Dual extrusion is a manufacturing process that involves the simultaneous extrusion of two different materials through a single die to create a unified part. This technique is particularly useful when a product requires a combination of properties, such as a soft, flexible material integrated with a hard, durable one. The process is commonly used in industries where products need to exhibit both flexibility and strength, such as in automotive seals, medical devices, or consumer goods. Below, we will explore the key steps and considerations involved in dual extrusion, providing a detailed understanding of how this process works and its applications.
Key Points Explained:
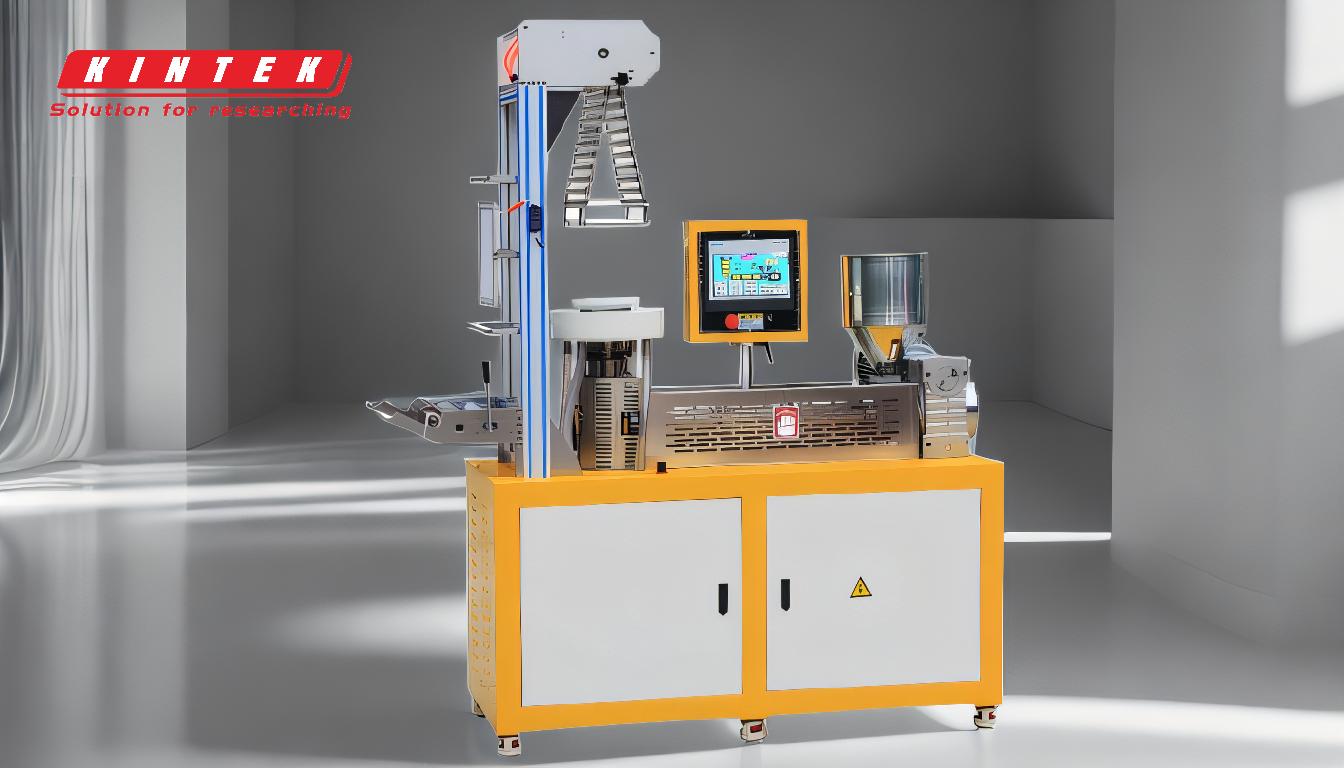
-
Understanding Dual Extrusion
- Dual extrusion, also known as co-extrusion, is a process where two or more materials are extruded simultaneously through a single die to form a single, integrated part.
- The materials used in dual extrusion can vary widely, including thermoplastics, elastomers, or other polymers, depending on the desired properties of the final product.
- This process is ideal for creating parts that require a combination of properties, such as flexibility and durability, or for achieving specific aesthetic or functional characteristics.
-
Materials Used in Dual Extrusion
- Soft Materials: These are typically elastomers or flexible polymers that provide cushioning, sealing, or vibration-dampening properties.
- Hard Materials: These are rigid polymers or thermoplastics that offer structural integrity, durability, and resistance to wear and tear.
- The materials must be compatible in terms of their melting points, adhesion properties, and flow characteristics to ensure a seamless bond during extrusion.
-
The Dual Extrusion Process
- Material Preparation: The two materials are prepared separately, often in pellet or granular form, and fed into their respective extruders.
- Extrusion: Each material is heated and melted in its extruder. The molten materials are then pushed through a shared die, where they merge and form a single, cohesive part.
- Cooling and Solidification: The extruded part is cooled, often using water baths or air cooling, to solidify the materials and lock in their combined properties.
- Post-Processing: The part may undergo additional processes, such as cutting, trimming, or surface treatment, to achieve the final desired shape and finish.
-
Advantages of Dual Extrusion
- Combined Properties: Dual extrusion allows manufacturers to create parts with a combination of soft and hard materials, offering both flexibility and durability.
- Cost Efficiency: By combining materials in a single process, manufacturers can reduce production steps and material waste.
- Design Flexibility: This process enables the creation of complex shapes and designs that would be difficult or impossible to achieve with single-material extrusion.
-
Applications of Dual Extrusion
- Automotive Industry: Used for seals, gaskets, and weatherstripping that require both flexibility and durability.
- Medical Devices: Ideal for creating components that need to be both soft for patient comfort and rigid for structural support.
- Consumer Goods: Commonly used in products like tool handles, grips, and footwear, where a combination of soft and hard materials enhances functionality and comfort.
-
Challenges and Considerations
- Material Compatibility: Ensuring that the two materials bond well and do not delaminate during or after extrusion is critical.
- Process Control: Precise control over temperature, pressure, and flow rates is necessary to achieve consistent results.
- Tooling Design: The die must be carefully designed to accommodate the flow and merging of the two materials without causing defects.
By understanding the dual extrusion process, manufacturers can leverage its advantages to create innovative products that meet specific performance requirements. Whether for automotive, medical, or consumer applications, dual extrusion offers a versatile and efficient solution for combining materials with contrasting properties.
Summary Table:
Aspect | Details |
---|---|
Process | Simultaneous extrusion of two materials through a single die. |
Materials | Soft (elastomers, flexible polymers) and hard (rigid polymers, thermoplastics). |
Advantages | Combined properties, cost efficiency, design flexibility. |
Applications | Automotive seals, medical devices, consumer goods (handles, grips, etc.). |
Challenges | Material compatibility, process control, tooling design. |
Discover how dual extrusion can elevate your product design—contact our experts today!