The vacuum level of a thermal evaporator typically ranges between 10^-5 to 10^-7 Torr (or 10^-7 to 10^-5 mbar). This high vacuum environment is essential to ensure the purity and quality of the deposited thin film. It allows evaporated molecules to travel in a straight line from the source to the substrate without colliding with residual gas molecules, which could otherwise lead to contamination, poor film adhesion, or reduced film quality. The specific vacuum level required depends on factors such as the material being deposited, the size of the vacuum chamber, and the desired film properties.
Key Points Explained:
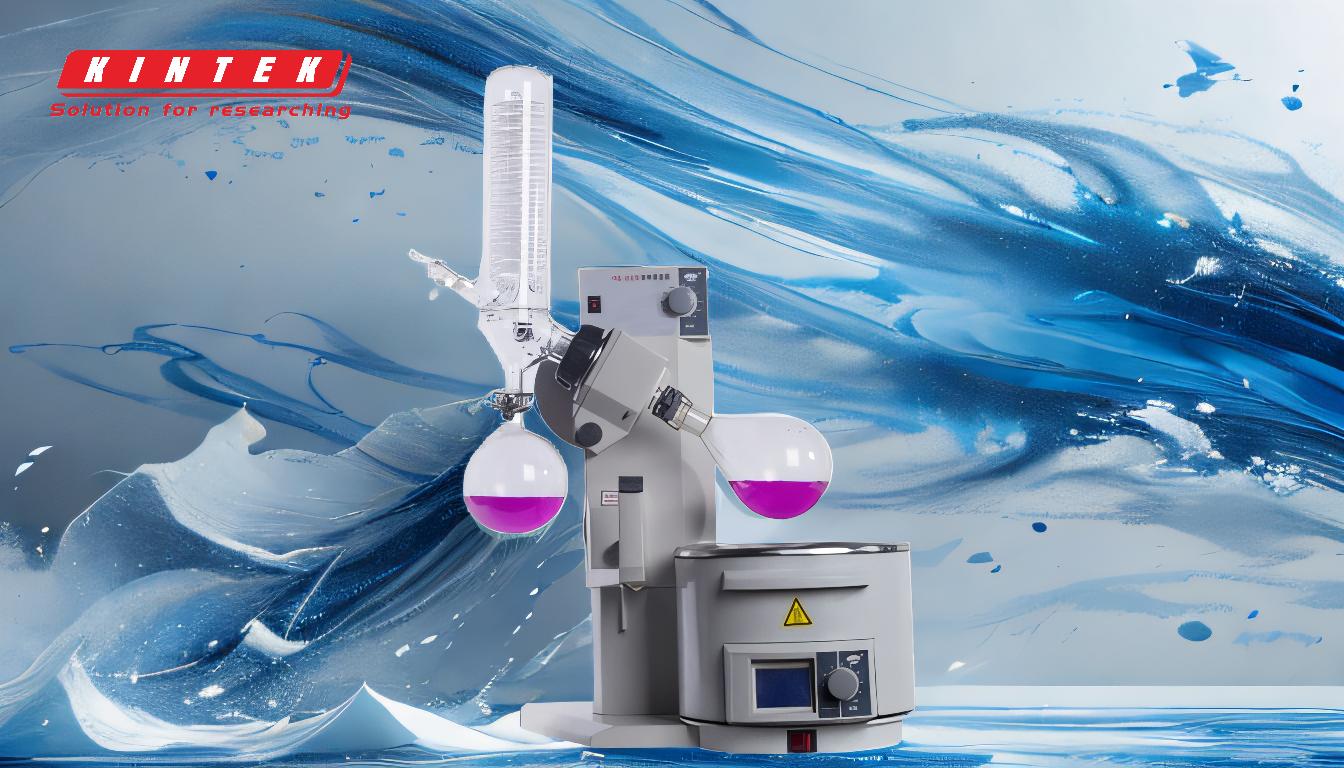
-
Vacuum Level Range:
- The vacuum level in a thermal evaporator typically ranges from 10^-5 to 10^-7 Torr (or 10^-7 to 10^-5 mbar).
- This range ensures a high vacuum environment, which is critical for the deposition process.
-
Importance of High Vacuum:
- Prevents Contamination: A high vacuum reduces the presence of residual gases (e.g., oxygen, nitrogen, carbon dioxide) that could contaminate the thin film, ensuring high purity and strong adhesiveness.
- Ensures Directional Deposition: At pressures around 10^-5 Torr, the mean free path of molecules is approximately 1 meter, allowing evaporated atoms to travel in a straight line from the source to the substrate without collisions. This ensures uniform and directional deposition.
- Maintains Film Quality: A high vacuum environment prevents unwanted interactions between evaporated atoms and residual gas molecules, which could otherwise weaken the film's adhesiveness or cause bonding with impurities.
-
Mean Free Path Considerations:
- The mean free path is the average distance an atom or molecule can travel before colliding with another particle. For effective thermal evaporation, the mean free path must be longer than the distance between the evaporation source and the substrate.
- A pressure of 3.0 x 10^-4 Torr or lower is typically required to achieve this condition. However, for optimal results, pressures in the range of 10^-5 to 10^-7 Torr are preferred.
-
Dependence on Material and Chamber Size:
- The specific vacuum level required can vary depending on the material being deposited and the size of the vacuum chamber.
- For example, some materials may require a higher vacuum (closer to 10^-7 Torr) to achieve the desired film quality, while others may tolerate slightly lower vacuum levels (closer to 10^-5 Torr).
-
Role in Resistive Evaporation:
- In resistive evaporation processes, a high vacuum is critical for two main reasons:
- Directional Deposition: It ensures that vapor molecules travel longer distances without colliding with gas molecules, leading to precise and uniform film deposition.
- Film Purity: It minimizes contamination from background gases, ensuring the deposited film remains pure and free of defects.
- In resistive evaporation processes, a high vacuum is critical for two main reasons:
-
Practical Considerations:
- Maintaining a high vacuum is not only about achieving the desired pressure but also about sustaining it throughout the deposition process. This requires a well-sealed vacuum chamber and efficient pumping systems.
- Running at the higher end of the pressure range (e.g., 10^-5 Torr) may allow for the simultaneous use of additional processes, such as ion beam sources, which can modify film properties like density or adhesion.
-
Impact on Thin Film Properties:
- A high vacuum ensures that the evaporated atoms stick well to the substrate, forming a stable and adherent layer. Without a high vacuum, the evaporated atoms might not adhere properly, leading to an unstable or poor-quality film.
- It also reduces the risk of oxidation or other chemical reactions that could degrade the film's performance.
In summary, the vacuum level of a thermal evaporator is a critical parameter that directly impacts the quality, purity, and performance of the deposited thin film. By maintaining a high vacuum environment (typically 10^-5 to 10^-7 Torr), the process ensures directional deposition, minimizes contamination, and enhances film adhesion and stability. The specific vacuum level required may vary depending on the material, chamber size, and desired film properties, but the overarching goal remains the same: to create a clean, controlled environment for high-quality thin film deposition.
Summary Table:
Key Aspect | Details |
---|---|
Vacuum Level Range | 10^-5 to 10^-7 Torr (or 10^-7 to 10^-5 mbar) |
Importance of High Vacuum | Prevents contamination, ensures directional deposition, maintains film quality |
Mean Free Path | Must exceed source-to-substrate distance for effective deposition |
Material Dependence | Specific vacuum levels vary based on material and chamber size |
Practical Considerations | Requires well-sealed chambers and efficient pumping systems |
Optimize your thin film deposition process—contact our experts today for tailored solutions!