Injection molding is a versatile manufacturing process used to produce a wide range of products across various industries. This method involves injecting molten material into a mold to create solid parts with high precision and repeatability. The products made through injection molding include everyday items like bottle caps and containers, as well as more complex components such as electronic housings, machinery parts, and agricultural equipment. The process is highly efficient, allowing for mass production of durable and intricate designs. Below, we explore the key categories of products that can be made using injection molding, along with their applications and significance.
Key Points Explained:
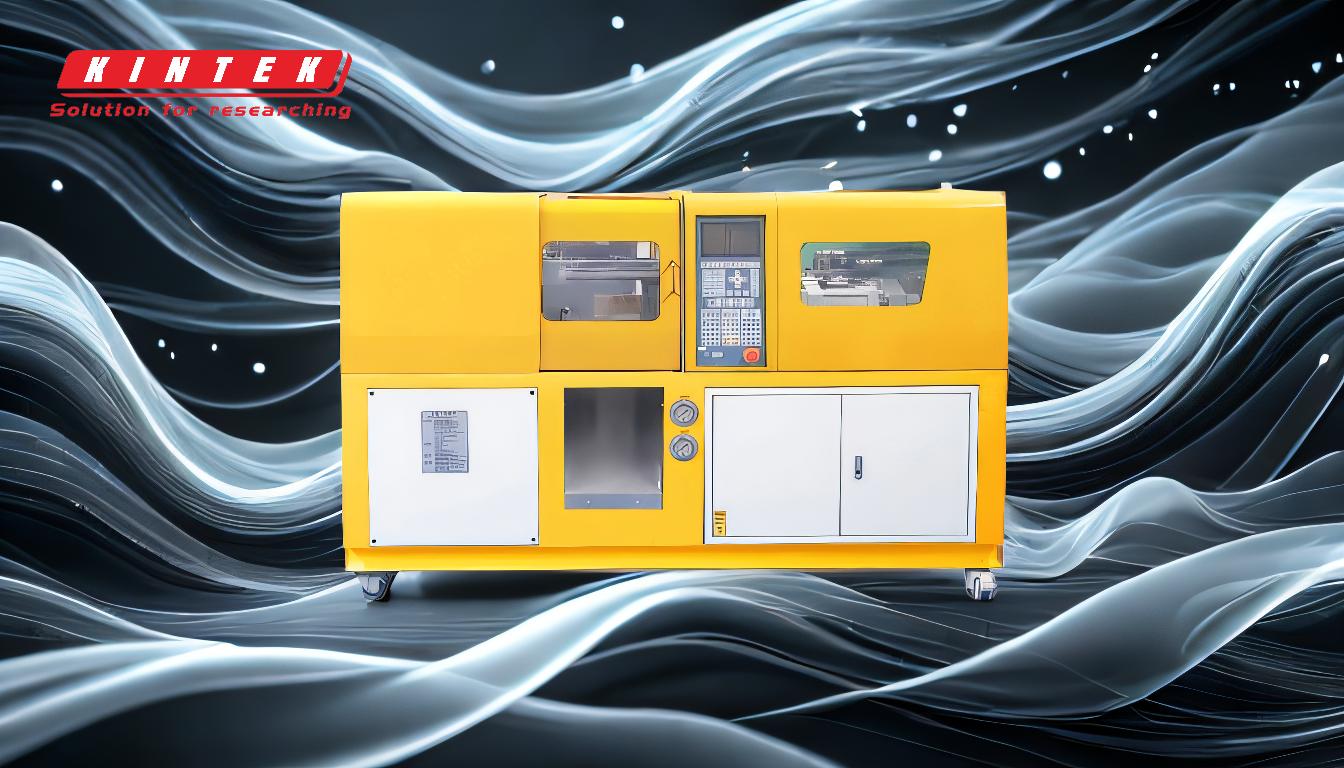
-
Electronic Housings and Components
- Injection molding is widely used to produce casings for electronic devices such as computers, televisions, and other consumer electronics.
- These housings are designed to protect sensitive internal components while providing a sleek and durable exterior.
- The process allows for intricate designs, including precise cutouts for buttons, ports, and ventilation.
- Materials like ABS (Acrylonitrile Butadiene Styrene) and polycarbonate are commonly used for their strength, heat resistance, and aesthetic appeal.
-
Bottle Caps and Containers
- Bottle caps and containers are among the most common products made through injection molding.
- These items require high precision to ensure proper sealing and functionality, especially in industries like food and beverage, pharmaceuticals, and cosmetics.
- Polypropylene (PP) and polyethylene (PE) are popular materials due to their flexibility, chemical resistance, and suitability for food contact.
