The process of mixing rubber compounds is a critical step in rubber manufacturing, where raw materials are transformed into a uniform rubber compound. This involves blending, softening, homogenizing, and dispersing ingredients through mechanical shear forces and heat. The process ensures thorough contact and uniform dispersion of compounding agents within the rubber matrix. Key equipment like internal mixers, with their rotating rotors, play a vital role in achieving efficient mixing by shearing and rubbing the material, reducing viscosity, and enhancing wettability. The mixed compound is then further processed through methods like extrusion, calendering, and vulcanization to produce finished rubber products.
Key Points Explained:
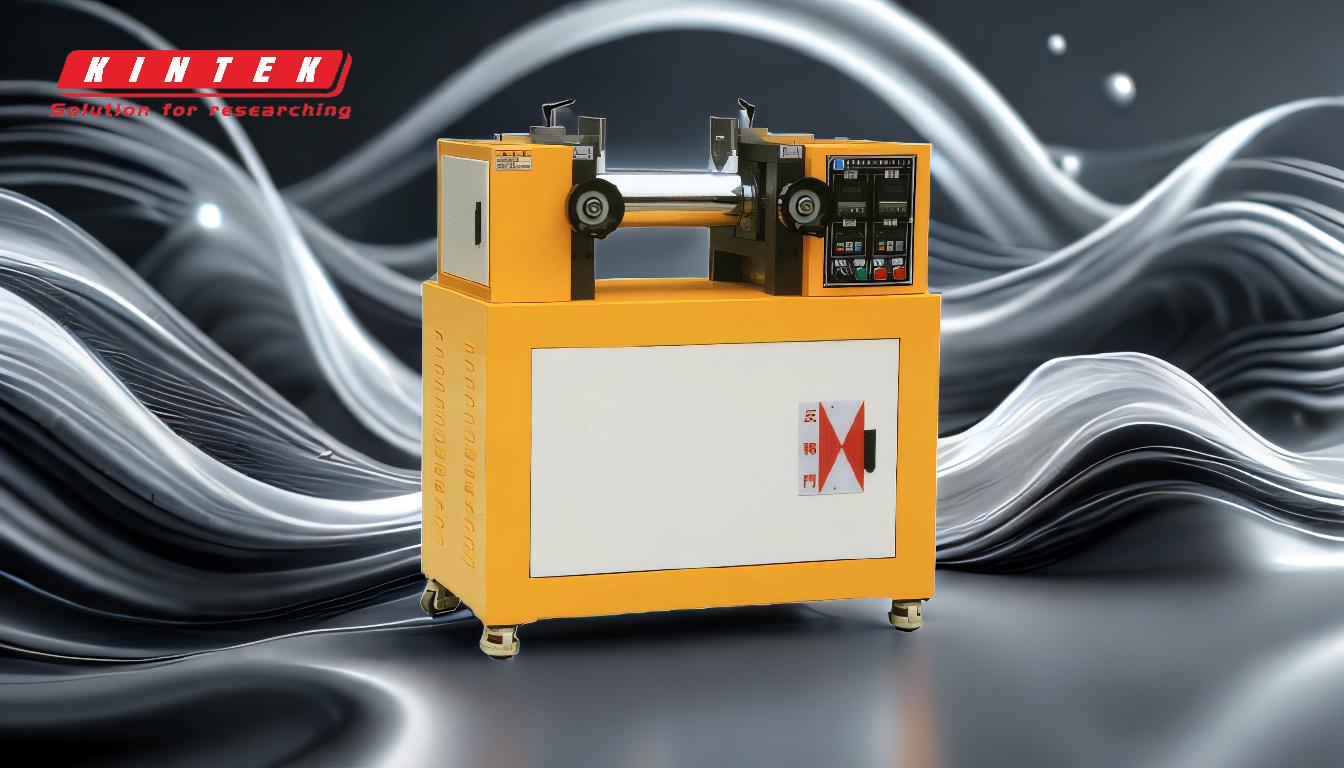
-
Purpose of Rubber Mixing:
- Rubber mixing is the process of combining raw materials (such as natural rubber, synthetic rubber, fillers, plasticizers, and curing agents) to create a homogeneous rubber compound.
- The goal is to achieve uniform dispersion of all ingredients, ensuring consistent properties in the final product.
-
Mechanical Shear Forces and Heat:
- The mixing process relies on mechanical shear forces, which are generated by equipment like internal mixers.
- As the rotors rotate, they shear and rub the rubber material, generating heat. This heat reduces the viscosity of the rubber, making it easier to blend and disperse the compounding agents.
-
Role of Internal Mixers:
- Internal mixers are commonly used for rubber mixing. They consist of two rotors that rotate relative to each other, creating shear forces.
- The ridges on the rotors continuously stir and shear the material, ensuring thorough mixing and uniform dispersion of additives.
- The heat generated during mixing also improves the wettability of the rubber on the compounding agent's surface, enhancing contact and dispersion.
-
Key Steps in the Mixing Process:
- Blending: Raw materials are combined in specific proportions to create the desired rubber compound.
- Softening: Mechanical shear forces and heat soften the rubber, making it more pliable and easier to mix.
- Homogenizing: The mixture is processed until it achieves a uniform consistency.
- Dispersing: Compounding agents (e.g., fillers, curing agents) are evenly distributed throughout the rubber matrix.
-
Challenges in Mixing:
- Natural rubber (NR) tends to increase in viscosity during long storage, which can complicate the mixing process. Pre-treatment or conditioning may be required to address this issue.
- Achieving uniform dispersion of additives, especially in high-viscosity compounds, can be challenging and requires precise control of mixing parameters.
-
Post-Mixing Processes:
- After mixing, the rubber compound undergoes additional processes to shape and cure it into finished products. These include:
- Extrusion: Shaping the rubber into continuous profiles or sheets.
- Calendering: Rolling the rubber into thin sheets or coating fabrics using a rubber calender.
- Vulcanization: Curing the rubber to improve its strength, elasticity, and durability through chemical cross-linking using a rubber vulcanizer.
- After mixing, the rubber compound undergoes additional processes to shape and cure it into finished products. These include:
-
Importance of Temperature Control:
- Temperature plays a critical role in the mixing process. Excessive heat can degrade the rubber, while insufficient heat may hinder proper dispersion of additives.
- Modern mixers often include cooling systems to regulate temperature and prevent overheating.
-
Quality Assurance:
- The quality of the mixed rubber compound is assessed through tests for uniformity, dispersion, and mechanical properties.
- Consistent mixing ensures that the final product meets the required specifications for strength, elasticity, and other performance characteristics.
By understanding these key points, purchasers and manufacturers can ensure that the rubber mixing process is optimized for quality, efficiency, and consistency in producing high-performance rubber compounds.
Summary Table:
Key Aspect | Details |
---|---|
Purpose | Combine raw materials to create a homogeneous rubber compound. |
Key Equipment | Internal mixers with rotating rotors for efficient shearing and mixing. |
Mixing Steps | Blending, softening, homogenizing, and dispersing ingredients. |
Challenges | Viscosity changes in natural rubber, uniform dispersion of additives. |
Post-Mixing Processes | Extrusion, calendering, and vulcanization for shaping and curing. |
Temperature Control | Critical to prevent degradation and ensure proper dispersion of additives. |
Quality Assurance | Tests for uniformity, dispersion, and mechanical properties. |
Optimize your rubber mixing process for quality and efficiency—contact our experts today!