Sputtering and plating are both techniques used to deposit thin films onto substrates, but they differ significantly in their mechanisms, processes, and applications. Sputtering is a type of physical vapor deposition (PVD) that involves bombarding a target material with energetic ions to eject atoms, which then deposit onto a substrate. In contrast, plating typically involves electrochemical processes where metal ions in a solution are reduced and deposited onto a substrate. Sputtering does not require melting the source material and operates at higher gas pressures, while plating relies on chemical reactions and often requires a liquid medium. Both methods are used in industries like electronics, optics, and coatings, but their choice depends on the specific requirements of the application.
Key Points Explained:
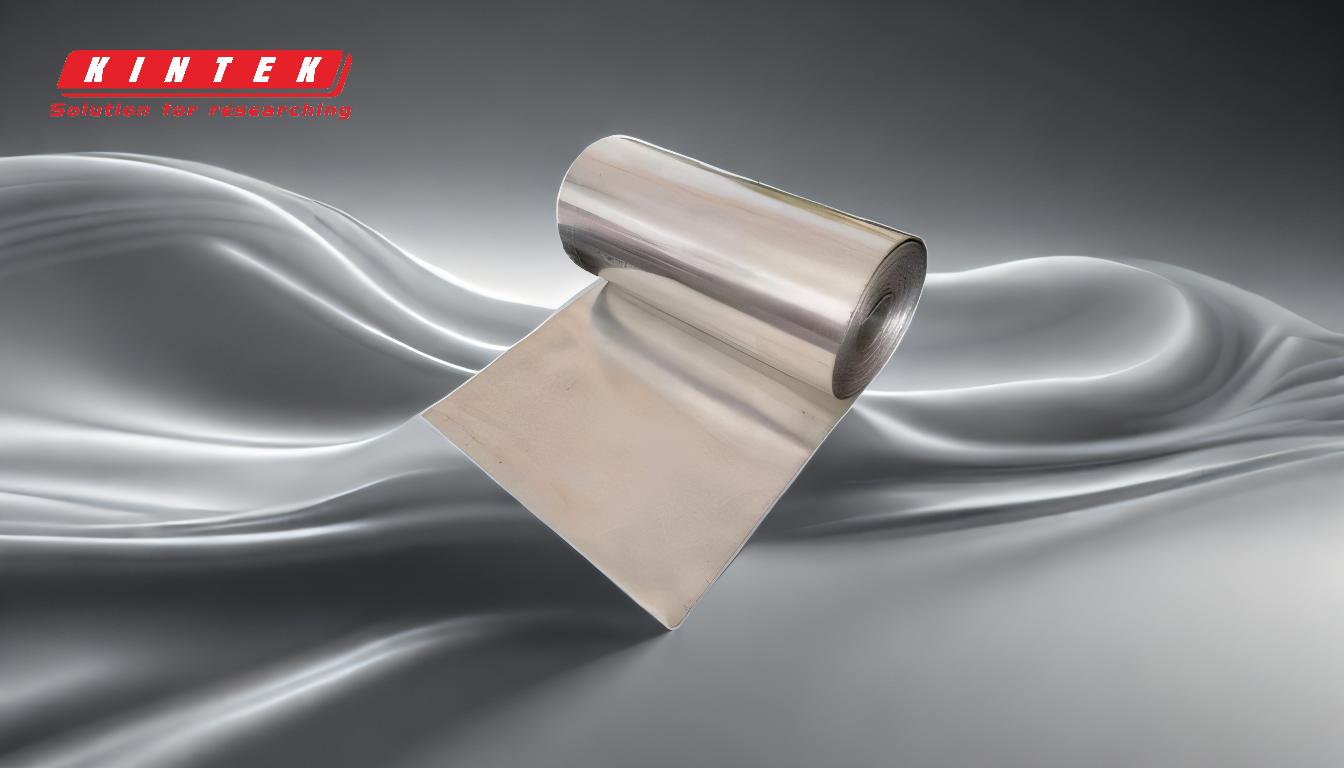
-
Mechanism of Deposition:
- Sputtering: Involves the use of energetic ions (typically from a plasma) to bombard a target material, causing atoms to be ejected from the target due to momentum transfer. These ejected atoms then travel and deposit onto a substrate to form a thin film. The process does not require the target material to melt.