- The process enables the production of lightweight, durable, and cost-effective solutions for packaging needs.
-
Outdoor Furniture
- Injection molding is used to create components for outdoor furniture, such as chairs, tables, and benches.
- These products are often made from materials like high-density polyethylene (HDPE) or polypropylene, which are resistant to weathering, UV radiation, and moisture.
- The process allows for the production of ergonomic designs and hollow structures, reducing material usage while maintaining strength and durability.
-
Agricultural Products
- Injection molding is employed to manufacture various agricultural tools and equipment, such as irrigation components, seed trays, and machinery parts.
- These products need to withstand harsh environmental conditions, including exposure to chemicals, sunlight, and mechanical stress.
- Materials like polyvinyl chloride (PVC) and polyethylene are chosen for their durability and resistance to degradation.
-
Toys
- The toy industry heavily relies on injection molding to produce a wide range of products, from action figures to building blocks.
- The process allows for the creation of detailed and colorful designs, ensuring safety and durability for children's use.
- Materials such as ABS and polypropylene are commonly used due to their non-toxic properties and ability to withstand rough handling.
-
Machinery Components
- Injection molding is used to produce precision components for machinery, including gears, housings, and connectors.
- These parts often require high strength, dimensional accuracy, and resistance to wear and tear.
- Engineering plastics like nylon, polyoxymethylene (POM), and polyetheretherketone (PEEK) are frequently used for their mechanical properties and thermal stability.
-
Automotive Parts
- The automotive industry utilizes injection molding for various components, such as dashboards, bumpers, interior trim, and under-the-hood parts.
- These parts need to meet strict safety and performance standards, including resistance to heat, chemicals, and impact.
- Materials like polypropylene, ABS, and polyamide (nylon) are commonly used for their strength, lightweight properties, and cost-effectiveness.
-
Medical Devices
- Injection molding is critical in the production of medical devices, including syringes, IV components, and surgical instruments.
- These products require high levels of precision, biocompatibility, and sterility.
- Materials such as polycarbonate, polypropylene, and medical-grade silicone are used to meet regulatory standards and ensure patient safety.
-
Consumer Goods
- A wide range of consumer goods, from kitchen utensils to household appliances, are manufactured using injection molding.
- The process enables the production of aesthetically pleasing and functional designs at a low cost.
- Materials like polypropylene and polystyrene are commonly used for their versatility and ease of processing.
-
Custom and Prototype Parts
- Injection molding is also used for creating custom parts and prototypes, allowing designers to test and refine their ideas before mass production.
- This application is particularly valuable in industries like aerospace, where precision and performance are critical.
- Advanced materials and rapid prototyping techniques can be employed to achieve high-quality results quickly.
In summary, injection molding is a highly adaptable manufacturing process capable of producing a diverse array of products across multiple industries. Its ability to create complex, durable, and cost-effective parts makes it an indispensable tool for manufacturers worldwide. Whether for everyday items like bottle caps or specialized components for machinery and medical devices, injection molding continues to play a vital role in modern production.
Summary Table:
Category | Examples | Key Materials | Applications |
---|---|---|---|
Electronic Housings | Casings for computers, TVs, etc. | ABS, Polycarbonate | Protects internal components, sleek designs with precise cutouts. |
Bottle Caps & Containers | Caps, bottles, pharmaceutical packaging | Polypropylene (PP), Polyethylene (PE) | Ensures sealing, lightweight, and cost-effective packaging. |
Outdoor Furniture | Chairs, tables, benches | HDPE, Polypropylene | Weather-resistant, ergonomic designs, and durable structures. |
Agricultural Products | Irrigation parts, seed trays | PVC, Polyethylene | Resists chemicals, sunlight, and mechanical stress. |
Toys | Action figures, building blocks | ABS, Polypropylene | Safe, durable, and colorful designs for children. |
Machinery Components | Gears, housings, connectors | Nylon, POM, PEEK | High strength, dimensional accuracy, and wear resistance. |
Automotive Parts | Dashboards, bumpers, interior trim | Polypropylene, ABS, Nylon | Heat, chemical, and impact resistance for safety and performance. |
Medical Devices | Syringes, IV components, instruments | Polycarbonate, PP, Medical-grade silicone | Biocompatible, sterile, and precise for patient safety. |
Consumer Goods | Kitchen utensils, appliances | Polypropylene, Polystyrene | Aesthetic, functional, and cost-effective designs. |
Custom & Prototype Parts | Aerospace components, prototypes | Advanced materials (e.g., PEEK) | Precision and performance testing for specialized industries. |
Unlock the potential of injection molding for your industry—contact us today to get started!