Stainless steel reactors are constructed using stainless steel alloys, which are chosen for their high strength, durability, and resistance to corrosion. These properties make stainless steel an ideal material for reactors operating under high-pressure conditions, typically up to 200 bar. The choice of stainless steel alloy depends on the specific application, including the chemical environment and pressure requirements. While other materials like glass or specialized alloys (e.g., Hastelloy or Inconel) are used for specific conditions, stainless steel remains a versatile and widely used material for reactor construction due to its balance of mechanical properties and chemical resistance.
Key Points Explained:
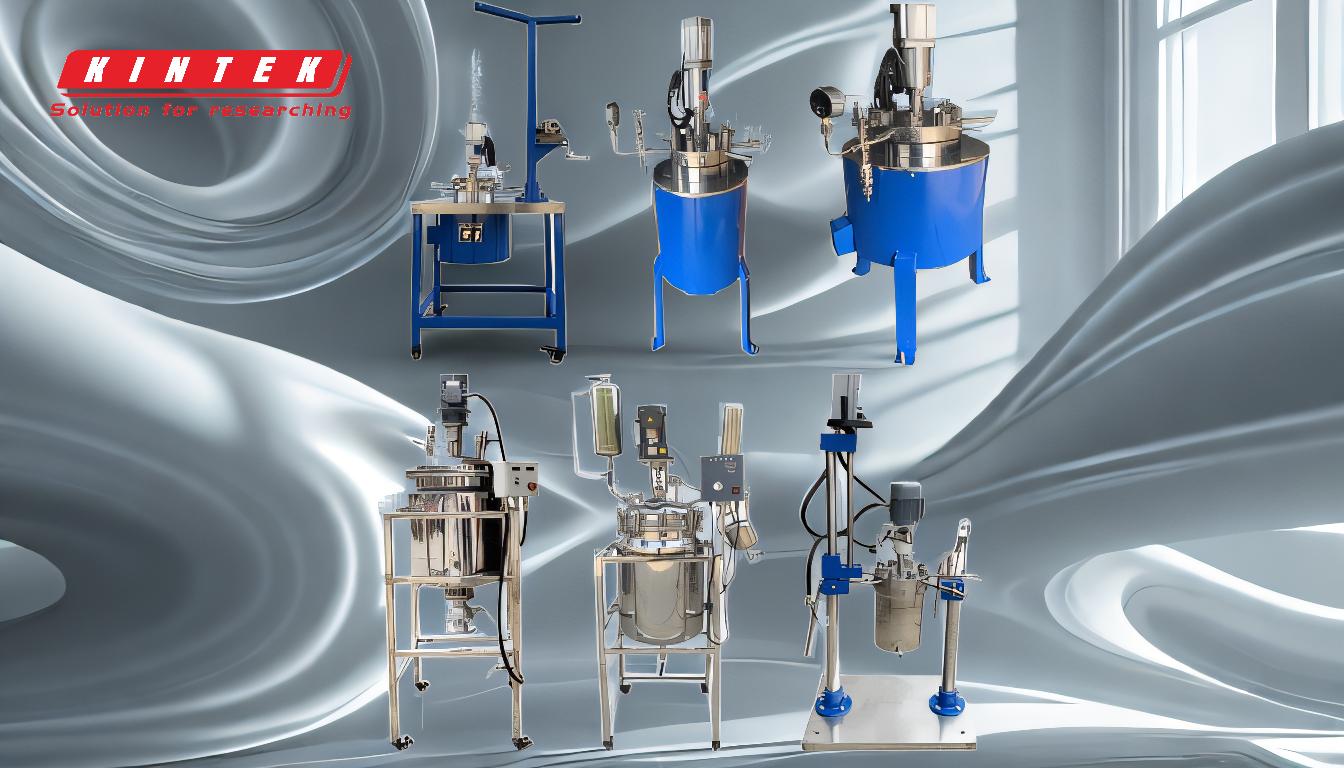
-
Material Composition of Stainless Steel Reactors:
- Stainless steel reactors are constructed using stainless steel alloys. These alloys are composed primarily of iron, with added elements such as chromium, nickel, and molybdenum to enhance their properties.
- The chromium content in stainless steel provides corrosion resistance by forming a passive oxide layer on the surface, while nickel improves ductility and toughness.
-
Key Properties of Stainless Steel Alloys:
- High Strength: Stainless steel alloys are known for their mechanical strength, making them suitable for high-pressure applications.
- Durability: These alloys can withstand prolonged use in harsh environments without significant degradation.
- Corrosion Resistance: The chromium content ensures resistance to corrosion, which is critical for reactors handling corrosive chemicals.
- Temperature Resistance: Stainless steel can maintain its structural integrity at elevated temperatures, which is essential for many chemical processes.
-
Pressure Range for Stainless Steel Reactors:
- Stainless steel is commonly used for reactors rated up to 200 bar. This makes it suitable for a wide range of industrial applications, including chemical synthesis, pharmaceutical production, and food processing.
- For lower pressures (around 5 bar), materials like glass may be preferred due to their transparency, allowing direct observation of the reaction. For extremely high pressures (a few thousand bars), specialized alloys like Hastelloy or Inconel are used.
-
Comparison with Other Materials:
- Glass Reactors: Used for low-pressure applications where visual monitoring is required. Glass is resistant to acids but lacks the strength for high-pressure operations.
- Specialized Alloys (Hastelloy, Inconel): These materials are used for extreme conditions, such as very high pressures or highly corrosive environments, where stainless steel may not suffice.
- Carbon Steel: While cheaper, carbon steel lacks the corrosion resistance of stainless steel and is less suitable for many chemical processes.
-
Applications of Stainless Steel Reactors:
- Stainless steel reactors are widely used in industries such as:
- Chemical Manufacturing: For processes involving corrosive substances or high pressures.
- Pharmaceuticals: Where cleanliness and corrosion resistance are critical.
- Food and Beverage: For processes requiring hygienic conditions and resistance to cleaning agents.
- Stainless steel reactors are widely used in industries such as:
-
Advantages of Stainless Steel in Reactor Construction:
- Versatility: Suitable for a wide range of chemical processes and operating conditions.
- Longevity: Resistant to wear and tear, reducing maintenance costs over time.
- Hygienic Properties: Easy to clean and sterilize, making it ideal for industries with strict hygiene standards.
-
Limitations of Stainless Steel:
- While stainless steel is highly versatile, it may not be suitable for extremely high-pressure or highly corrosive environments, where specialized alloys are preferred.
- The cost of stainless steel reactors can be higher than those made from carbon steel or glass, but this is often justified by their durability and performance.
In summary, stainless steel reactors are constructed using stainless steel alloys, which provide a combination of strength, durability, and corrosion resistance. These properties make stainless steel an ideal material for reactors operating under moderate to high pressures, particularly in industries where chemical resistance and hygiene are critical. While other materials like glass or specialized alloys are used for specific applications, stainless steel remains a widely preferred choice due to its versatility and reliability.
Summary Table:
Aspect | Details |
---|---|
Material Composition | Iron, chromium, nickel, molybdenum for enhanced properties. |
Key Properties | High strength, durability, corrosion resistance, temperature resistance. |
Pressure Range | Up to 200 bar, suitable for moderate to high-pressure applications. |
Applications | Chemical manufacturing, pharmaceuticals, food and beverage industries. |
Advantages | Versatility, longevity, hygienic properties, and reduced maintenance costs. |
Limitations | Not ideal for extremely high pressures or highly corrosive environments. |
Interested in stainless steel reactors for your industry? Contact us today to learn more!