- Plating: Typically relies on electrochemical processes. Metal ions in a solution are reduced at the substrate surface, forming a metallic coating. This process often involves an electric current to drive the reduction reaction.
-
Process Environment:
- Sputtering: Operates in a vacuum or low-pressure environment with inert gases (e.g., argon). The process can occur at higher gas pressures (5-15 mTorr), where sputtered particles may undergo gas-phase collisions before reaching the substrate.
- Plating: Usually takes place in a liquid medium (electrolyte solution). The substrate is immersed in the solution, and metal ions are deposited onto its surface through electrochemical reactions.
-
Energy Source:
- Sputtering: Uses electrical energy to generate a plasma, which produces the energetic ions needed to sputter the target material. The process is driven by physical bombardment rather than thermal energy.
- Plating: Relies on electrical energy to drive the reduction of metal ions in the solution. The energy is used to facilitate the chemical reactions that deposit the metal onto the substrate.
-
Deposition Rate and Control:
- Sputtering: Generally has a lower deposition rate compared to some other PVD methods like thermal evaporation. However, it offers excellent control over film composition and uniformity, making it suitable for precise applications.
- Plating: Can achieve high deposition rates, especially in electroplating processes. The thickness and uniformity of the coating can be controlled by adjusting parameters like current density and plating time.
-
Material Compatibility:
- Sputtering: Can deposit a wide range of materials, including metals, alloys, and ceramics. It is particularly useful for materials with high melting points that are difficult to evaporate.
- Plating: Primarily used for depositing metals and alloys. The process is limited to materials that can be dissolved in an electrolyte solution and reduced onto the substrate.
-
Applications:
- Sputtering: Commonly used in the semiconductor industry, optical coatings, and thin-film solar cells. It is also employed in creating hard coatings for tools and decorative coatings.
- Plating: Widely used in industries such as automotive (for corrosion resistance), electronics (for conductive layers), and jewelry (for decorative finishes).
-
Advantages and Limitations:
-
Sputtering:
- Advantages: High precision, ability to deposit complex materials, good adhesion, and uniformity.
- Limitations: Lower deposition rates, higher equipment costs, and the need for a vacuum environment.
-
Plating:
- Advantages: High deposition rates, cost-effectiveness for large-scale production, and the ability to coat complex geometries.
- Limitations: Limited to conductive substrates, potential for environmental concerns due to chemical waste, and less control over film composition compared to sputtering.
-
Sputtering:
In summary, sputtering and plating are distinct deposition techniques with unique mechanisms, environments, and applications. Sputtering excels in precision and material versatility, while plating is favored for its speed and cost-effectiveness in large-scale metal deposition. The choice between the two depends on the specific requirements of the application, such as the desired material properties, deposition rate, and substrate characteristics.
Summary Table:
Aspect | Sputtering | Plating |
---|---|---|
Mechanism | Physical vapor deposition (PVD) using energetic ions to eject target atoms. | Electrochemical reduction of metal ions in a solution. |
Environment | Vacuum or low-pressure with inert gases. | Liquid medium (electrolyte solution). |
Energy Source | Electrical energy to generate plasma. | Electrical energy to drive reduction reactions. |
Deposition Rate | Lower rate, high precision. | Higher rate, suitable for large-scale production. |
Material Compatibility | Metals, alloys, ceramics. | Primarily metals and alloys. |
Applications | Semiconductors, optical coatings, solar cells. | Automotive, electronics, jewelry. |
Advantages | High precision, material versatility, good adhesion. | High deposition rates, cost-effective for large-scale production. |
Limitations | Lower deposition rates, higher equipment costs, vacuum required. | Limited to conductive substrates, environmental concerns with chemical waste. |
Need help choosing the right deposition technique? Contact our experts today for personalized guidance!