Inert gases, particularly argon, are widely used in sputtering due to their unique properties that make them ideal for the process. They are chemically inert, meaning they do not react with the target material or other process gases, ensuring a purely physical deposition process. Their high molecular weight contributes to higher sputtering and deposition rates, making the process more efficient. Additionally, inert gases do not decompose in the glow discharge, providing a stable source of ions for effective bombardment of the target material. Their use also prevents unwanted chemical reactions, such as oxidation or hydrolysis, which could degrade the sample.
Key Points Explained:
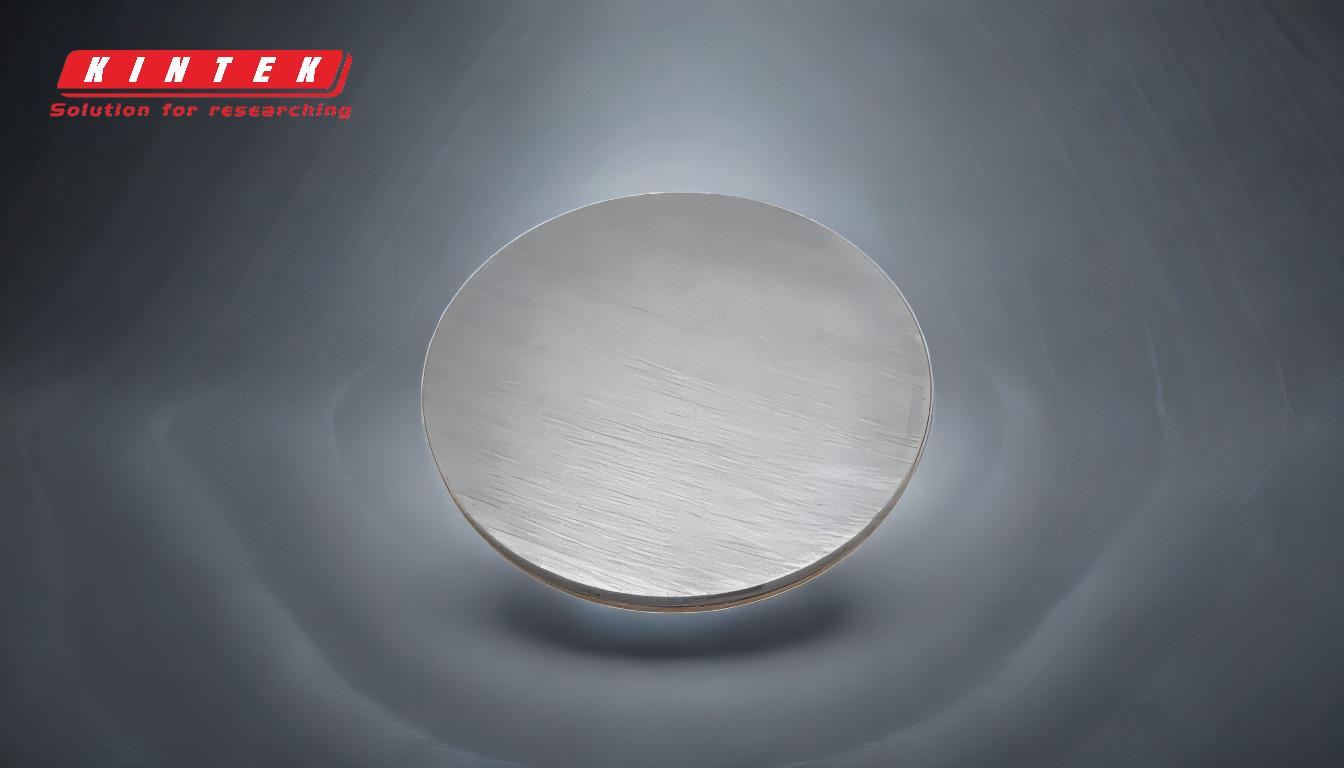
-
Chemical Inertness:
- Inert gases, such as argon, do not react with the target material or other process gases. This ensures that the sputtering process is purely physical, without any unwanted chemical reactions.
- This property is crucial for maintaining the integrity of the target material and the deposited film, as it prevents contamination and degradation.
-
High Molecular Weight:
- Inert gases like argon and xenon have high molecular weights, which enhances the sputtering and deposition rates.
- Higher molecular weight results in more efficient energy transfer during the bombardment of the target material, leading to faster and more effective sputtering.
-
Stability in Glow Discharge:
- Inert gases do not decompose in the glow discharge, providing a stable and consistent source of ions for the sputtering process.
- This stability is essential for maintaining a controlled and predictable sputtering environment, which is critical for achieving high-quality thin films.
-
Prevention of Unwanted Reactions:
- The use of inert gases helps to avoid undesirable chemical reactions, such as oxidation and hydrolysis, which can occur with reactive gases like oxygen or moisture in the air.
- By preventing these reactions, inert gases ensure that the deposited film remains pure and free from contaminants.
-
Facilitation of Plasma Formation:
- Inert gases are introduced into the chamber after creating a vacuum, providing a medium for plasma formation.
- The low-pressure environment ensures that the gas atoms only facilitate the sputtering process without introducing additional complexities or reactions.
-
Purely Physical Deposition:
- The use of inert gases ensures that the deposition process is purely physical, involving the transfer of material from the target to the substrate without any chemical changes.
- This is particularly important for applications where the chemical composition of the deposited film must remain unchanged.
In summary, the use of inert gases in sputtering is essential for maintaining a controlled, efficient, and contamination-free deposition process. Their chemical inertness, high molecular weight, stability in glow discharge, and ability to prevent unwanted reactions make them the ideal choice for this critical thin-film deposition technique.
Summary Table:
Property | Benefit |
---|---|
Chemical Inertness | Prevents unwanted reactions, ensuring a purely physical deposition process. |
High Molecular Weight | Enhances sputtering and deposition rates for greater efficiency. |
Stability in Glow Discharge | Provides a stable source of ions for consistent bombardment. |
Prevents Unwanted Reactions | Avoids oxidation or hydrolysis, maintaining film purity. |
Facilitates Plasma Formation | Enables plasma creation in a vacuum environment. |
Purely Physical Deposition | Ensures no chemical changes to the deposited film. |
Optimize your sputtering process with inert gases—contact our experts today for tailored solutions!