Sputtering is a versatile thin film deposition process widely used in industries such as semiconductors, optics, and coatings. It involves the ejection of atoms from a target material through bombardment by high-energy ions, typically in a vacuum chamber filled with a gas like argon. These ejected atoms then deposit onto a substrate, forming a thin, uniform coating. The process is highly controllable and can be tailored for specific applications, such as improving secondary electron emission in scanning electron microscopy or creating anti-reflective coatings. The sputtering process can be broken down into several key steps, including vacuum preparation, substrate cleaning, material deposition, and cooling. Techniques like direct current (DC) and radio frequency (RF) sputtering are commonly used, and reactive sputtering introduces chemical reactions to enhance film properties.
Key Points Explained:
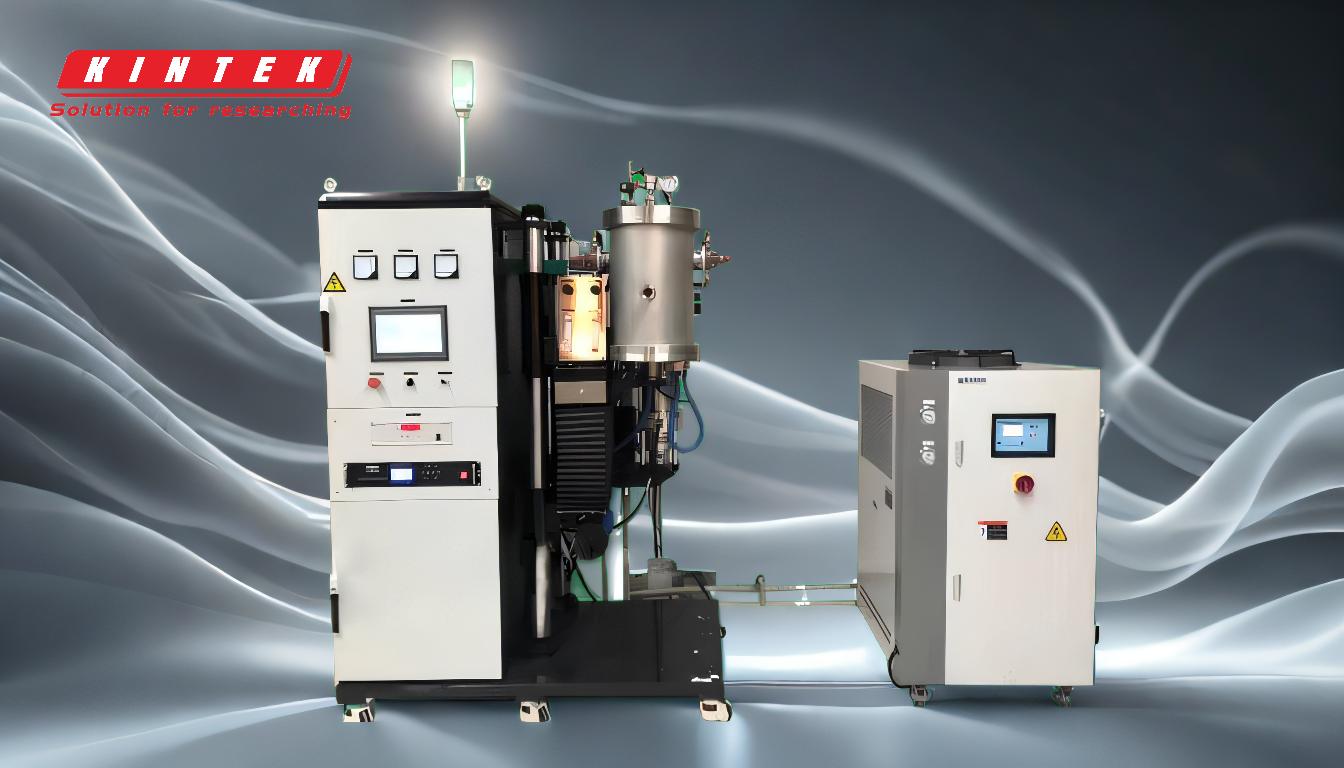
-
Basic Mechanism of Sputtering:
- Sputtering involves bombarding a target material with high-energy ions, typically from a gas like argon, in a vacuum chamber.
- The ions collide with the target, causing atoms to be ejected (sputtered) from its surface.
- These ejected atoms travel through the vacuum and deposit onto a substrate, forming a thin, uniform film.
-
Steps in the Sputtering Process:
- Ramp Up: The vacuum chamber is prepared by gradually increasing temperature and decreasing pressure to create the necessary environment for sputtering.
- Etching: The substrate is cleaned using cathodic cleaning to remove surface contaminants, ensuring better adhesion of the deposited film.
- Coating: The target material is bombarded with ions, and the ejected atoms are projected onto the substrate surface, forming the desired coating.
- Ramp Down: The chamber is gradually cooled and returned to ambient pressure, completing the process.
-
Types of Sputtering Techniques:
- Direct Current (DC) Sputtering: A simple and widely used method where a DC voltage is applied between the target (cathode) and the substrate (anode). It is effective for conductive materials.
- Radio Frequency (RF) Sputtering: Used for insulating materials, RF sputtering applies an alternating current to the target, preventing charge buildup.
- Reactive Sputtering: Combines conventional sputtering with chemical reactions. Reactive gases like nitrogen or oxygen are introduced, reacting with the sputtered atoms to form compounds such as nitrides or oxides on the substrate.
-
Applications of Sputtering:
- Semiconductors: Used in integrated circuit fabrication to deposit thin films of metals and insulators.
- Optics: Creates anti-reflective coatings on glass and other optical components.
- Data Storage: Deposits magnetic layers in hard disk drives and optical layers in CDs/DVDs.
- Tool Coatings: Enhances the durability and performance of cutting tools through hard coatings.
-
Advantages of Sputtering:
- Uniformity: Produces highly uniform and dense films, even on complex geometries.
- Versatility: Can deposit a wide range of materials, including metals, alloys, and compounds.
- Control: Offers precise control over film thickness and composition.
- Low Temperature: Suitable for temperature-sensitive substrates.
-
Challenges and Considerations:
- Cost: Requires expensive equipment and high vacuum conditions.
- Deposition Rate: Can be slower compared to other deposition methods like evaporation.
- Material Limitations: Not all materials are suitable for sputtering, especially those with low sputtering yields.
-
Reactive Sputtering in Detail:
- Involves the use of reactive gases like nitrogen or oxygen, which chemically react with the sputtered metal atoms to form compounds.
- This process is used to create hard coatings, such as titanium nitride (TiN), which are widely used in cutting tools and wear-resistant applications.
- The reaction occurs on the substrate surface, and excess gas is pumped away to maintain the desired film composition.
By understanding these key points, one can appreciate the complexity and versatility of the sputtering process, making it a cornerstone of modern thin film deposition technologies.
Summary Table:
Aspect | Details |
---|---|
Basic Mechanism | Bombardment of target material with high-energy ions in a vacuum chamber. |
Key Steps | Ramp Up, Etching, Coating, Ramp Down. |
Techniques | DC Sputtering, RF Sputtering, Reactive Sputtering. |
Applications | Semiconductors, Optics, Data Storage, Tool Coatings. |
Advantages | Uniformity, Versatility, Control, Low Temperature. |
Challenges | High Cost, Slower Deposition Rate, Material Limitations. |
Discover how sputtering can enhance your projects—contact our experts today!