Sputtering is a widely used technique in materials science for depositing thin films of various materials onto substrates. While the process is commonly associated with metals, it can also be applied to non-metallic materials, including carbon. The sputtering process involves creating a vacuum, introducing an inert gas, applying a high voltage to ionize the gas, and using a magnetic field to direct the ionized gas toward a target material. This target material is then eroded, and its atoms are deposited onto a substrate. Carbon, in its various forms, can indeed be sputtered, although the process may require specific conditions and equipment to achieve the desired results.
Key Points Explained:
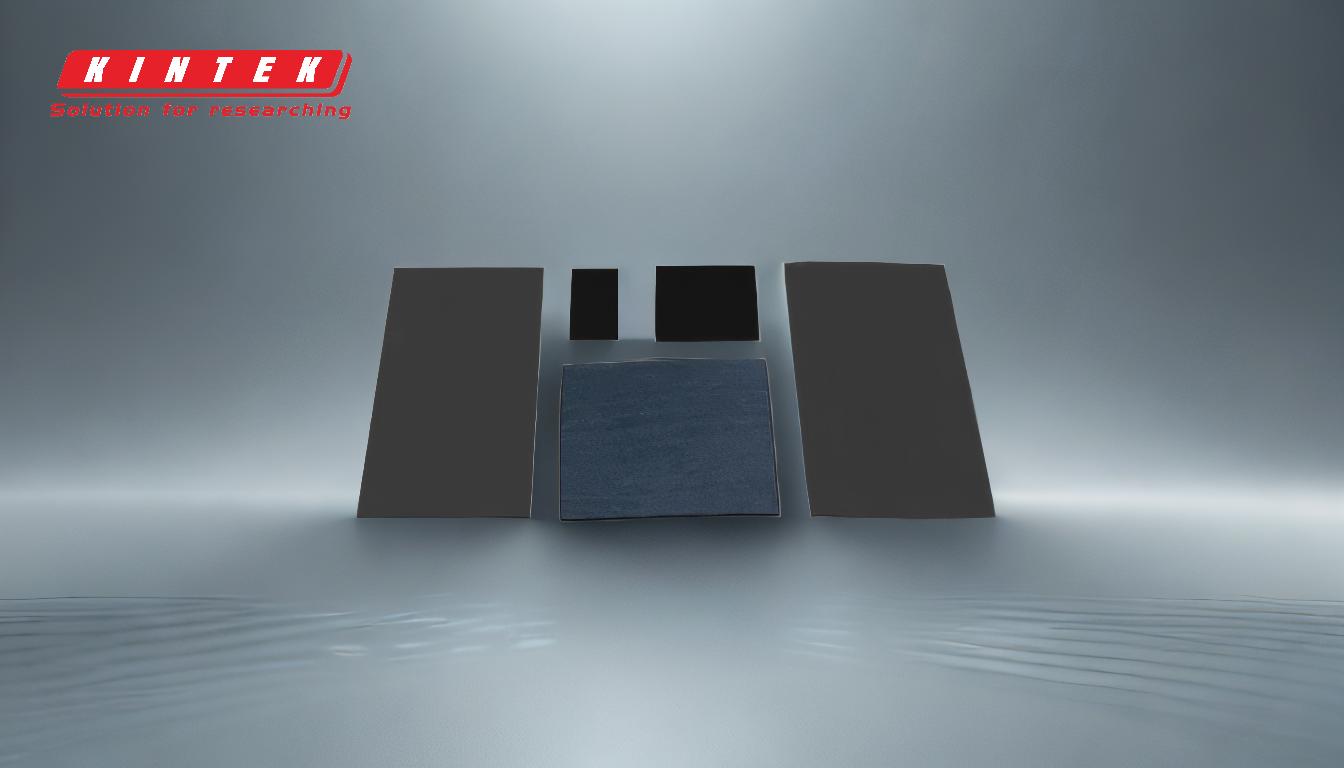
-
Vacuum Formation and Inert Gas Introduction:
- The first step in the sputtering process is to create a vacuum within the reaction chamber. This is crucial for removing moisture and other impurities that could interfere with the deposition process. The pressure is typically reduced to around 1 Pa.
