Blown film extrusion is a manufacturing process used to create plastic films, commonly seen in products like plastic bags, packaging materials, and agricultural films. It involves melting plastic pellets and extruding them through a circular die. As the molten plastic emerges, air is blown into the center of the die, causing the plastic to expand into a bubble or tube. This bubble is then cooled, flattened, and rolled into a film. The process allows for the production of films with varying thicknesses, widths, and properties, making it versatile for a wide range of applications.
Key Points Explained:
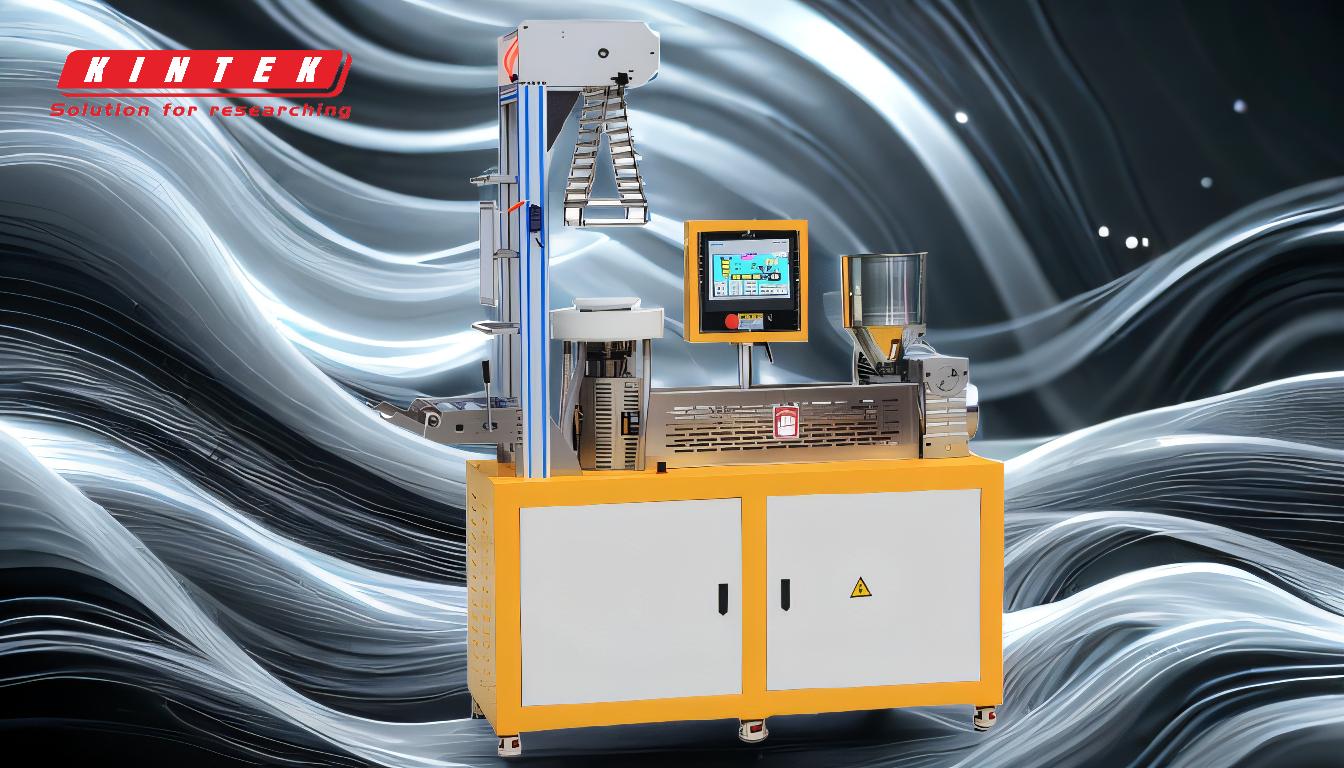
-
Process Overview:
- Blown film extrusion begins with plastic pellets being fed into an extruder, where they are melted and homogenized.
- The molten plastic is then forced through a circular die, forming a continuous tube of plastic.
- Air is introduced into the center of the die, inflating the tube into a bubble. This bubble is then cooled, typically using air rings, to solidify the plastic.
- The cooled bubble is collapsed into a flat film and wound onto rolls for further processing or packaging.
-
Key Components of the Process:
- Extruder: The extruder is the heart of the blown film process. It consists of a screw that rotates within a heated barrel, melting the plastic pellets and pushing the molten plastic through the die.
- Circular Die: The die shapes the molten plastic into a continuous tube. The design of the die can influence the thickness and uniformity of the film.
- Air Ring: The air ring cools the plastic bubble as it exits the die. Proper cooling is essential to control the film's properties, such as strength and clarity.
- Nip Rolls: These rolls flatten the bubble into a double-layered film, which is then wound onto a roll.
-
Advantages of Blown Film Extrusion:
- Versatility: The process can produce films with a wide range of thicknesses, widths, and properties, making it suitable for various applications.
- Cost-Effectiveness: Blown film extrusion is generally more cost-effective than other film production methods, especially for large-scale production.
- Strength and Durability: The biaxial orientation of the film during the blowing process results in films with excellent strength and durability.
-
Applications of Blown Film:
- Packaging: Blown film is widely used in the packaging industry for products such as plastic bags, shrink wrap, and food packaging.
- Agriculture: Agricultural films, such as mulch films and greenhouse covers, are often produced using blown film extrusion.
- Medical: Blown film is used in the production of medical packaging and disposable medical products.
- Construction: Films used in construction, such as vapor barriers and protective coverings, are often made using this process.
-
Considerations for Equipment and Consumable Purchasers:
- Material Selection: The type of plastic resin used (e.g., LDPE, HDPE, LLDPE) will affect the properties of the final film. Purchasers should consider the specific requirements of their application when selecting materials.
- Die Design: The design of the die can significantly impact the quality of the film. Purchasers should ensure that the die is suitable for their desired film thickness and width.
- Cooling System: Efficient cooling is crucial for achieving the desired film properties. Purchasers should evaluate the cooling system's capacity and effectiveness.
- Production Speed: The speed at which the film is produced can affect the overall efficiency of the process. Purchasers should consider the production speed capabilities of the equipment.
In summary, blown film extrusion is a versatile and cost-effective process for producing plastic films with a wide range of applications. Understanding the key components, advantages, and considerations can help equipment and consumable purchasers make informed decisions to meet their specific needs.
Summary Table:
Aspect | Details |
---|---|
Process Overview | Melts plastic pellets, extrudes through a die, inflates with air, cools, and flattens into film. |
Key Components | Extruder, circular die, air ring, nip rolls. |
Advantages | Versatility, cost-effectiveness, strength, and durability. |
Applications | Packaging, agriculture, medical, construction. |
Purchasing Considerations | Material selection, die design, cooling system, production speed. |
Ready to optimize your plastic film production? Contact our experts today for tailored solutions!