The milling process of rubber is a critical step in rubber manufacturing, involving several stages to transform raw rubber into a usable form. The process typically begins with mastication, where rubber is softened and made more pliable. This is followed by mixing, where additives are incorporated to enhance the rubber's properties. The next step is shaping, where the rubber is formed into the desired shape through methods like extrusion or calendering. Finally, curing or vulcanization is performed to stabilize the rubber and improve its durability. Each of these steps is essential for producing high-quality rubber products.
Key Points Explained:
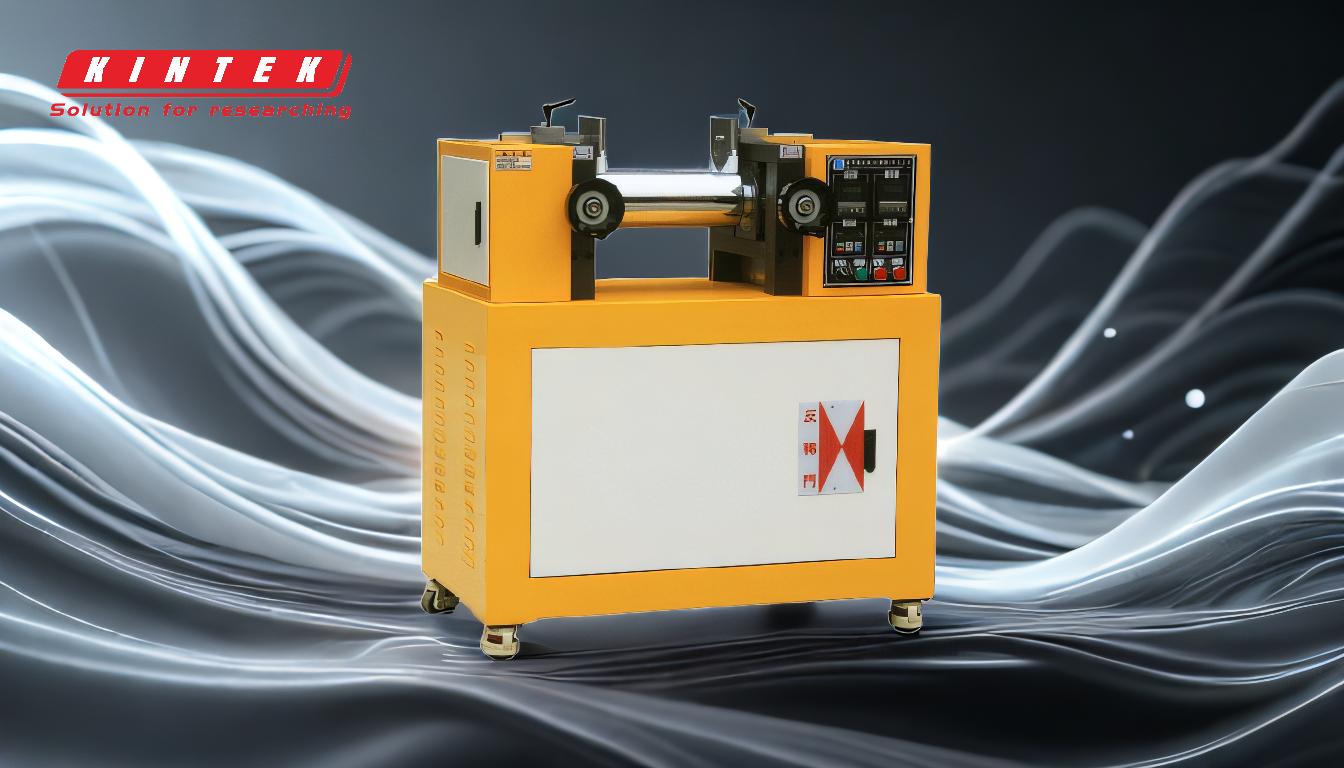
-
Mastication of Rubber:
- Purpose: The first step in the rubber milling process, mastication involves softening the rubber to make it more pliable and easier to work with.
- Process: Raw rubber is passed through a mill, where it is subjected to mechanical shearing and heat. This breaks down the rubber's molecular structure, reducing its viscosity and making it easier to mix with other ingredients.
- Importance: Mastication is crucial for ensuring that the rubber can be uniformly mixed with additives, which is essential for achieving the desired properties in the final product.
-
Mixing Rubber:
- Purpose: This step involves incorporating various additives into the rubber to enhance its properties, such as strength, elasticity, and resistance to wear and tear.
- Process: The masticated rubber is mixed with additives like carbon black, sulfur, and other chemicals in a mixer. The mixture is then homogenized to ensure uniform distribution of the additives.
- Importance: Proper mixing is vital for achieving the desired performance characteristics in the final rubber product. Inconsistent mixing can lead to defects and reduced performance.
-
Shaping Rubber:
- Purpose: After mixing, the rubber is shaped into the desired form, which can be done through various methods depending on the final product requirements.
-
Methods:
- Extrusion: The rubber mixture is forced through a die to create long, continuous shapes like tubes or profiles.
- Calendering: The rubber is passed through a series of rollers to create sheets or films of uniform thickness.
- Molding: The rubber is placed into a mold and compressed to form specific shapes.
- Importance: Shaping is crucial for producing rubber products with the correct dimensions and geometry, which are essential for their intended applications.
-
Curing or Vulcanization:
- Purpose: The final step in the rubber milling process, curing involves heating the shaped rubber to stabilize it and improve its durability.
- Process: The rubber is heated in the presence of sulfur or other curing agents, which form cross-links between the rubber molecules. This process, known as vulcanization, enhances the rubber's strength, elasticity, and resistance to heat and chemicals.
- Importance: Curing is essential for transforming the rubber into a durable material that can withstand the stresses and strains of its intended use. Without proper curing, the rubber would remain soft and prone to deformation.
In summary, the milling process of rubber is a multi-step procedure that involves mastication, mixing, shaping, and curing. Each step plays a critical role in transforming raw rubber into a high-quality, durable product suitable for various applications. Understanding these steps is essential for anyone involved in the rubber manufacturing industry, as it ensures the production of rubber products that meet the required performance standards.
Summary Table:
Step | Purpose | Process | Importance |
---|---|---|---|
Mastication | Soften rubber for pliability and easier mixing | Mechanical shearing and heat to break down molecular structure | Ensures uniform mixing with additives for desired properties |
Mixing | Incorporate additives to enhance properties | Mixing with carbon black, sulfur, and chemicals; homogenizing | Achieves consistent performance; prevents defects in the final product |
Shaping | Form rubber into desired shapes | Extrusion, calendering, or molding | Produces correct dimensions and geometry for intended applications |
Curing | Stabilize rubber and improve durability | Heating with sulfur to form cross-links (vulcanization) | Enhances strength, elasticity, and resistance to heat and chemicals |
Need expert guidance on rubber milling? Contact us today to optimize your manufacturing process!