Sputtering is a widely used thin-film deposition technique that involves the ejection of atoms from a target material by bombarding it with high-energy ions. The energy range of sputtering typically spans from several hundred electron volts (eV) to several kiloelectron volts (keV). This energy range is crucial for dislodging atoms from the target material and depositing them onto a substrate. The minimum energy required to remove an atom from the target surface is generally 3 to 4 times the binding energy of the target atoms, ensuring efficient sputtering. This process is highly versatile and is employed in various industries, including semiconductor manufacturing, optics, and surface finishing.
Key Points Explained:
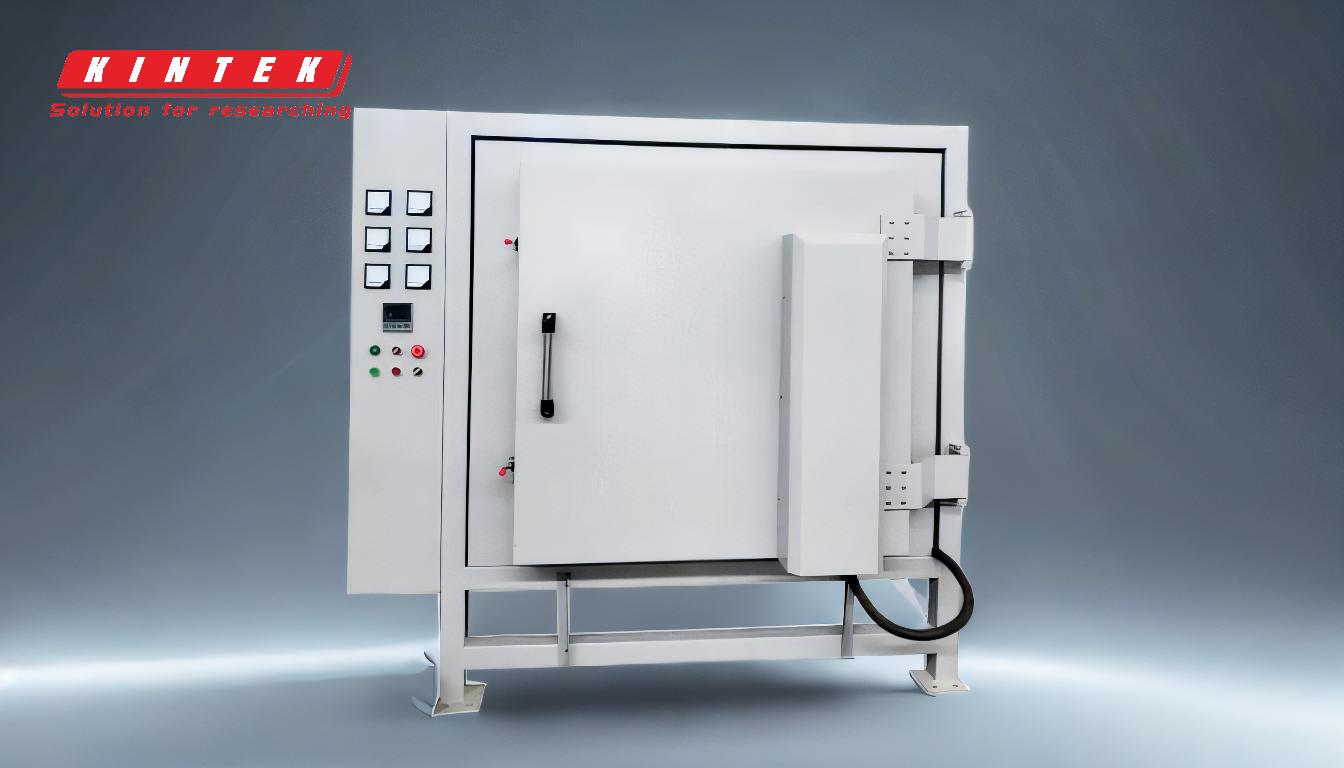
-
Energy Range of Sputtering:
- The energy of the ion beam used in sputtering typically ranges from several hundred volts to several kilovolts. This range is necessary to provide sufficient energy to dislodge atoms from the target material.
- The energy required to eject an atom from the target surface is known as the primary energy, which is usually 3 to 4 times greater than the binding energy of the target atoms. This ensures that the atoms are effectively removed from the target.
-
Process of Sputtering:
- Sputtering involves creating a vacuum in the deposition chamber and introducing an inert gas (usually Argon).
- A high voltage is applied to generate a glow discharge, creating positively charged ions (e.g., Ar+).
- These ions are accelerated towards the negatively charged target (cathode), where they collide and transfer their energy to the target atoms.
- The energy transfer causes the target atoms to be ejected as neutral particles, which then travel and deposit onto the substrate, forming a thin film.
-
Applications and Advantages of Sputtering:
- Sputtering is used in various industries, including semiconductor processing, precision optics, and surface finishing.
- The technique offers several advantages, such as strong adhesion, excellent step coverage, uniform film thickness, and the ability to deposit alloy films.
- It is also compatible with mass production due to its high reproducibility, time-power controllability, and low target replacement frequency.
-
Factors Influencing Sputtering Energy:
- The binding energy of the target material's atoms plays a crucial role in determining the minimum energy required for sputtering.
- The type of inert gas used (e.g., Argon) and the applied voltage also influence the energy range and efficiency of the sputtering process.
- The geometry of the deposition chamber and the distance between the target and substrate can affect the energy distribution and deposition rate.
-
Comparison with Other Deposition Techniques:
- Sputtering is a type of Physical Vapor Deposition (PVD), which differs from Chemical Vapor Deposition (CVD) in that it does not involve chemical reactions.
- Compared to other PVD techniques, sputtering offers better film uniformity and adhesion, making it suitable for applications requiring high precision and durability.
In summary, the energy range of sputtering is a critical parameter that ensures the efficient removal of target atoms and their deposition onto a substrate. This range, typically from several hundred eV to several keV, is influenced by factors such as the binding energy of the target atoms, the type of inert gas used, and the applied voltage. The versatility and advantages of sputtering make it a preferred method for thin-film deposition in various high-tech industries.
Summary Table:
Aspect | Details |
---|---|
Energy Range | Several hundred eV to several keV |
Minimum Energy | 3-4 times the binding energy of target atoms |
Process | Inert gas (Argon), high voltage, glow discharge, neutral particle ejection |
Applications | Semiconductor manufacturing, precision optics, surface finishing |
Advantages | Strong adhesion, uniform film thickness, high reproducibility |
Key Factors | Binding energy, inert gas type, applied voltage, chamber geometry |
Unlock the potential of sputtering for your industry—contact our experts today!