- Once the vacuum is established, an inert gas, such as argon, is introduced into the chamber. Argon is commonly used because it is chemically inert and does not react with the target material or the substrate.
-
Heating the Chamber:
- The reaction chamber is then heated to temperatures ranging from 150°C to 750°C. This heating step is important for several reasons:
- It helps to further remove any residual moisture or contaminants.
- It can improve the adhesion of the sputtered material to the substrate.
- For some materials, including certain forms of carbon, heating can enhance the sputtering efficiency.
- The reaction chamber is then heated to temperatures ranging from 150°C to 750°C. This heating step is important for several reasons:
-
Magnetic Field and High Voltage Application:
- A magnetic field is created within the chamber by placing electromagnets around the target material. This magnetic field helps to confine the plasma and increase the ionization of the inert gas.
- A high voltage is applied to ionize the argon atoms, creating a plasma. The positively charged argon ions are then accelerated toward the negatively charged target material.
-
Target Material Erosion and Deposition:
- The positively charged argon ions collide with the target material, causing atoms or molecules to be ejected from the target. This process is known as sputtering.
- The ejected particles travel through the chamber and deposit onto the substrate, forming a thin film. In the case of carbon, this could result in a thin film of amorphous carbon, diamond-like carbon, or other carbon-based materials.
-
Sputtering Carbon:
- Carbon can be sputtered, but the process may differ slightly from sputtering metals. Carbon targets are often made from graphite or other carbon-rich materials. The sputtering of carbon can produce various forms of carbon films, depending on the conditions:
- Amorphous Carbon: This is a non-crystalline form of carbon that can be deposited at relatively low temperatures.
- Diamond-Like Carbon (DLC): This form of carbon has properties similar to diamond, including high hardness and low friction. DLC films are often deposited using a combination of sputtering and chemical vapor deposition (CVD) techniques.
- Graphene: While sputtering is not the most common method for producing graphene, it is possible to deposit thin layers of graphene using sputtering under specific conditions.
- Carbon can be sputtered, but the process may differ slightly from sputtering metals. Carbon targets are often made from graphite or other carbon-rich materials. The sputtering of carbon can produce various forms of carbon films, depending on the conditions:
-
Challenges and Considerations:
- Target Material: The choice of target material is critical. For carbon sputtering, high-purity graphite targets are often used to ensure the quality of the deposited film.
- Substrate Preparation: The substrate must be carefully prepared to ensure good adhesion of the carbon film. This may involve cleaning, heating, or applying a bonding layer.
- Process Parameters: The sputtering process parameters, such as pressure, temperature, and voltage, must be carefully controlled to achieve the desired film properties. For example, higher temperatures may be required to deposit diamond-like carbon films.
-
Applications of Sputtered Carbon Films:
- Protective Coatings: Carbon films, particularly diamond-like carbon, are used as protective coatings for tools, medical devices, and electronic components due to their hardness and low friction.
- Optical Coatings: Amorphous carbon films are used in optical applications, such as anti-reflective coatings and infrared optics.
- Electronics: Carbon films are used in various electronic applications, including as electrodes in batteries and supercapacitors, and as conductive layers in thin-film transistors.
In conclusion, carbon can indeed be sputtered, and the process involves creating a vacuum, introducing an inert gas, applying a high voltage, and using a magnetic field to direct the ionized gas toward a carbon target. The resulting carbon films can have a wide range of applications, from protective coatings to electronic components. However, the process requires careful control of parameters and may involve specific considerations depending on the desired form of carbon.
Summary Table:
Step | Description |
---|---|
Vacuum Formation | Create a vacuum (~1 Pa) to remove moisture and impurities. |
Inert Gas Introduction | Introduce inert gas (e.g., argon) to ionize and create plasma. |
Heating the Chamber | Heat chamber (150°C–750°C) to remove contaminants and improve adhesion. |
Magnetic Field & High Voltage | Apply a magnetic field and high voltage to ionize gas and accelerate ions toward the target. |
Target Erosion & Deposition | Erode target material (e.g., graphite) and deposit carbon atoms onto the substrate. |
Carbon Film Types | Amorphous carbon, diamond-like carbon (DLC), and graphene can be produced. |
Applications | Protective coatings, optical coatings, and electronic components. |
Interested in sputtering carbon for your applications? Contact our experts today to learn more!