact.
- SSR: High mechanical strength, capable of withstanding high pressure, temperature, and mechanical agitation.
-
Temperature and Pressure Tolerance:
- GLR: Limited by the glass lining, typically used at lower temperatures and pressures.
- SSR: Can operate at higher temperatures and pressures, suitable for more demanding processes.
-
Maintenance and Durability:
- GLR: Requires careful handling and maintenance to prevent damage to the glass lining.
- SSR: More durable and easier to maintain, with less risk of damage from physical stress.
-
Applications:
- GLR: Ideal for processes involving highly corrosive chemicals, such as in the pharmaceutical and fine chemical industries.
- SSR: Suitable for a wide range of applications, including food processing, chemical manufacturing, and high-pressure reactions.
-
Cost Considerations:
- GLR: Generally more expensive due to the specialized manufacturing process and materials.
- SSR: More cost-effective for many applications, especially where high mechanical strength is required.
-
Customization and Flexibility:
- GLR: Limited customization options due to the fragility of the glass lining.
- SSR: Highly customizable, with various grades of stainless steel available to suit specific process requirements.
In summary, the choice between GLR and SSR depends on the specific needs of the process, including chemical compatibility, mechanical stress, temperature, and pressure requirements. GLRs are preferred for highly corrosive environments, while SSRs are better suited for processes requiring high mechanical strength and durability.
Summary Table:
Feature | Glass Lined Reactors (GLR) | Stainless Steel Reactors (SSR) |
---|---|---|
Material Composition | Steel with glass lining (chemically inert) | Entirely stainless steel (robust mechanical properties) |
Chemical Resistance | Exceptional resistance to corrosive chemicals | Good resistance, but less suitable for highly corrosive substances |
Mechanical Strength | Brittle, prone to damage under mechanical stress | High strength, withstands pressure and agitation |
Temperature Tolerance | Limited by glass lining (lower temperatures) | Operates at higher temperatures and pressures |
Maintenance | Requires careful handling to prevent glass damage | Durable, easier to maintain |
Applications | Ideal for highly corrosive processes | Suitable for high-pressure, high-temperature tasks |
Cost | More expensive due to specialized materials | Cost-effective for high-strength applications |
Customization | Limited due to glass fragility | Highly customizable with various steel grades |
Need help choosing the right reactor for your process? Contact our experts today!