Blown film extrusion is a widely used manufacturing process for producing plastic films, commonly used in packaging, agriculture, and other industries. The raw materials for blown film extrusion primarily consist of thermoplastic resins, with polyethylene being the most commonly used due to its versatility, cost-effectiveness, and desirable properties. The main types of polyethylene used are Low-Density Polyethylene (LDPE), High-Density Polyethylene (HDPE), and Linear Low-Density Polyethylene (LLDPE). These materials are chosen based on the specific requirements of the film being produced, such as flexibility, strength, and transparency.
Key Points Explained:
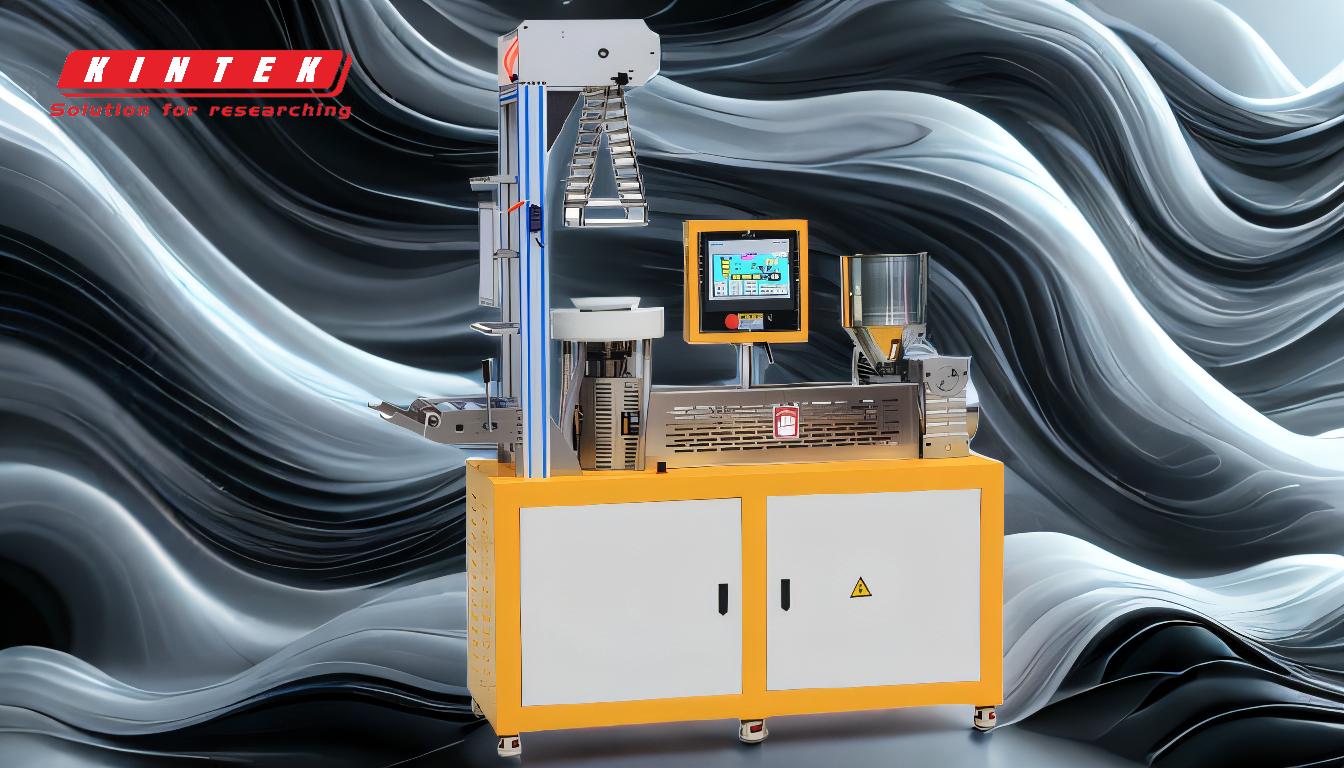
-
Primary Raw Material: Polyethylene
- Definition and Properties: Polyethylene is a thermoplastic polymer made from ethylene monomers. It is known for its flexibility, durability, and resistance to moisture and chemicals. These properties make it ideal for blown film extrusion, where the material needs to be melted, extruded, and then cooled to form a thin film.
-
Types of Polyethylene:
- Low-Density Polyethylene (LDPE): LDPE is characterized by its high flexibility and transparency. It is commonly used for applications requiring a soft, pliable film, such as plastic bags and wraps.
- High-Density Polyethylene (HDPE): HDPE is more rigid and has a higher tensile strength compared to LDPE. It is often used for applications requiring a stronger, more durable film, such as grocery bags and industrial liners.
- Linear Low-Density Polyethylene (LLDPE): LLDPE combines the flexibility of LDPE with the strength of HDPE. It is often used in applications that require a balance of strength and flexibility, such as stretch films and heavy-duty sacks.
-
Selection Criteria for Raw Materials
- End-Use Requirements: The choice of polyethylene type depends on the specific requirements of the final product. For example, LDPE is preferred for applications requiring high clarity and flexibility, while HDPE is chosen for its strength and rigidity.
- Processing Conditions: Different types of polyethylene have different melting points and flow characteristics, which can affect the extrusion process. For instance, LDPE has a lower melting point and is easier to process, making it suitable for high-speed extrusion.
- Cost Considerations: The cost of raw materials is also a significant factor in the selection process. LDPE is generally less expensive than HDPE, but the choice ultimately depends on the desired properties of the final film.
-
Additional Additives and Modifiers
- Stabilizers: These are added to the polymer to prevent degradation during the extrusion process. Stabilizers help maintain the material's properties and extend the life of the film.
- Colorants: Colorants are used to add color to the film. They can be added in the form of masterbatches, which are concentrated mixtures of pigments and additives.
- Antistatic Agents: These are added to reduce static electricity on the film surface, which can be important in applications where static could cause issues, such as in packaging electronic components.
- Slip Agents: Slip agents are used to reduce the coefficient of friction on the film surface, making it easier to handle and process.
-
Environmental and Sustainability Considerations
- Recyclability: Polyethylene films are recyclable, and many manufacturers are focusing on using recycled materials in their production processes to reduce environmental impact.
- Biodegradable Additives: Some manufacturers are incorporating biodegradable additives into polyethylene films to enhance their environmental friendliness. These additives help the film break down more quickly in the environment.
In summary, the raw material for blown film extrusion is primarily polyethylene, with LDPE, HDPE, and LLDPE being the most commonly used types. The selection of the specific type of polyethylene depends on the desired properties of the final film, processing conditions, and cost considerations. Additionally, various additives and modifiers can be incorporated to enhance the film's properties and performance. Environmental and sustainability considerations are also becoming increasingly important in the selection of raw materials for blown film extrusion.
Summary Table:
Polyethylene Type | Key Properties | Common Applications |
---|---|---|
LDPE | High flexibility, transparency | Plastic bags, wraps |
HDPE | Rigidity, high tensile strength | Grocery bags, industrial liners |
LLDPE | Balance of strength and flexibility | Stretch films, heavy-duty sacks |
Need help selecting the right polyethylene for your blown film extrusion? Contact our experts today!