Sputtering, while a widely used thin-film deposition technique, has several notable disadvantages. These include high capital expenses, relatively low deposition rates for certain materials, susceptibility to film contamination, and challenges in controlling film thickness. Additionally, sputtering can degrade sensitive materials like organic solids due to ionic bombardment and requires complex equipment and maintenance. The process also faces limitations in material selection and integration with other techniques like lift-off processes. These drawbacks make sputtering less suitable for specific applications, particularly where precision, cost-efficiency, or material compatibility are critical.
Key Points Explained:
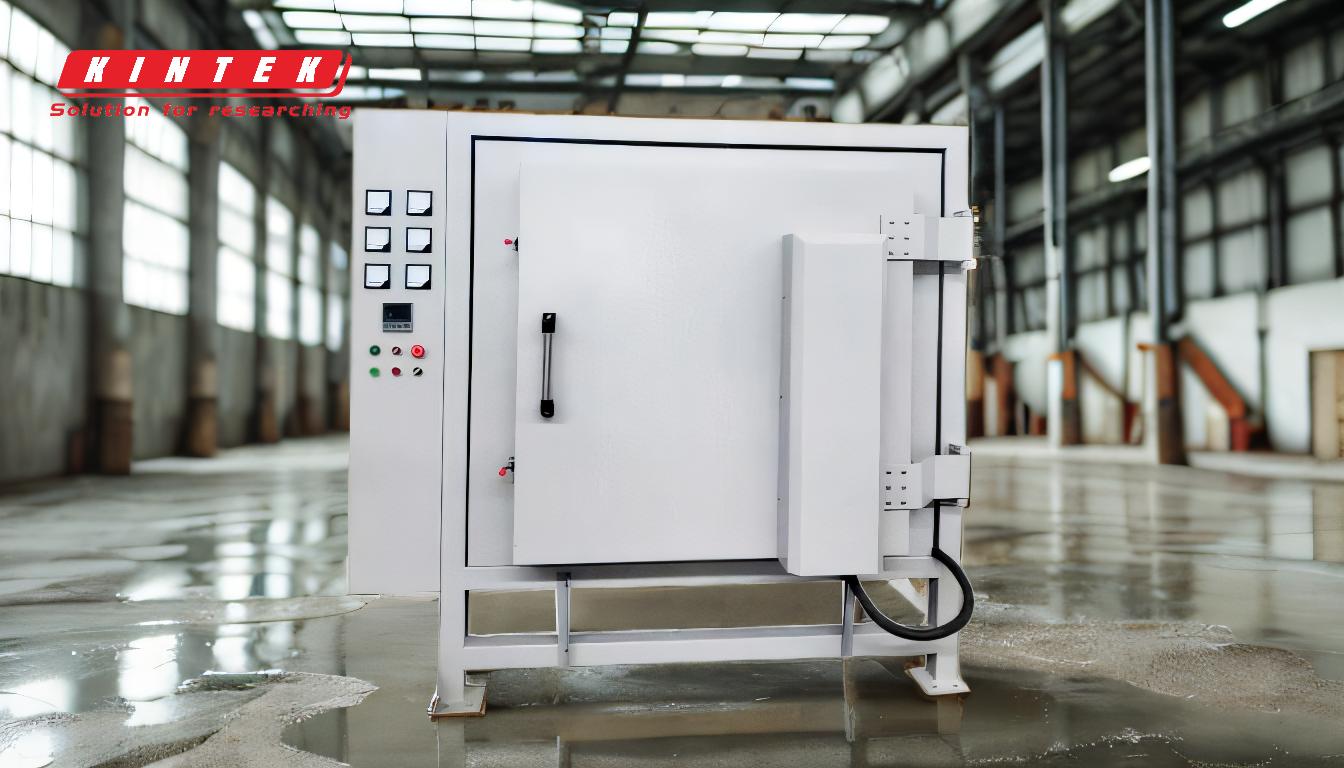
-
High Capital Expenses:
- Sputtering equipment is complex and requires significant investment in high-pressure devices and vacuum systems. This makes the initial setup cost-intensive, which can be a barrier for smaller-scale operations or research labs.
-
Low Deposition Rates:
- For certain materials, such as SiO2, the deposition rates in sputtering are relatively low compared to other techniques like evaporation. This can lead to longer processing times and reduced throughput, impacting overall efficiency.
-
Film Contamination:
- Sputtering has a greater tendency to introduce impurities into the substrate compared to evaporation. This is because sputtering operates under a lesser vacuum range, allowing impurities from the source materials or sputtering gases to diffuse into the film.
-
Material Degradation:
- Some materials, particularly organic solids, are susceptible to degradation due to ionic bombardment during the sputtering process. This limits the range of materials that can be effectively deposited using this technique.
-
Substrate Temperature Rise:
- The sputtering process can cause a significant rise in substrate temperature, which may be detrimental to temperature-sensitive materials or substrates. This necessitates additional cooling systems, increasing energy costs and reducing production rates.
-
Difficulty in Film Thickness Control:
- Achieving precise control over film thickness is challenging in sputtering. This can be a critical limitation in applications requiring highly uniform or specific film properties.
-
Integration Challenges with Lift-Off Processes:
- Sputtering is difficult to combine with lift-off processes used for structuring films. The diffuse transport characteristic of sputtering makes full shadowing impossible, leading to contamination issues and complicating the fabrication of patterned films.
-
Material Selection Limitations:
- The selection of coating materials in sputtering is limited by their melting temperatures. High-melting-point materials may not be suitable for sputtering, restricting the range of applications.
-
Maintenance and Operational Complexity:
- Sputtering systems require regular maintenance and careful control of process parameters. This adds to operational complexity and can lead to downtime, affecting productivity.
-
Impurity Introduction from Sputtering Gases:
- Inert sputtering gases, such as argon, can become impurities in the growing film. This is particularly problematic in applications requiring high-purity films, such as in semiconductor manufacturing.
In summary, while sputtering is a versatile and widely used deposition technique, its disadvantages—ranging from high costs and low deposition rates to contamination and material degradation—make it less suitable for certain applications. Understanding these limitations is crucial for selecting the appropriate deposition method based on specific project requirements.
Summary Table:
Disadvantage | Description |
---|---|
High Capital Expenses | Complex equipment and vacuum systems require significant initial investment. |
Low Deposition Rates | Slower deposition for materials like SiO2 compared to evaporation techniques. |
Film Contamination | Greater susceptibility to impurities due to lesser vacuum ranges. |
Material Degradation | Organic solids degrade under ionic bombardment, limiting material compatibility. |
Substrate Temperature Rise | Heat-sensitive materials may require additional cooling systems. |
Difficulty in Film Thickness Control | Challenges in achieving precise and uniform film thickness. |
Integration with Lift-Off Processes | Difficult to combine with lift-off processes due to diffuse transport. |
Material Selection Limitations | High-melting-point materials may not be suitable for sputtering. |
Maintenance and Operational Complexity | Requires regular maintenance and careful control of process parameters. |
Impurity Introduction from Gases | Inert gases like argon can become impurities in high-purity films. |
Need help choosing the right deposition technique? Contact our experts today to find the best solution for your project!